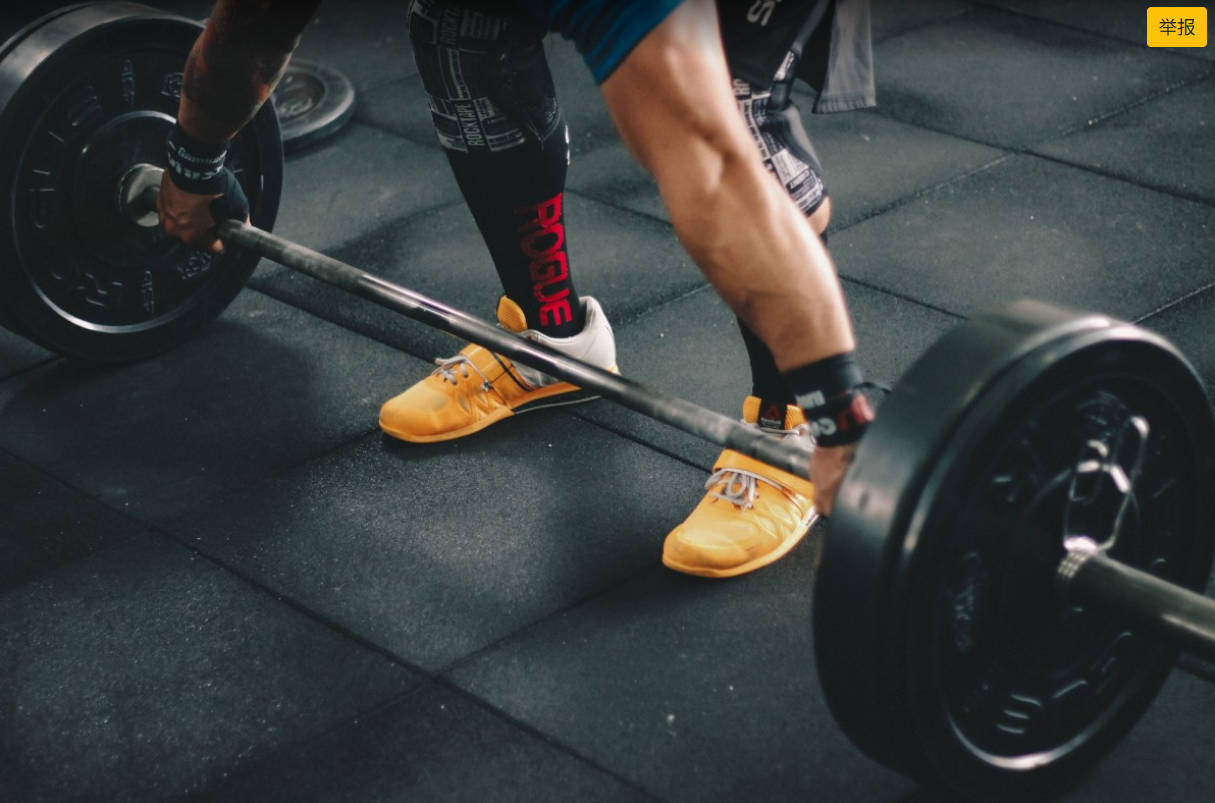
Electroplating is a crucial process used across various industries to enhance the surface properties of metal parts, such as corrosion resistance, wear resistance, aesthetic appeal, and electrical conductivity. Ensuring the quality of electroplated products is paramount to their performance and longevity. This article delves into the comprehensive inspection methods, international standards, and application-specific tests employed to ascertain the quality of electroplated components.
Contents
Visual Inspection
The initial step in quality inspection involves a thorough visual examination to detect any superficial defects like uneven coating, bubbles, cracks, scratches, impurities, or discoloration. This step is critical for ensuring the aesthetic quality of the product, especially for consumer goods and automotive parts where appearance is paramount.
Thickness Testing
The thickness of the electroplated layer is a key quality parameter that directly impacts corrosion resistance, wear resistance, and electrical properties. Techniques such as X-ray fluorescence (XRF) offer non-destructive measurement and are widely accepted for their accuracy and reliability. International standards like ASTM B568 and ISO 3497 provide guidelines for thickness measurements, ensuring consistency across industries.
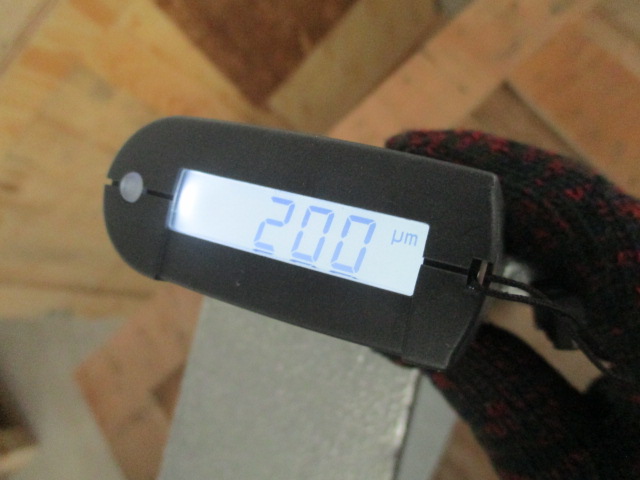
Adhesion Testing
Adhesion tests assess the bond strength between the electroplated layer and the substrate. Methods include the peel test, bend test, and thermal shock test. The ASTM B571 standard outlines several procedures for evaluating the adhesion of metallic coatings, ensuring that the plating will withstand the intended use conditions without delaminating.
Composition Analysis
Analyzing the chemical composition of the electroplating solution and the deposited layer ensures that the metal coating meets specified requirements. Spectroscopic analysis and electrochemical techniques are employed to measure element concentrations. Standards such as ISO 12608 provide guidance on the analysis of cyanide-free silver plating solutions, reflecting the industry’s move towards environmentally friendly processes.
Corrosion Resistance Testing
Corrosion resistance is vital for parts exposed to harsh environments. Salt spray testing (ASTM B117) and acid rain simulation are common methods for evaluating the durability of electroplated surfaces. These tests subject the coated parts to aggressive conditions to predict their lifespan and performance in real-world applications.
Hardness Testing
The hardness of the electroplated layer, indicative of wear resistance, is measured using Vickers or Rockwell hardness testing methods. The specific standards, such as ASTM E384 for microindentation hardness tests, ensure that the electroplated components can endure the wear and tear of their intended application.
Electrical Conductivity Testing
For electroplated parts used in electrical applications, testing for electrical resistance or conductivity is essential. This ensures that components like connectors and contacts meet the necessary electrical performance criteria.
Porosity Testing
Porosity tests, such as the copper sulfate test, are used to detect microscopic holes in the coating that can compromise corrosion resistance. This test is particularly relevant for parts used in marine and aerospace applications, where high corrosion resistance is required.
Application-Specific Tests
Depending on the part’s intended use, additional application-specific tests may be necessary. For instance, automotive parts may undergo vibration and impact testing to simulate operational stresses, while medical devices require biocompatibility testing to ensure they are safe for use in the human body.
Conclusion
Ensuring the quality of electroplated products is a multifaceted process that requires adherence to international standards and meticulous inspection methods. By employing a comprehensive quality inspection regime that includes visual inspection, thickness testing, adhesion testing, composition analysis, corrosion resistance testing, hardness testing, electrical conductivity testing, porosity testing, and application-specific assessments, manufacturers can guarantee that their electroplated components meet the rigorous demands of their application environments. This not only enhances the performance and durability of the products but also reinforces the reputation of manufacturers for producing high-quality, reliable components.