Within the global supply chain, China serves as a significant manufacturing hub, supplying a plethora of products and goods worldwide. However, with increasing consumer concerns over product quality and safety, coupled with the evolution of international trade, quality inspection have become paramount in China.
These services not only ensure that manufactured products meet expected standards and specifications but also provide customers with confidence and assurance that their purchases are safe and reliable.
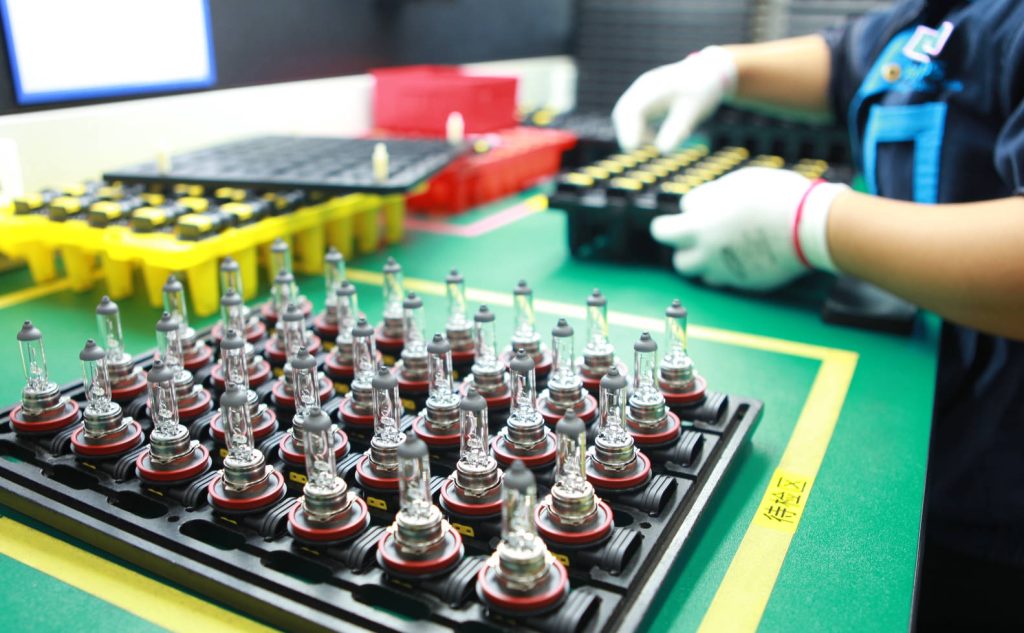
Contents
- 1 How do quality inspection in China benefit sellers?
- 2 Outsourcing Quality inspection vs. Hiring QC Staff in China: What’s Best for Foreign Buyers?
- 3 How Third-Party Inspection Companies Calculate Quality Inspection Costs
- 4 Benefits of the Man-Day Pricing Model
- 5 Components of a Man-Day Cost
- 6 Which Third-party Companies Can Provide Quality Inspection Service in China?
- 7 Ten Requirements for Products in Quality Inspection
- 8 What quality inspection services do third-party inspection companies offer?
- 9 How can we assist you?
- 10 Quality inspection
- 11 Container Loading Supervision
- 12 Factory Audit
How do quality inspection in China benefit sellers?
Quality inspection in China provide several benefits to sellers, especially those involved in exports or aiming to ensure products meet international standards. Here are some key ways quality inspection help sellers:
1. Ensuring Product Quality: Quality inspection ensure products meet expected quality standards and specifications. This helps avoid returns, claims, or customer dissatisfaction due to manufacturing defects or quality issues.
2. Risk Reduction: By conducting quality inspections during production, sellers can identify and address potential quality issues early, reducing the risk of products being returned or rejected. This helps save time and costs.
3. Compliance with Standards: Products exported to many countries need to meet specific quality standards and certifications. Quality inspection help sellers ensure products meet or exceed these standards, avoiding regulatory or certification issues in target markets.
4. Protecting Reputation: Providing high-quality products helps sellers maintain their brand reputation and customer trust. Regular quality inspections help build and sustain a positive corporate reputation.
5. Supply Chain Management: Quality inspection assist sellers in supervising various stages of the supply chain to ensure each step from raw materials to final products meets quality requirements, improving overall supply chain efficiency and reliability.
6. Increasing Sales: Offering high-quality products typically increases sales and customer satisfaction, leading to more business opportunities and growth.
Outsourcing Quality inspection vs. Hiring QC Staff in China: What’s Best for Foreign Buyers?
In the global marketplace, many foreign buyers engage in long-term procurement relationships with Chinese manufacturers. Ensuring product quality is paramount for these buyers to maintain their standards and meet customer expectations.
One key decision faced by such buyers is whether to employ a third-party inspection company or hire in-house Quality Control (QC) staff in China to oversee quality assurance. Each option comes with its own set of advantages and disadvantages, which should be carefully analyzed before making a decision.
