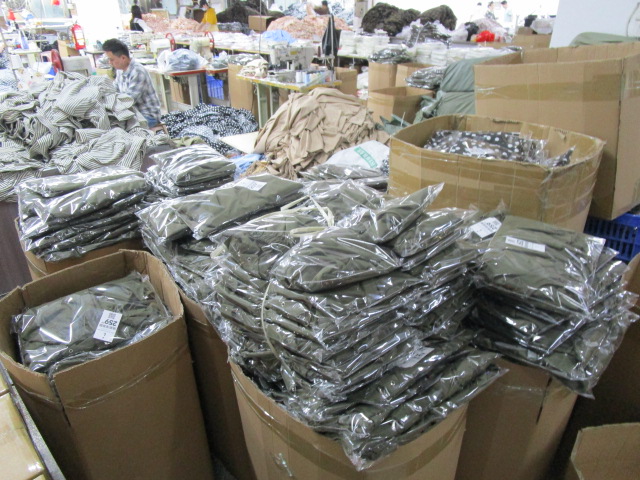
In the apparel industry, ensuring high-quality products is essential for customer satisfaction and brand reputation. Third-party inspection plays a vital role in this process by providing impartial and professional assessment of garment quality. In this article, we will explore the positive impact of third-party inspectors on comprehensive apparel quality control processes. Specifically, we will highlight the benefits of engaging third-party inspectors in clothing factories in China, where we, at NBNQC, offer apparel quality inspection services to our valued clients.
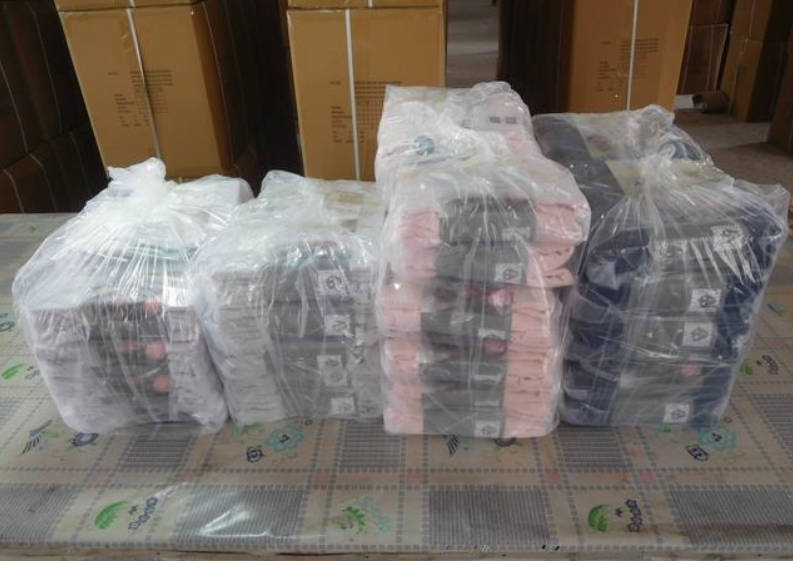
Contents
1.Impartial Assessment:
Third-party inspectors bring an unbiased perspective to the quality control process. By being independent of the manufacturer, they can provide objective evaluations without any conflicts of interest. Their impartial assessment helps maintain integrity and ensures that all quality aspects are thoroughly examined.
2.Compliance with Standards:
Third-party inspectors are well-versed in industry standards and regulations. They possess in-depth knowledge of quality criteria, such as fabric standards, stitching requirements, labeling regulations, and safety guidelines. Their expertise allows them to ensure that clothing products comply with relevant standards, minimizing the risk of non-compliance and potential legal issues.
3.Expertise in Quality Control:
With years of experience in the apparel industry, third-party inspectors have a deep understanding of quality control methodologies. They are familiar with various inspection techniques, sampling methods, and statistical analysis. Their expertise enables them to identify potential quality issues and recommend corrective actions to improve manufacturing processes.
4.Timely Feedback and Issue Resolution:
Third-party inspectors visit clothing factories and conduct inspections at different stages of production, including in-process and pre-shipment inspections. Their presence allows for real-time monitoring and immediate feedback on quality concerns. Manufacturers can promptly address any identified issues, preventing them from escalating and impacting product quality.
5.Supplier Evaluation and Improvement:
Engaging third-party inspectors provides an opportunity to evaluate and monitor suppliers’ performance consistently. Inspectors assess suppliers’ adherence to quality standards, production capacity, delivery schedules, and overall reliability. This evaluation process allows manufacturers to make informed decisions regarding supplier selection and collaboration, promoting long-term partnerships with reliable partners.
6.Customer Satisfaction and Brand Reputation:
By ensuring consistent quality, third-party inspectors contribute to enhancing customer satisfaction. By delivering high-quality products, manufacturers can build trust and loyalty with their customers. Positive customer experiences not only drive repeat business but also enhance brand reputation and facilitate market growth.
7.Risk Mitigation:
Third-party inspectors help mitigate risks associated with poor quality products. By identifying and rectifying quality issues before shipment, they help prevent the distribution of defective garments. This risk mitigation reduces potential product recalls, returns, and customer complaints, ultimately safeguarding manufacturers’ financial interests and brand reputation.
8.Continuous Improvement:
Third-party inspectors provide valuable insights and recommendations for process improvement. Their expertise allows them to identify areas where manufacturers can optimize their production processes, reduce defects, enhance efficiency, and achieve better quality control. This feedback fosters a culture of continuous improvement, leading to better manufacturing practices and higher product quality.
Engaging third-party inspectors in comprehensive apparel quality control processes brings numerous benefits to clothing manufacturers in China. Their impartial assessments, compliance expertise, and industry knowledge positively impact the entire production cycle, from raw materials to finished products. By partnering with trusted third-party inspection services like NBNQC, manufacturers can ensure consistent quality, mitigate risks, and enhance customer satisfaction, ultimately building a strong brand reputation in the global market.