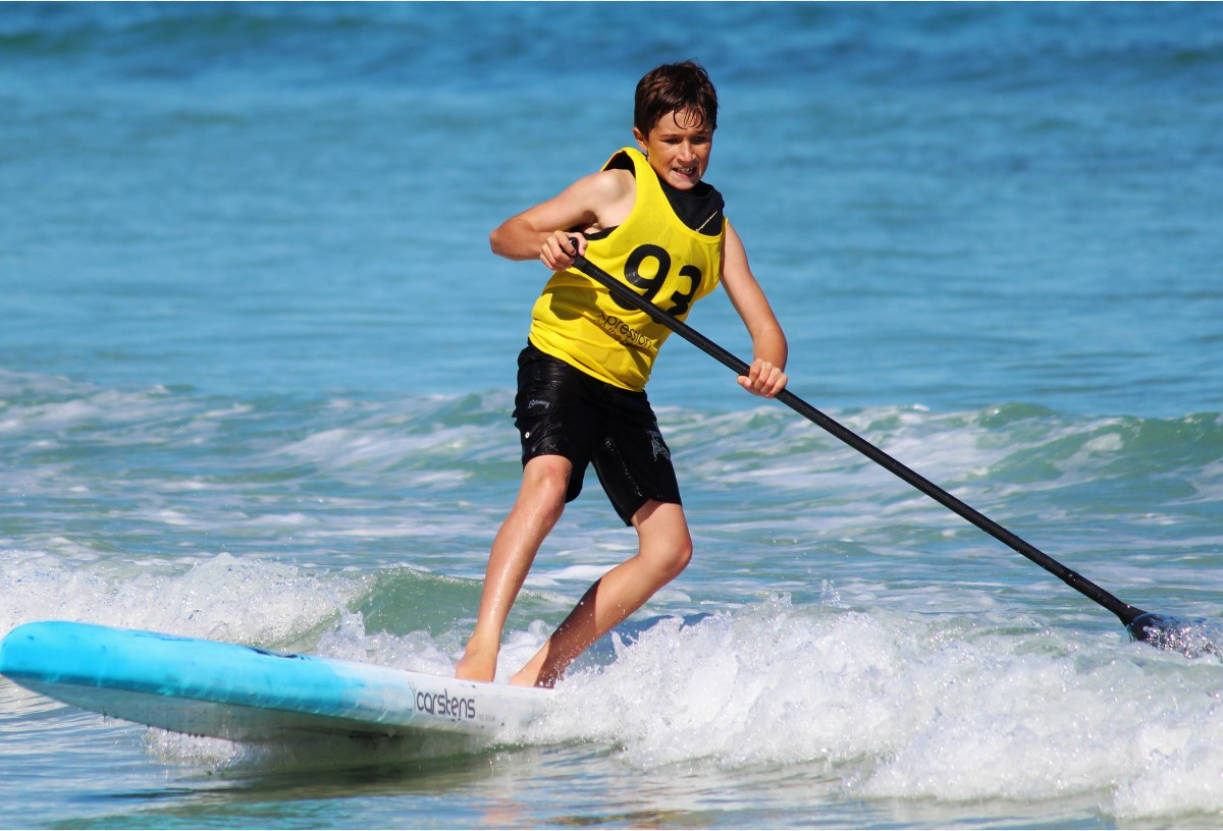
NBNQC collaborates with over 600 renowned global brands, importers and retailers, providing comprehensive quality control services for their supply chains in China. We ensure that every shipment meets quality requirements and safety standards.
Our inspection services cover a wide range of products, including but not limited to textiles, electrical appliances, toys, furniture, daily consumer goods, and hardware machinery.
Top Inspectors – We hire local inspectors, most of whom come from internationally recognized third-party inspection companies. Our team includes both full-time and part-time inspectors, we conduct detailed evaluations for every inspection to continually eliminate underperforming inspectors.
Competitive Pricing – By eliminating all unnecessary costs, we offer product inspections at just $209 per man-day and factory audits at only $239 per man-day.
Comprehensive Reports – Our inspection reports include everything you need to see, with detailed English descriptions and photos, we can also insert your checklists into the reports.