How Third-Party Inspection Companies Calculate Quality Inspection Costs
Third-party inspection companies typically calculate quality inspection costs using the “man-day” method. This method charges a flat rate for each day an inspector spends on the job, covering all associated costs without hidden fees.
Benefits of the Man-Day Pricing Model
- Transparency: Clients receive a clear, all-inclusive price without hidden fees or unexpected charges.
- Simplicity: Simplifies the quotation process, making it easier for clients to understand and compare costs.
- Consistency: Provides a reliable cost reference for future inspections, helping clients budget and plan more effectively.
- Efficiency: Streamlines administrative processes, reducing the time and effort required to manage and process invoices and payments.
Components of a Man-Day Cost
A comprehensive man-day cost includes various detailed expenses:
1. Inspector’s Salary:
- Base Salary: The fundamental component, reflecting the inspector’s qualifications, experience, and expertise.
- Benefits and Insurance: This includes health insurance, retirement contributions, and other employment benefits.
- Overtime Pay: Additional compensation for work done beyond standard working hours.
2. Meals, Travel, and Accommodation:
- Meals: Daily allowances or reimbursements for meals consumed during the inspection period.
- Travel Expenses: Costs incurred for transportation, including airfare, train tickets, car rentals, fuel, and local transit.
- Accommodation: Expenses for lodging if the inspection site is far from the inspector’s home base, including hotels or other temporary housing.
3. Inspection Report Creation:
- Data Collection and Entry: Costs associated with gathering inspection data, taking photographs, and recording observations.
- Report Writing: The time and effort required to compile and write the inspection report, ensuring clarity and accuracy.
4. Inspection Report Review:
- Quality Assurance: Internal review processes to ensure the report meets quality standards and is free of errors.
- Technical Review: Verification by technical experts to confirm that all technical aspects of the inspection are accurately represented.
5. Additional Service Costs:
- Customer Service: Support provided to clients, including answering queries, addressing concerns, and providing updates.
- Scheduling and Coordination: Administrative efforts to schedule inspections, confirm dates, and coordinate logistics.
- Inspector Deployment: Arrangements for dispatching inspectors to various locations, ensuring timely and efficient deployment.
- Technical and Information Communication: Ongoing communication between inspectors, clients, and technical teams to ensure smooth operations and address any issues promptly.
6. Inspection Company’s Profit:
- Operational Margin: The profit margin necessary for the inspection company to cover its operational costs and remain financially viable.
- Investment in Technology and Training: Funds allocated for improving inspection technologies, training inspectors, and enhancing service quality.
- Business Development: Resources dedicated to marketing, sales, and expanding the company’s client base and service offerings.
Which Third-party Companies Can Provide Quality Inspection Service in China?
In China, quality inspection is crucial for the manufacturing and import businesses. To ensure that products meet both domestic and international standards and regulations, many companies rely on third-party quality inspection service providers. These companies have professional technical teams and advanced testing equipment to offer comprehensive quality control solutions to their clients. Here are some well-known third-party companies that provide quality inspection in China:
SGS Group: SGS is one of the leading global providers of inspection, testing, certification, and inspection services, with an extensive network and professional teams in China. Their services cover various stages from raw materials to finished products, including product testing, factory audits, and supply chain management.
TÜV Rheinland Group: As a renowned German quality certification organization, TÜV Rheinland offers comprehensive quality inspection and certification services in China. Their professional teams ensure that products comply with domestic and international standards, helping clients improve product quality and market competitiveness.
Bureau Veritas (BV) Group: BV Group is a global provider of inspection, verification, testing, and certification services, with multiple offices and laboratories in China. Their professional teams provide reliable quality control and risk management services to clients through strict inspection processes and advanced testing equipment.
Intertek: Intertek is a UK-based global quality inspection and certification company with years of experience and a good reputation in China. Their services cover various industries, including electronics, toys, and apparel, providing clients with comprehensive quality inspection and compliance assessment.
Bureau Veritas (French Classification Society): As a global inspection, certification, testing, and certification company with over a century of history, the French Classification Society also has a relatively complete service network in China, providing clients with quality inspection, supply chain management, and technical consulting services.
