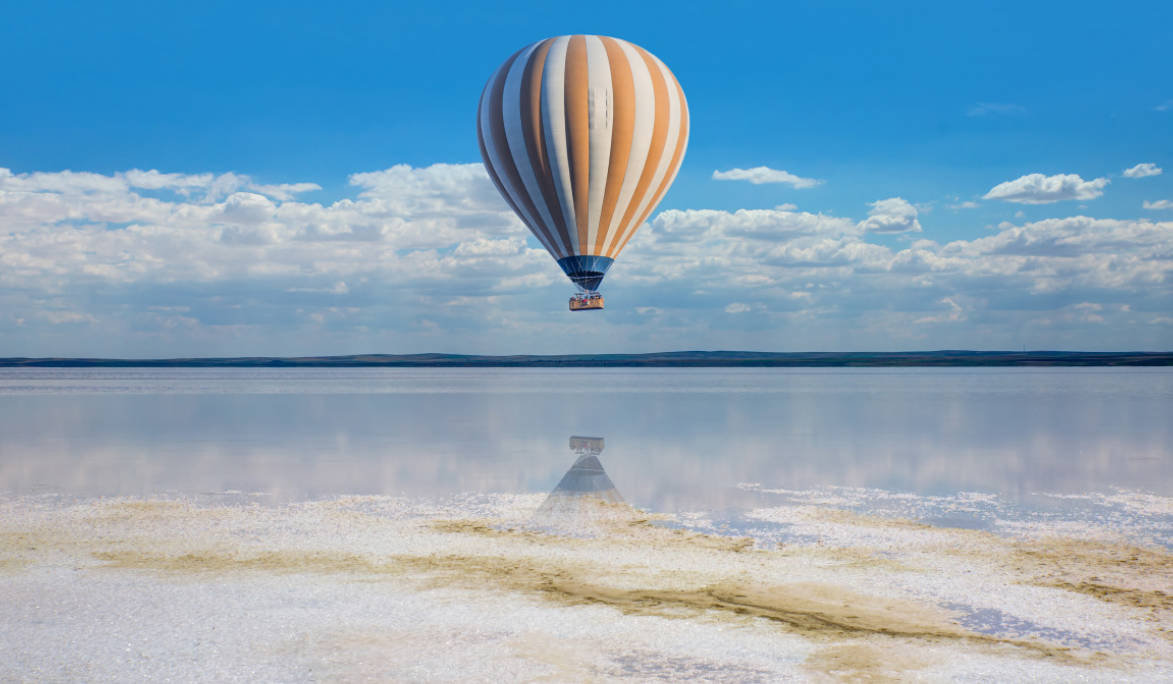
Factory audit services are critical for businesses seeking to ensure the reliability and quality of their supply chains. In China, where manufacturing is a global powerhouse, factory audits help companies verify compliance with industry standards and regulations.
From a broader perspective, factory audits serve as a strategic tool for mitigating risks and ensuring sustainability in the global supply chain. They help companies navigate complex regulatory environments, safeguard their brand reputation, and promote ethical business practices.
By providing a comprehensive evaluation of a factory’s operations, audits facilitate informed decision-making and foster long-term partnerships based on trust and transparency. This holistic approach not only enhances operational efficiency but also contributes to global economic stability by ensuring that manufacturing practices align with international standards and consumer expectations.
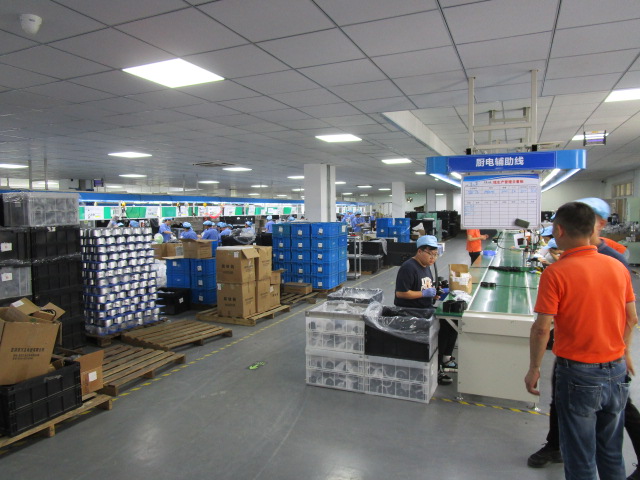
Contents
- 1 What is a Factory Audit?
- 2 Categories of Factory Audits
- 3 The Benefits of Factory Audits for Buyers
- 4 How Suppliers Can Prepare for a Successful Factory Audit?