Efficient Operations – We can arrive on-site for inspections within 36 hours and submit reports within 18 hours after the inspection.
Flexibility – You can cancel or reschedule inspections for free before 10 AM (China Standard Time) the day before the scheduled inspection, and submit or modify related inspection requirements at any time before the inspection.
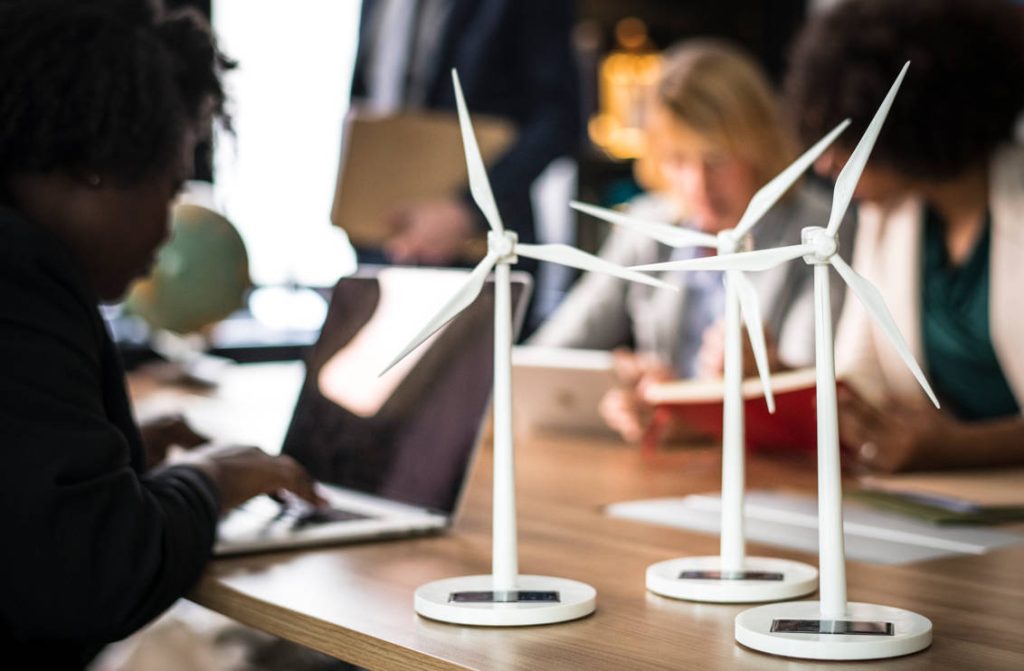
Contents
Quality Control and Inspection Services in China
Executing quality control and inspection services at factories in China is a challenging task, especially for new suppliers. Factors such as seasonal fluctuations, changes in raw material prices, supplier integrity, and the supplier’s quality control capabilities lead to inconsistent product quality between batches. This results in some orders not meeting customer requirements and even posing safety hazards to users.
Conducting quality control and inspection in China serves to protect consumers, buyers, and suppliers alike. Quality inspections can timely detect critical defects during the production process or before shipment, allowing enough time to implement rework or other corrective measures. This not only reduces quality risks but also helps maintain the cooperative relationship between buyers and sellers.
Five Major Mistakes Third-Party Inspection Agencies Should Avoid in Quality Control Processes
Third-party inspection agencies play a crucial role in ensuring product quality and compliance. However, they must be wary of several common pitfalls that can undermine their effectiveness. Here are five major mistakes that these agencies should avoid:
1. Inadequate Communication
Effective communication is vital for successful quality control. Failing to thoroughly communicate product details, inspection requirements, and inspection dates can lead to misunderstandings and missed inspections. Inadequate communication with clients and suppliers can result in incomplete inspections and overlooked quality issues.
2. Lack of Objectivity and Fairness
Inspection agencies must maintain objectivity and fairness in their evaluations. Yielding to supplier pressure or personal relationships can compromise the integrity of the inspection process. Bias and favoritism can lead to inaccurate reports, allowing substandard products to pass inspection and reach the market.
