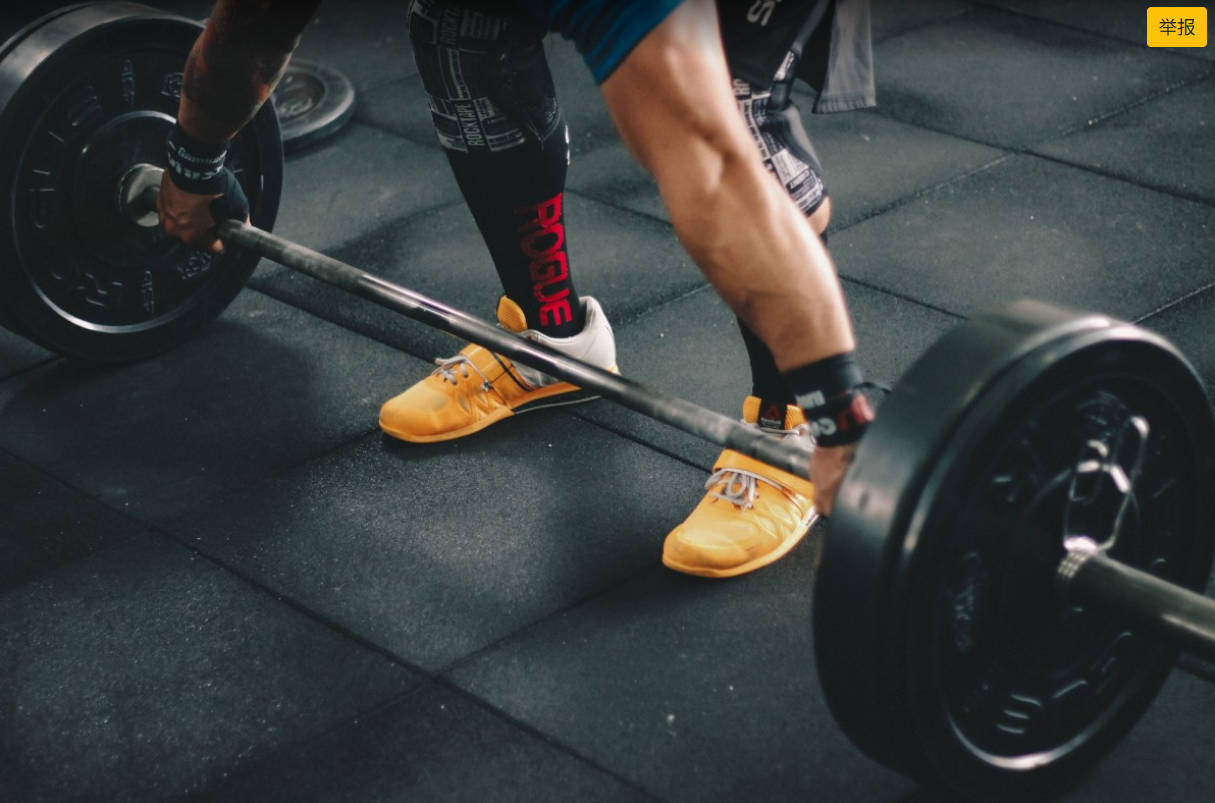
In the realm of purchasing inventory products, the decision to utilize third-party inspection services is often a pivotal one. Third-party inspection involves hiring independent professionals to assess the quality, quantity, and compliance of goods before they are accepted into inventory. This practice has both advantages and disadvantages, which must be carefully considered by businesses seeking to maintain quality control and mitigate risks in their supply chain.
Advantages:
- Unbiased Evaluation: Third-party inspectors offer an impartial assessment of products, free from any conflicts of interest that may arise from in-house or supplier-conducted inspections. This unbiased evaluation helps ensure objectivity in quality assessment.
- Expertise and Specialization: Third-party inspection agencies typically employ specialists with expertise in various industries and product categories. Their specialized knowledge allows for thorough and accurate evaluation, including identification of potential defects or compliance issues that might be overlooked by non-specialized inspectors.
- Risk Mitigation: By identifying quality issues or non-compliance early in the procurement process, third-party inspection helps mitigate risks associated with receiving substandard or non-compliant products. This proactive approach can prevent costly production delays, rework, or even legal ramifications resulting from the distribution of faulty goods.
- Supplier Accountability: Utilizing third-party inspection services sends a clear message to suppliers that quality is a priority. Suppliers are more likely to uphold quality standards and fulfill contractual obligations when they know that independent inspections will verify product integrity.
- Enhanced Reputation: Demonstrating a commitment to quality through third-party inspection can enhance a company’s reputation among customers, partners, and regulatory agencies. It signals a dedication to delivering reliable products and ensures compliance with industry standards and regulations.
Disadvantages:
- Cost: Third-party inspection services incur additional costs, including inspection fees and expenses related to arranging and coordinating inspections. These expenses can add up, particularly for businesses with large or frequent inventory purchases, potentially impacting profit margins.
- Time Constraints: Coordinating third-party inspections may introduce delays in the procurement process, especially when dealing with international suppliers or complex supply chains. Time-sensitive projects may face challenges if inspections prolong lead times beyond acceptable limits.
- Communication Challenges: Language barriers, cultural differences, and distance can sometimes hinder effective communication between third-party inspectors and suppliers. Misunderstandings or incomplete information exchanges may compromise the accuracy and reliability of inspection results.
- Limited Control: Despite thorough inspection protocols, businesses ultimately relinquish some degree of control over the inspection process to third-party agencies. This lack of direct oversight may lead to concerns regarding the consistency or comprehensiveness of inspections conducted.
- Dependency Risks: Over-reliance on third-party inspection services may create a dependency on external entities for quality assurance. If these services become unavailable or experience disruptions, businesses could encounter difficulties in maintaining consistent quality control standards.
Conclusion:
In conclusion, the decision to employ third-party inspection for purchasing inventory products involves weighing the benefits against the associated costs and challenges. While third-party inspection offers impartial evaluation, specialized expertise, and risk mitigation advantages, it also entails financial expenses, potential delays, and relinquishment of control. Businesses must carefully evaluate their specific needs, budget constraints, and risk tolerance to determine the most appropriate approach to quality control in their supply chain management. Ultimately, a balanced strategy that incorporates both internal quality assurance measures and selective use of third-party inspection can optimize product quality, mitigate risks, and safeguard the reputation and profitability of the business.