- 5 Manufacturing Audit vs. Factory Audit
- 6 NBNQC’s Manufacturing Audit Process
- 7 Manufacturing Audit Application Scenarios
- 8 How to Get Started with Our Manufacturing audit Service?
What is a Factory Audit?
A factory audit is a systematic evaluation of a manufacturing facility conducted by an external party. This process involves inspecting various aspects of the factory, including its production capabilities, management systems, working conditions, and adherence to regulatory requirements. The goal is to ensure that the factory meets the standards necessary to produce goods of high quality, maintain ethical labor practices, and operate efficiently.
Categories of Factory Audits
Factory audits can be broadly categorized into several types, each focusing on different aspects of the manufacturing process:
- Quality System Audit: This type evaluates the factory’s quality management systems (QMS). It checks if the factory follows standardized procedures to ensure product quality, such as ISO 9001 compliance.
- Social Compliance Audit: This audit focuses on the factory’s adherence to labor laws and ethical standards. It covers aspects like working conditions, employee rights, health and safety, and compliance with local and international labor regulations. Standards like SA8000 or Sedex are commonly used.
- Environmental Audit: This audit assesses the factory’s environmental impact, including waste management, resource usage, and adherence to environmental regulations. It ensures that the factory operates sustainably and minimizes its environmental footprint.
- Production Capability Audit: This audit evaluates the factory’s production capacity, equipment, and technology. It ensures that the factory can meet the production volume and quality requirements of the buyer.
- Security Audit: Often conducted to ensure compliance with the Customs-Trade Partnership Against Terrorism (C-TPAT) standards, this audit examines the factory’s security measures to prevent terrorism and smuggling.
The Benefits of Factory Audits for Buyers
With increasing concerns about sustainability, labor practices, and regulatory compliance, buyers need to ensure their suppliers meet certain standards to mitigate risks and maintain brand integrity. Here explores the key benefits factory audits bring to buyers, covering aspects such as quality assurance, risk mitigation, supplier verification, regulatory compliance, and promoting ethical and sustainable practices.
1. Quality Assurance
One of the primary reasons buyers conduct factory audits is to ensure consistent product quality. A thorough audit evaluates the factory’s production processes, machinery, and quality control systems. This helps buyers confirm that the manufacturer can consistently produce goods that meet their specific quality standards. For businesses that rely on the timely delivery of high-quality products, this is crucial for maintaining customer satisfaction and brand reputation.
Factory audits examine various aspects of production, including raw material sourcing, employee training, production methods, and final inspection processes. By identifying areas for improvement or inconsistencies early on, buyers can avoid potential quality issues that might arise later in the supply chain, reducing the need for costly rework or product recalls.
2. Risk Mitigation
Factory audits serve as an effective tool for identifying and mitigating risks before they escalate into significant problems. Whether the risk is related to product quality, environmental practices, or compliance with labor laws, early detection through audits allows buyers to take corrective actions before issues affect production schedules or lead to financial losses.
For instance, if a factory is found to be using outdated equipment, there could be a higher risk of production delays or defects. Similarly, poor working conditions or non-compliance with local labor laws can lead to strikes, fines, or reputational damage, all of which can disrupt the supply chain. By conducting regular audits, buyers can preemptively address these risks, ensuring smoother production and minimizing disruptions.
3. Supplier Verification
Supplier verification is a vital aspect of building a reliable supply chain. Through factory audits, buyers can confirm that a factory is legitimate, financially stable, and capable of meeting production demands. In industries where product integrity and delivery timelines are crucial, working with unreliable suppliers can lead to significant operational and financial risks.
Factory audits not only assess the physical infrastructure of the supplier but also examine their management systems, certifications, and financial stability. By verifying these aspects, buyers gain confidence that the supplier can meet both current and future production requirements. This also helps establish long-term, trustworthy relationships with suppliers, reducing the risk of delays, product defects, or fraud.
4. Regulatory Compliance
Compliance with local and international regulations is critical for businesses that operate globally. Factory audits ensure that suppliers adhere to all necessary legal standards, including health and safety regulations, labor laws, and environmental requirements. Non-compliance can lead to legal penalties, supply chain disruptions, or even bans from specific markets, posing a significant risk to buyers.
An audit can help ensure that the factory meets necessary certifications, such as ISO standards, and complies with environmental and social regulations like REACH (Registration, Evaluation, Authorization, and Restriction of Chemicals) or RoHS (Restriction of Hazardous Substances). This guarantees that products are safe, sustainable, and legal, protecting both the buyer and their customers from potential liability.