In addition, there are many trustworthy inspection companies in China that provide quality inspection. Here’s a carefully selected list of competitive inspection companies for your reference:
Num | Company | Services | Location | Contact |
01 | SGS | Product inspection, Testing & Certification, Training, Business Assurance, | Switzerland ,Beijing, Shanghai | https://www.sgsgroup.com.cn/en-cn |
02 | Intertek | Certification, assurance, testing, inspection | UK, Shengzhen | https://www.intertek.com/ |
03 | TUV SUD | Certification, testing, inspection, information and expert guidance | Germany/Beijing | https://www.tuvsud.com/en |
04 | BV | Certification, assurance, testing, inspection | France, Guangzhou | https://www.inspec-bv.com/ |
05 | QIMA | Testing, inspection, audit, certification, professional services, software solutions | Hong Kong | https://www.qima.com/ |
06 | Pro QC | Product quality, factory & supplier audits, management system audits | Shenzhen | https://proqc.com/ |
07 | V-trust | Quality Control, Lab Testing & Certificate, Supplier Evaluation | Guangzhou | https://www.v-trust.com/en/ |
08 | CICC | Inspection, Surveying, Testing, Calibration, Audit & Certification | Beijing | https://www.ccicsg.com/ |
09 | AQF | Inspection, Audit, Lab testing | Shenzhen | https://www.asiaqualityfocus.com/ |
10 | AQI | Product inspection, Factory audit, Value-Added Services, Product Testing & Certification | Hong Kong | https://aqiservice.com/ |
11 | HQTS | Quality Control Management, Audits, Compliance Testing | Fuzhou | https://www.hqts.com/ |
12 | TESTCOO | Inspection, Audit | Hangzhou | https://www.testcoo.com/en |
13 | VICC | Inspection, Audit, Lab testing, Engineering support, Certification & Consultation | Beijing | https://www.vicc.com/ |
14 | Novas QC | Inspection, Audit | Qingdao | https://www.novasqc.com/ |
15 | NBNQC | Inspection, Audit | Ningbo | https://www.nbnqc.com/ |
Ten Requirements for Products in Quality Inspection
In modern manufacturing, product quality inspection is a critical process to ensure that products meet quality standards and customer requirements. By implementing a systematic and standardized inspection process, product quality can be effectively controlled, enhancing customer satisfaction and market competitiveness. Here are ten specific requirements for products during quality inspection:
1. Dimensions and Tolerances
Accurate Dimensions: Each part of the product must be manufactured according to the dimensions specified in the design drawings. Dimensional accuracy directly impacts product assembly and performance.
Tolerance Range: The allowable dimensional variations must fall within the specified tolerance range. Setting tolerance ranges ensures consistency and interchangeability in mass production.
2. Appearance Quality
No Defects: The product surface should be free from visible scratches, dents, cracks, and other defects. Appearance quality not only affects the aesthetic appeal but also reflects potential issues in the manufacturing process.
Consistency: The color, texture, and other appearance characteristics of the product should be consistent, meeting design and customer expectations. Consistent appearance is a crucial part of the product’s brand image.
3. Performance Requirements
Function Testing: The product should operate normally and meet the designed functional requirements. This includes testing the basic functions and any additional features of the product.
Reliability Testing: The product should maintain reliable performance under various usage conditions, such as durability and stability. Reliability testing typically includes long-term operation tests and environmental stress tests.
4. Physical and Chemical Properties
Material Composition: The composition and quality of the materials used in the product must meet relevant standards, such as hardness, density, and conductivity. This ensures the product’s physical performance during use.
Chemical Properties: The product should exhibit expected resistance to corrosion, acidity, and alkalinity in specified chemical environments. Stability in chemical properties ensures the product’s lifespan in different environments.
5. Mechanical Performance
Strength and Hardness: The product should have sufficient strength and hardness to withstand expected usage loads. Mechanical performance testing typically includes tensile, compressive, and bending tests.
Elasticity and Toughness: The product should possess appropriate elasticity and toughness, allowing it to endure certain deformation during use without damage. Elasticity and toughness testing ensures the product’s stability under stress.
6. Electrical Performance
Electrical Safety: For electrical products, they must comply with relevant electrical safety standards, such as insulation performance and leakage protection. Electrical safety is essential to protect user safety.
Electrical Functionality: Electrical characteristics such as voltage, current, and power should meet design specifications. Electrical functionality testing ensures the normal operation and performance of the product.
7. Environmental Requirements
Non-Hazardous Materials: The product should not contain harmful substances such as heavy metals and VOCs (volatile organic compounds), complying with environmental standards. Meeting environmental requirements is a basic threshold for market entry.
Recyclability: The product should be designed to be recyclable or degradable to minimize environmental impact. Recyclability is a crucial aspect of sustainable development.
8. Safety
Usage Safety: The product should not cause harm to users during operation, complying with relevant safety standards. Usage safety is the primary consideration in product design and manufacturing.
Protective Measures: Products that may pose potential hazards should have appropriate protective measures, such as guards and safety locks. Protective measures are essential for ensuring user safety.
9. Applicability
Suitable Environment: The product should perform well under the designed environmental conditions, such as temperature, humidity, and pressure. Applicability testing ensures the product’s stable performance in various environmental conditions.
Compatibility: The product should be compatible with related equipment or systems, operating without faults. Compatibility testing ensures seamless operation in system integration.