3. Inspector Complacency
Inspectors sometimes develop a false sense of security, especially if they have previously inspected similar products without issues. This complacency can lead to insufficient sampling and overlooked defects. Assuming that past performance guarantees current quality can result in significant quality control failures.
4. Vague and Incomplete Inspection Reports
Clear and detailed inspection reports are essential for effective quality control. Reports that are vague, unclear, or omit critical issues fail to provide an accurate representation of the product’s quality. Important problems that are not documented in the report may go unaddressed, leading to future quality and compliance issues.
5. Bribery
Corruption and bribery are serious concerns in the inspection industry. Accepting bribes to overlook defects or falsify reports undermines the entire quality control process. Bribery not only damages the reputation of the inspection agency but also puts consumers at risk by allowing substandard products to enter the market.
What can we do for quality control in China?
Factory audit: For new suppliers or annual evaluations of existing suppliers, our factory audit services provide accurate data and detailed images, giving you an in-depth understanding of every aspect of your suppliers. This information assists you in selecting the most suitable partners, ensuring your supply chain in China remains in optimal condition. By thoroughly assessing supplier capabilities and compliance, we help you mitigate risks and enhance overall supply chain reliability.
Initial Production Check: Conducted when 0-20% of the order quantity has been produced, this check offers reliable real-time information about the production site. It aids in closer collaboration with suppliers, facilitating the smooth completion of orders. Understanding these early details contributes to effective coordination with suppliers, enabling you to make informed decisions that enhance the production process and ensure quality outcomes.
During Production Inspection: When 20-80% of the order quantity has been produced, our inspectors provide detailed insights into the production conditions and essential information throughout the process. They meticulously examine raw materials, semi-finished products, production progress, and management practices to ensure they meet your quality requirements. This mid-production check helps identify and rectify issues early, maintaining high standards and preventing costly rework.
Pre-Shipment Inspection:Also known as Final Random Inspection, this is conducted when 80-100% of the order quantity has been produced. It is the last quality control process before goods leave the supplier’s factory or warehouse. The results of this inspection will help you make crucial decisions to accept, reject, or rework the products, ensuring only high-quality goods are shipped to your customers.
Full Inspection: Our full inspection service ensures a 100% pass rate by examining every product thoroughly. Passionate inspectors at NBN will meticulously check each item, helping you launch your brand to new heights by guaranteeing that only flawless products reach the market. This comprehensive approach eliminates the risk of defects and reinforces your commitment to quality.
Container Loading Supervision:Conducted during the container loading process, this inspection ensures the accurate shipment of the correct goods in the right quantities. By overseeing the entire loading process, NBN’s inspectors enhance the safety of transportation and mitigate the risk of trade disputes and fraud. This service provides you with secure and reliable transportation for your goods, safeguarding your investment and ensuring customer satisfaction.
Benefits of Our Quality Control Services
- Enhanced Supplier Reliability – Our services ensure you partner with the most reliable and capable suppliers, minimizing risks associated with new or underperforming suppliers.
- Consistent Product Quality – By implementing thorough inspections at various stages of production, we ensure that the quality of your products remains consistent, meeting your specifications and standards.
- Reduced Risk of Defects – Early detection of defects and issues during the production process helps prevent defective products from reaching the market.
- Improved Supply Chain Efficiency – Our real-time monitoring and detailed inspections help streamline the production process, ensuring timely delivery and reducing delays caused by quality issues.
- Informed Decision-Making – Accurate and comprehensive reports from our inspections provide you with valuable insights, enabling you to make informed decisions regarding supplier selection, production processes, and shipment logistics.
- Enhanced Customer Satisfaction – By ensuring high-quality products and reliable delivery, our services help improve customer satisfaction, fostering trust and long-term relationships with your clients.
- Reduced Risk of Trade Disputes and Fraud – Our oversight during the container loading process and other stages helps ensure the correct goods are shipped in the right quantity, reducing the risk of trade disputes and fraud.
- Cost Savings – By minimizing defects, avoiding rework, and ensuring timely deliveries, our quality control services contribute to significant cost savings in your supply chain operations.
