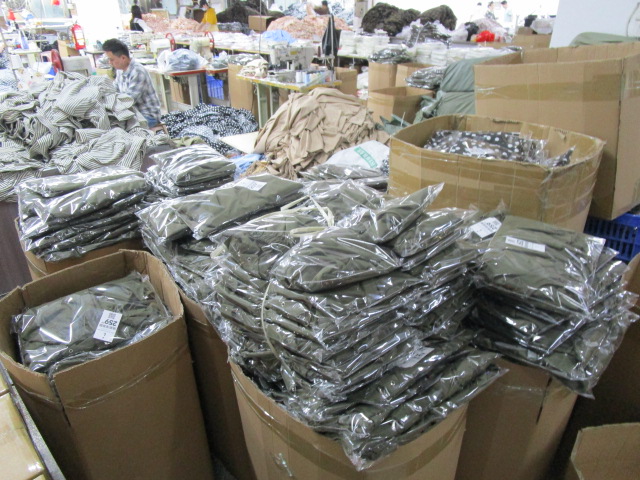
In the process of inspecting mechanical parts, it is very important to understand the two main processes for shaping metal into the desired shapes, which are: casting and forging. Each method brings unique characteristics, benefits, and applications, making them crucial in various industrial sectors. Here, we delve into the definitions, processes, types, and distinguishing factors of both casting and forging, providing insights into their roles in manufacturing.
Contents
Casting: A Versatile Process for Complex Shapes
Casting is a manufacturing process where metal is melted into a liquid state and poured into a mold, which contains a hollow cavity of the desired shape. Upon cooling and solidification, the metal takes the shape of the mold, resulting in a casting. This method is favored for its versatility in creating complex shapes and sizes, often unachievable through other manufacturing means.
Types of Casting
Casting can be broadly classified into two categories:
- Ordinary Sand Casting: Utilizes wet sand, dry sand, or chemically hardened sand for mold making. It’s the most common form due to its simplicity and cost-effectiveness.
- Special Casting: Employs unique materials for molds, including natural mineral sand and gravel (investment casting, mud casting, shell casting, etc.) or metals (metal casting, pressure casting, continuous casting, etc.). These methods are chosen for specific applications requiring finer details or particular material properties.
Casting Process Steps
The casting process involves several key steps:
- Mold Preparation: Crafting the mold is crucial, as its quality significantly impacts the casting’s final quality. Molds can be made from various materials and are categorized based on their reusability.
- Melting and Pouring: Metals are melted and poured into the molds. The choice of metal varies based on the application, ranging from cast iron and steel to non-ferrous alloys.
- Casting Processing and Inspection: After casting, the parts undergo processes to remove excess material and are inspected for quality assurance.
Forging: Enhancing Material Strength
Forging shapes metal using compressive forces, often applied through forging machinery. This process not only alters the metal’s shape but also enhances its structural integrity, making forged parts ideal for high-stress applications.
Types of Forging
Forging is categorized into:
- Open Forging (Free Forging): Metal is deformed between two anvils to achieve the desired shape, either manually or mechanically.
- Closed Die Forging: Metal is compressed in a die to obtain precise shapes. Techniques include die forging, cold heading, and more.
Forging Advantages
- Improved Mechanical Properties: Forging refines the metal’s grain structure, enhancing its strength and resistance to impact and fatigue.
- Material Efficiency: Forging typically results in less material waste compared to casting, as the process starts with closer to final shape sizes.
- Versatility in Materials: While both processes can work with a wide range of metals, forging is particularly effective with alloys known for their strength.
Key Differences Between Casting and Forging
- Manufacturing Technique: Casting involves melting metals into a liquid and pouring them into molds, while forging deforms the metal in solid state through compressive forces.
- Material Structure and Strength: Forged parts generally offer superior mechanical properties, such as strength and ductility, due to the compression and resultant grain refinement. Cast parts, while versatile in shape, may contain defects like porosity or inclusions.
- Cost and Complexity: Casting can produce more complex shapes at potentially lower costs, especially for intricate designs. Forging, though possibly higher in initial setup costs, provides parts with higher strength, making it cost-effective for demanding applications.
In conclusion, the choice between casting and forging depends on the specific requirements of the part, including its application, desired material properties, and complexity. While casting offers versatility in shape and complexity, forging excels in strength and material integrity. Understanding these differences helps manufacturers and engineers select the most appropriate method for their products, ensuring optimal performance and cost-efficiency.