10. Regulations and Standards
Compliance: The product must comply with the laws, regulations, and industry standards of the country or region where it is sold. Compliance is the basic prerequisite for legal market entry.
Certification Requirements: Some products may require specific certifications, such as CE certification or UL certification. Certification is the product’s passport to the international market.
By strictly adhering to these requirements, enterprises can establish a systematic and standardized quality inspection process, ensuring the stability and reliability of product quality. This not only helps enterprises gain market trust but also provides consumers with safe and reliable products.
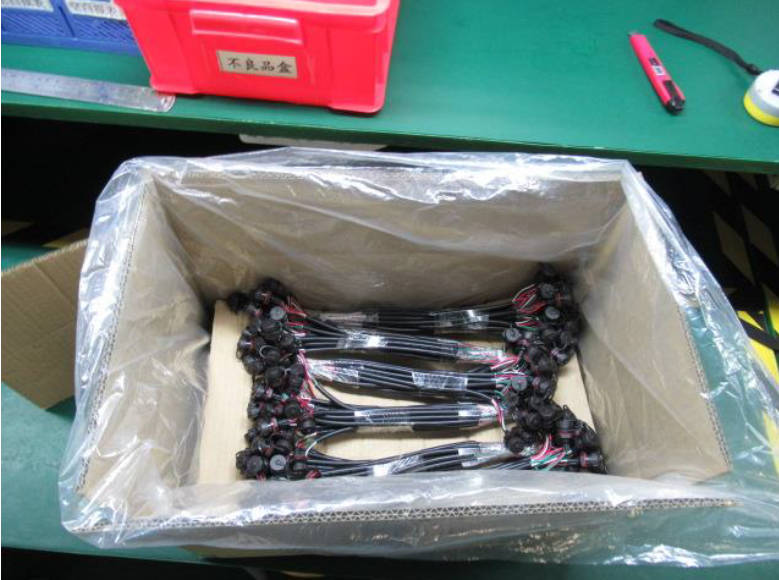
What quality inspection services do third-party inspection companies offer?
To ensure that products meet standards and customer expectations, an increasing number of companies are choosing to entrust third-party inspection companies to provide quality inspection services. These services span the entire production process, including initial production inspection, in-process inspection, pre-shipment inspection, full inspection, container loading supervision, and other stages, aimed at ensuring the quality of every critical aspect of the product.
Initial production inspection is conducted at the beginning of the production process to ensure that product manufacturing adheres to relevant standards and requirements from the outset. This stage typically involves inspection of raw materials, verification of production equipment, and preliminary review of the production process to identify and rectify potential quality issues, ensuring smooth production.
In-process inspection occurs during the production process to monitor quality control and management. Through regular inspections and audits, any quality issues in the production process can be promptly identified and corrected, ensuring consistent quality throughout production.
Pre-shipment inspection is the final quality check conducted before products are ready for shipment. This stage typically involves a comprehensive inspection of product appearance, dimensions, functionality, performance, etc., to ensure compliance with customer requirements and standards. Only products that pass pre-shipment inspection are allowed for shipment, ensuring that products do not encounter quality issues during transportation.
Full inspection involves a comprehensive examination of products, including visual inspection, dimensional inspection, functional testing, performance testing, etc. This stage ensures that every detail of the product meets relevant standards and requirements. Only products that pass full inspection are allowed to enter the market, ensuring product quality and customer satisfaction.
Container loading supervision involves monitoring and inspecting the packing and loading process of products. This stage typically includes checking packaging methods, loading procedures, as well as the quantity and quality of goods to ensure that products are not damaged or lost during transportation, and to ensure timely and safe delivery to the destination.
How can we assist you?
NBNQC, as a leading third-party inspection company in China, specializes in providing comprehensive quality inspection services to global clients. With extensive experience and expertise, we cater to the needs of various industries. Here’s how we can assist you:
Quality inspection
From raw materials to finished products, our inspection services can be conducted at any stage of production, without disrupting factory operations.
During Production Inspection(DPI)
Container Loading Supervision
Ensure accurate shipment of the correct goods in the right quantity, enhancing the safety of the transportation, while mitigating the risk of trade disputes and fraud. NBN’s inspectors will oversee the entire container loading process, providing you with secure and reliable transportation for your goods.
Factory Audit
We provide accurate data and images, giving you an in-depth understanding of every aspect of your suppliers, assisting you in selecting the most suitable ones, and ensuring that your supply chain in China is always in optimal condition.
Get Start with our Services
You Might Also Like
- Understanding Factory Audit Services In China
- Full Inspection In China
- Quality Control In China
- Product Inspection In China: Ensure Consistent Quality And Compliance
- Navigating Quality Control: Understanding Pre-Shipment Inspection In China
- Third-Party Inspection In China: A Comprehensive Overview
- Container loading supervision in China