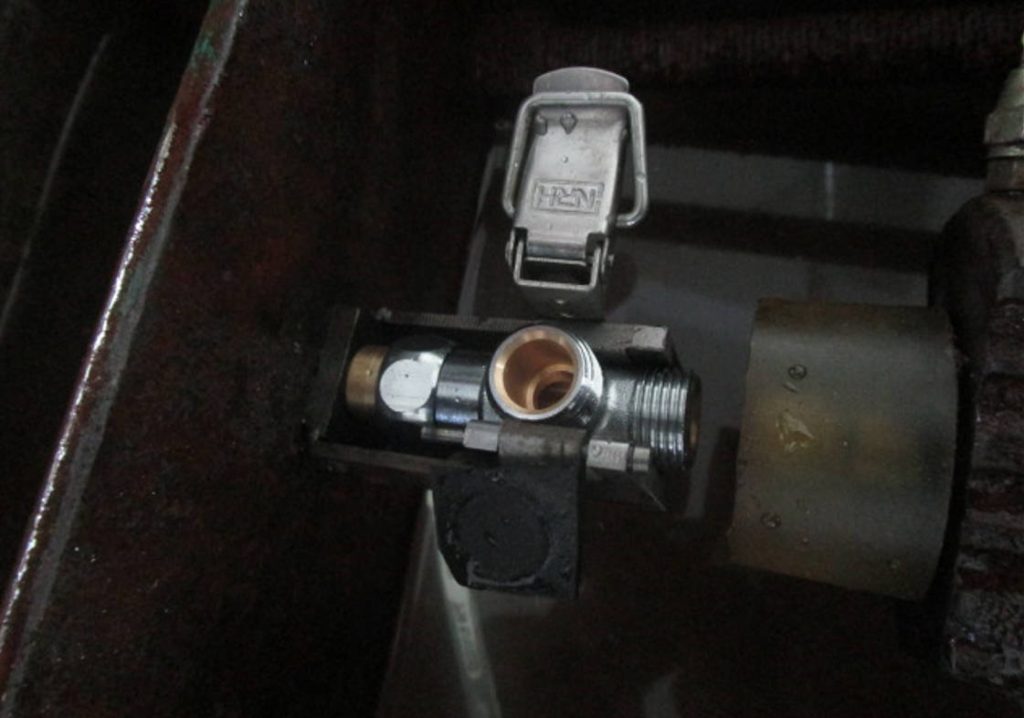
Our Quality Control Process and Inspection Points
NBNQC’s quality control process involves carefully verifying and inspecting each item according to the order/client’s requirements combined with our inspection checklist. Any defects or non-conformities will be objectively revealed, and our inspection report will comprehensively present the current status and detailed situation of the order.
Here are the inspection steps we typically use:
- Quantity
- Check the quantity of raw materials, only conducted when Initial production inspection
- Check the quantity of semi-finished products, only conducted when During production inspection
- Check the quantity of finished products
- Check the quantity of packed products
2. Product Conformity
- Style
- Color
- Materials
- Size & Weight
- Artworks & Label
3. Workmanship
- Based on the client’s specified sampling standards and AQL values.
- If these requirements are not provided, we will follow the corresponding industry general standards.
- After sampling, check all samples, categorize defective products, record the quantity, and take photos.
4. On-Site Testing
- Conduct tests specified by the client
- Conduct corresponding tests for the product. NBN testing guidelines
5. Packaging
- Packing condition, including the cleanliness, integrity, hardness, and humidity of the cartons
- Shipping marks and carton labeling
- Packaging method and product packing quantity
- Weight and dimensions of cartons
- Inner packaging inspection, including printing, labels, and integrity.
6. Communication & Report
- Communicate with the client on-site if there are special or urgent situations
- Issue the final inspection report
Download our Inspection Report
Get Start with our Services
You Might Also Like
- Understanding Factory Audit Services In China
- Full Inspection In China
- Quality Inspection In China: Ensuring Product Excellence
- Product Inspection In China: Ensure Consistent Quality And Compliance
- Navigating Quality Control: Understanding Pre-Shipment Inspection In China
- Third-Party Inspection In China: A Comprehensive Overview
- Container loading supervision in China