5. Sustainability and Ethics
As consumers increasingly demand products that are ethically sourced and environmentally friendly, factory audits have become an essential tool for promoting sustainability and ethical practices. By auditing suppliers, buyers can ensure that their products are manufactured in conditions that respect labor rights and environmental standards.
This includes assessing factors such as fair wages, safe working environments, the prohibition of forced labor, and efforts to minimize environmental impact. Factories that implement sustainable practices, such as reducing waste, conserving energy, or minimizing water usage, contribute to the buyer’s broader corporate social responsibility (CSR) goals. In turn, buyers can market their products as ethically produced, enhancing brand reputation and consumer trust.
How Suppliers Can Prepare for a Successful Factory Audit?
1. Review Relevant Compliance and Quality Standards
Suppliers should familiarize themselves with the specific standards and regulations that will be audited, whether related to quality management (e.g., ISO 9001), environmental practices, or labor laws. Understanding these requirements helps identify areas where improvements are needed, reducing the risk of non-compliance during the audit.
2. Conduct Internal Audits
Before the official audit, it’s beneficial to conduct internal audits to assess the factory’s current state. These internal assessments should cover all areas of the audit scope, including production processes, record-keeping, employee training, and safety protocols. Internal audits provide an opportunity to address any weaknesses before the external audit takes place.
3. Organize Documentation
Auditors will expect to see comprehensive documentation during the audit. Suppliers should ensure that all required paperwork is up-to-date, complete, and readily accessible. This includes production records, quality control procedures, maintenance logs, safety inspection reports, and employee training records. Well-organized documentation not only saves time but also creates a positive impression.
4. Train Employees
Employees play a crucial role in audit success. Suppliers should provide training sessions to ensure that all workers understand their responsibilities, quality standards, and safety protocols. Employees should also be prepared to answer questions from auditors and demonstrate compliance during site inspections.
5. Maintain Cleanliness and Organization
A well-organized and clean factory environment is a reflection of good operational practices. Suppliers should ensure that their facilities are clean, well-maintained, and free from hazards. This not only improves safety but also positively influences the auditor’s perception of the factory’s management.
6. Address Previous Audit Findings
If the factory has undergone previous audits, suppliers should review any past findings or corrective action requests and ensure that these issues have been addressed. Demonstrating continuous improvement and responsiveness to previous audit feedback can result in a higher audit score.
Manufacturing Audit vs. Factory Audit
Manufacturing audits are comprehensive evaluations of a factory’s operations, designed to ensure compliance with quality standards, production capabilities, legal requirements, and other crucial criteria.
By identifying potential issues and providing actionable insights, manufacturing audits help factories maintain high operational standards and meet the demands of buyers and regulatory bodies.
Compared to specialized types of factory audits like Quality System Audits, Social Compliance Audits, Environmental Audits, and Production Capability Audits, manufacturing audits offer a broader and more integrated evaluation.
In contrast, a manufacturing audit encompasses all these aspects and more, providing a holistic view of the factory’s overall performance. This integrated approach allows for a more thorough understanding of the factory’s strengths and weaknesses, making manufacturing audits highly advantageous for ensuring comprehensive compliance and operational excellence.
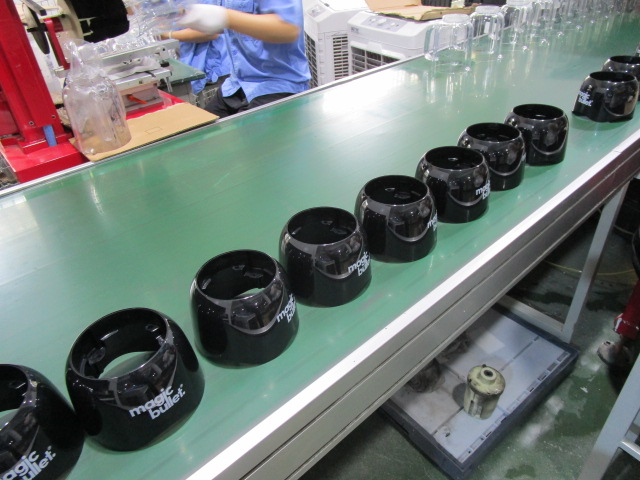
NBNQC’s Manufacturing Audit Process
Our auditors will conduct a comprehensive assessment of the designated factory to evaluate its capabilities, reliability, and legality. This thorough evaluation, performed in accordance with ISO 9000 Quality Management System standards, leads to a detailed factory rating.
