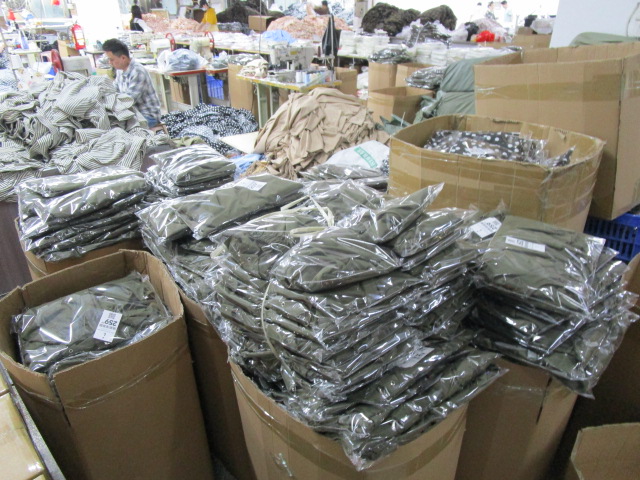
In the realm of product development and quality control, extensive testing plays a vital role in ensuring product consistency and durability. Through rigorous testing procedures, manufacturers can identify and address potential issues, improve product performance, and enhance customer satisfaction. This article delves into the relationship between extensive testing and the consistency and durability of products, highlighting the benefits of thorough testing methodologies.
1.Enhancing Product Consistency:
Extensive testing contributes significantly to achieving product consistency throughout the manufacturing process. Here’s how:
1.1 Identifying Manufacturing Variances:
Testing helps identify any variations that may arise during the production process. By subjecting products to multiple tests, manufacturers can detect inconsistencies in materials, dimensions, assembly, or finishing. This allows them to address these variations and establish standard operating procedures to ensure uniformity.
1.2 Evaluating Material Quality:
Through comprehensive testing, manufacturers can assess the quality and performance of materials used in product manufacturing. This includes analyzing the strength, durability, chemical resistance, and other relevant characteristics of the materials. By selecting high-quality materials, manufacturers can maintain consistency in product performance and longevity.
1.3 Validating Design Specifications:
Testing validates whether the product design meets the desired specifications. By conducting numerous tests, manufacturers can verify if the product functions as intended, performs optimally under various conditions, and meets the predetermined standards. This ensures that each unit produced adheres to the same set of specifications, enhancing overall consistency.
1.4 Assessing Production Processes:
Extensive testing allows manufacturers to evaluate their production processes and identify potential areas of improvement. By continuously monitoring and analyzing test results, manufacturers can identify any issues in the production line that may affect consistency. They can then make necessary adjustments, such as refining assembly techniques, implementing quality control measures, or training workers to ensure consistent output.
2.Ensuring Product Durability:
Extensive testing is crucial for ensuring the durability and longevity of products. Here’s why:
2.1 Identifying Weak Points:
By subjecting products to rigorous tests, manufacturers can identify potential weak points and vulnerabilities. This includes assessing the product’s resistance to environmental factors, stress, wear and tear, and other conditions it may encounter during its lifespan. Identifying weak points allows manufacturers to reinforce or redesign those areas to improve overall durability.
2.2 Evaluating Endurance:
Through extensive testing, manufacturers can simulate real-life usage scenarios and evaluate the product’s endurance. This includes subjecting the product to repeated cycles of stress, load, temperature variations, or other relevant factors. Testing endurance helps manufacturers determine the product’s expected lifespan and make necessary adjustments to enhance durability.
2.3 Improving Component Reliability:
Extensive testing not only focuses on the overall product but also on individual components. By testing each component independently, manufacturers can identify any weaknesses or failure points. This enables them to select more reliable components or develop improvements that increase the durability and longevity of the product.
2.4 Validating Performance Under Extreme Conditions:
Products may be exposed to extreme conditions during their usage, such as extreme temperatures, humidity, or mechanical stress. Through comprehensive testing, manufacturers can evaluate how the product performs under these extreme conditions. This allows them to make design modifications, select suitable materials, or implement additional protective measures to enhance the product’s durability.
Extensive testing is essential for achieving product consistency and durability. By subjecting products to rigorous testing procedures, manufacturers can identify variations, validate design specifications, assess production processes, identify weak points, evaluate endurance, improve component reliability, and validate performance under extreme conditions. This results in products that consistently meet customer expectations, perform reliably over time, and withstand the challenges of everyday usage. Through a commitment to extensive testing, manufacturers can enhance their reputation, build customer trust, and deliver products of the highest quality.
NBNQC provide quality control and inspection services in China, contact us if you need.