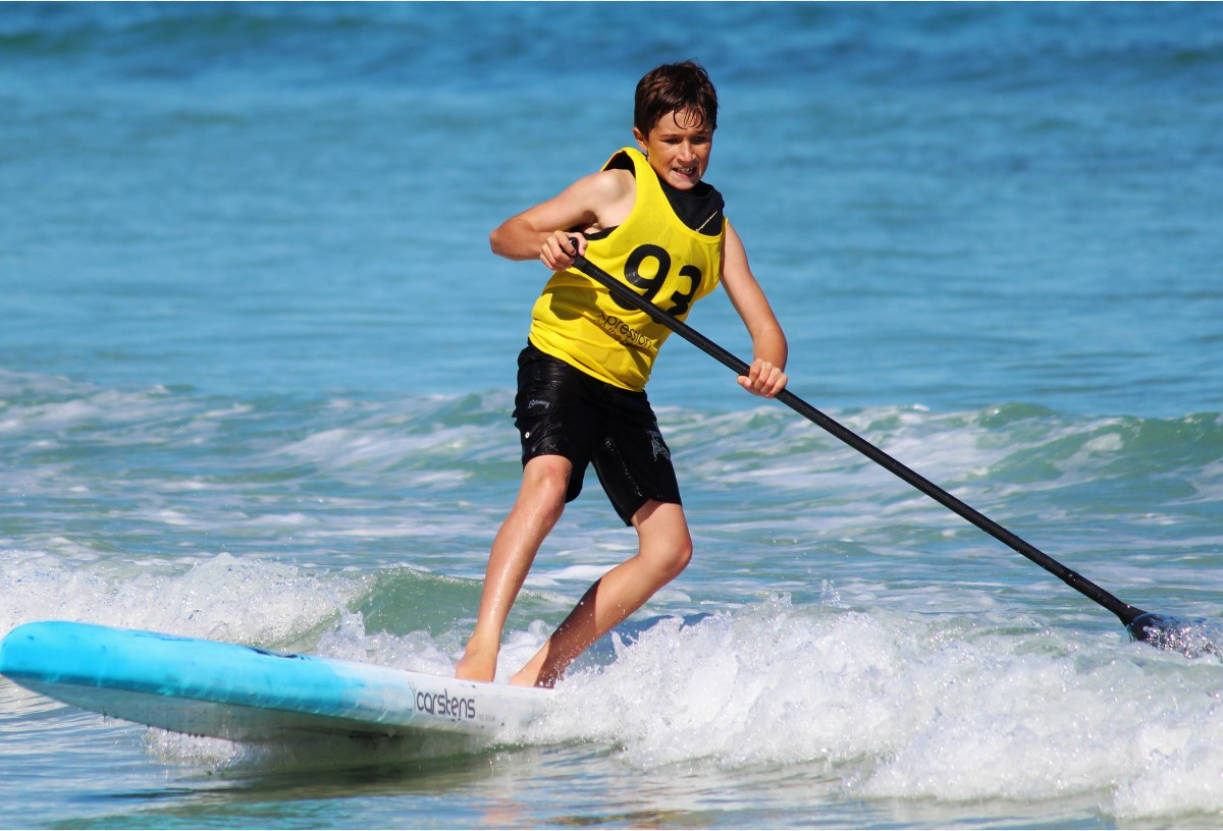
In global manufacturing and trade, product quality is critical to ensuring customer satisfaction, maintaining brand reputation, and minimizing costly returns. One of the most reliable methods to guarantee that every product meets the required standards is full inspection (also known as 100% inspection). This comprehensive inspection process ensures that every single item in a batch is carefully checked for defects, functionality, and compliance with specifications. In this article, we’ll explore the importance of full inspection, how it works, and why it’s a key component of any successful quality control strategy.
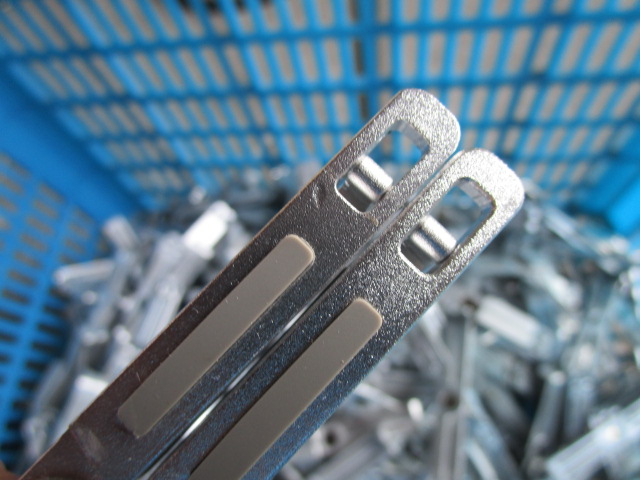
Contents
What is Full Inspection?