Key Features of Our Audit:
1. Systematic Approach:
- Ensuring adherence to ISO 9000 principles for a structured and objective evaluation.
- Conducting an in-depth assessment of the factory’s operations, focusing on quality management and production capabilities.
2. Evaluation Criteria:
- Capabilities: Assessing the factory’s ability to meet production requirements consistently.
- Reliability: Evaluating operational reliability and stability.
- Legality: Verifying the factory’s legal status and compliance with relevant regulations.
3. Outcome:
- Providing a comprehensive factory rating based on audit findings.
- Offering clear insights into the factory’s operational standards, supporting informed decision-making for your business.
Key Audit Points
1.Factory Profile:
- Verification: Thoroughly verify the factory’s legal status and trade creditworthiness.
- Information Check: Ensure legitimacy and financial stability through essential documentation and records.
2. Human Resources:
- Organizational Structure: Assess detailed organization charts to understand the hierarchy.
- Workforce Distribution: Evaluate the distribution and skill level of staff across various departments to ensure adequate and qualified staffing.
3. Trade Capacity:
- Export Performance: Analyze the factory’s overall export performance.
- Product Range and Market Distribution: Detail the range of products and their distribution in global markets to gauge trade effectiveness.
4. Production Capability:
- Operational Information: Examine basic operational data.
- Raw Material Sourcing: Assess the sourcing of raw materials.
- Machinery and Equipment: Evaluate the condition and efficiency of machinery and equipment to determine production capacity.
5. Quality Control:
- Quality Control System: Scrutinize the existing quality control system and certifications.
- Supplier Management: Review practices for managing suppliers.
- Customer Complaint Handling: Evaluate procedures for handling customer complaints to ensure high standards of product quality and consistency.
6. Research and Development:
- Engineering Capabilities: Focus on the factory’s engineering capabilities.
- Sample Production Processes: Assess sample production processes and testing equipment.
- Innovation Potential: Highlight the factory’s potential for innovation and development.
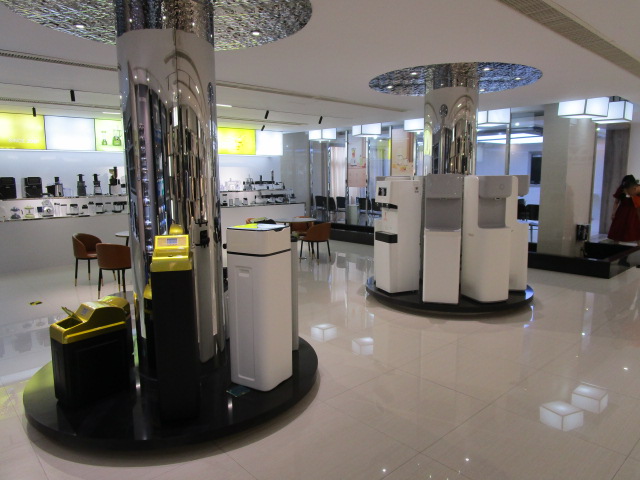
Manufacturing Audit Application Scenarios
- Pre-Collaboration Assessment: Before partnering with a new supplier, verify that they meet production capacity, quality management, and compliance standards.
- Ongoing Quality Verification: Regularly inspect the supplier’s quality management system to ensure consistent adherence to established standards.
- Risk Identification and Mitigation: Audit the factory’s production processes, equipment, and management to identify potential risks and implement measures to mitigate them.
- Contractual Compliance: Conduct periodic factory audits as required by contracts or agreements to ensure ongoing compliance.
- Brand Reputation Assurance: Ensure the supplier’s production conditions and management practices align with customer brand requirements, maintaining brand reputation and market competitiveness.
How to Get Started with Our Manufacturing audit Service?
Supplier Notification: We recommend that our clients notify suppliers at least 2 days in advance about the plan for a third-party manufacturing audit.
Client Booking: To schedule our audit services, simply fill out the NBN Booking Form and email it to us at [email protected]. We will promptly reply with a confirmation email. Our auditor will arrive at your designated factory within 36 hours.
Or Supplier Booking: It is also acceptable if the supplier sends us the booking form and CC the client in the email.
Payment: Upon booking acceptance, we will send you a proforma invoice via email. Payment is required before the audit date.
You Might Also Like
- Full Inspection In China
- Quality Inspection In China: Ensuring Product Excellence
- Quality Control In China
- Product Inspection In China: Ensure Consistent Quality And Compliance
- Navigating Quality Control: Understanding Pre-Shipment Inspection In China
- Third-Party Inspection In China: A Comprehensive Overview
- Container loading supervision in China