A full inspection, is a thorough and exhaustive quality control process where every product in a batch is individually inspected to ensure that it meets specific criteria, such as quality standards, safety regulations, and functional requirements. Unlike random sampling inspections, which examine only a portion of the production lot, full inspection ensures that no product is overlooked.
This method is commonly used for high-stakes industries where even a single defective product can result in serious consequences, such as consumer safety risks, regulatory non-compliance, or significant brand damage.
Why is Full Inspection Necessary?
- Ensuring Consistent Quality Across Every Unit
Full inspection guarantees that every product is free from defects and meets the required specifications. For manufacturers, this method ensures consistent quality across all units, preventing discrepancies that can affect product performance or customer experience. - Reducing the Risk of Defective Products Reaching Customers
A single defective product can lead to costly returns, legal issues, and loss of customer trust. By performing a full inspection, businesses can eliminate the risk of faulty products reaching customers, ensuring that only high-quality products are shipped. - Compliance with Regulatory Standards
Many industries, such as electronics, medical devices, and food products, have strict regulatory standards that products must meet before they are distributed to consumers. A full inspection ensures that each product complies with safety, environmental, and performance regulations, avoiding legal complications or penalties. - Building Customer Confidence and Trust
Consumers are more likely to trust brands that are known for delivering high-quality, reliable products. By conducting a 100% inspection, companies can showcase their commitment to quality, which helps build long-term customer loyalty and positive word-of-mouth marketing. - Reducing Costs in the Long Run
Although full inspection may involve higher upfront costs due to the need for labor and time, it can save significant amounts of money in the long run by preventing defective products from causing costly returns, product recalls, and reputational damage.
How Does Full Inspection Work?
The full inspection process typically involves a systematic examination of each product based on pre-determined criteria. Here’s how it generally works:
- Inspection Criteria Definition
Before conducting the inspection, it’s important to define what qualifies as a “defect” or “issue.” This includes specifications for appearance, dimensions, functionality, packaging, labeling, and safety features. Clear criteria ensure consistency and accuracy during the inspection. - Product Evaluation
Inspectors will evaluate every product individually. This includes visual checks for cosmetic defects, functional tests to ensure performance, and safety checks to verify compliance with industry standards. - Testing and Verification
For many products, especially complex ones, functional and performance tests are carried out during full inspection. This could involve stress tests, durability checks, safety tests, and verifying that the product performs as intended under various conditions. - Packaging and Labeling Checks
Inspectors also examine the packaging and labeling of products during full inspection to ensure that the items are properly packed and correctly labeled, as per the agreed-upon specifications and legal requirements. - Reporting and Documentation
After the inspection is completed, a detailed report is provided, highlighting any defects or non-conformities found during the inspection. This report serves as a critical reference for both the manufacturer and the buyer to ensure that corrective actions can be taken if necessary.
Benefits of Full Inspection
- Eliminates Risk of Product Defects
The most obvious benefit of full inspection is the elimination of defects. By inspecting every single product, businesses can catch defects early, reducing the risk of substandard products being sent to customers. - Improves Customer Satisfaction
When consumers receive products that are defect-free and function as expected, their satisfaction increases. Full inspection guarantees that products meet quality standards, leading to fewer complaints, fewer returns, and higher customer retention rates. - Increases Brand Reputation
Brands known for consistently delivering high-quality products often experience increased customer loyalty and enhanced market positioning. A 100% inspection program reinforces a company’s commitment to quality and sets it apart from competitors who may only use random sampling inspections. - Minimizes Legal Risks
For certain industries, such as healthcare, food, or electronics, failing to meet regulatory standards can result in legal repercussions, fines, or product recalls. A full inspection ensures that each product complies with industry-specific regulations, thus minimizing the risk of legal complications. - Cost-Effective in the Long Term
While full inspection requires more resources compared to sampling inspections, it is cost-effective in the long run because it prevents the expensive consequences of defective products, such as returns, recalls, or damage to the company’s reputation.
When Should You Opt for Full Inspection?
There are situations when opting for full inspection is particularly critical:
- High-Value Products
When dealing with high-value goods, such as luxury items or sensitive equipment, ensuring that each product meets the required standards is crucial. A full inspection reduces the risk of a costly mistake. - Safety-Critical Products
Products that are used in safety-critical environments, such as medical devices, pharmaceuticals, or automotive parts, should undergo full inspection to ensure they are free of defects that could lead to serious consequences. - Regulatory Compliance
Certain industries, such as electronics and food, require that every product meets strict regulatory guidelines. A 100% inspection ensures that every unit complies with the relevant laws and certifications. - Customer Demands for High Quality
If your customers demand the highest quality products, especially in competitive industries, full inspection is a must to maintain the desired level of quality control and protect your reputation.
Conclusion
A full inspection is an essential quality control method for ensuring that every product meets the highest standards before reaching the consumer. Whether you’re in the electronics, automotive, food, or any other industry, implementing a full inspection process helps reduce risks, improve customer satisfaction, and ensure compliance with regulatory standards.