Pre-shipment inspection plays a vital role in the manufacturing and trading industry, particularly in the case of paper products. Ensuring that the quality and specifications of paper products are met before they are shipped to customers is essential for maintaining customer satisfaction and minimizing disputes. This article discusses the importance of pre-shipment inspection for paper products and outlines a comprehensive process to execute such inspections effectively.
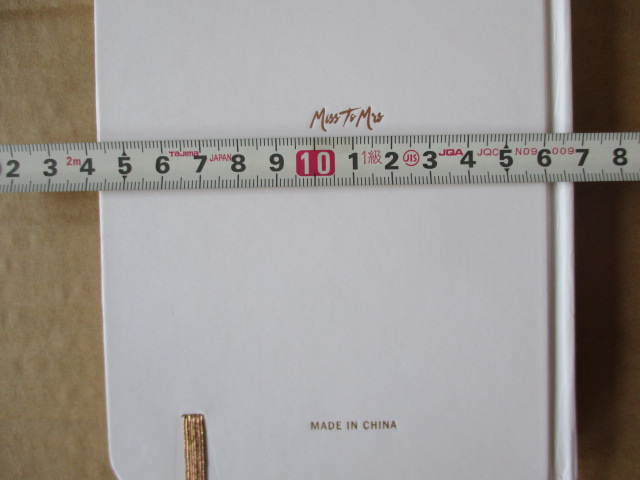
Contents
Importance of Pre-Shipment Inspection for Paper Products:
Pre-shipment inspection serves as a critical quality control measure that helps identify any defects, discrepancies, or deviations from the agreed-upon specifications before the products are dispatched to customers. In the case of paper products, which encompass a wide range including packaging materials, stationery, printing paper, and more, ensuring quality is paramount. Flaws in paper products can result in dissatisfied customers, increased returns, and damage to a company’s reputation. By conducting a thorough inspection prior to shipment, manufacturers and exporters can uphold the quality of their products, mitigate risks, and build trust with their customers.
Process of Pre-Shipment Inspection for Paper Products:
1.Establishing Inspection Criteria:
The first step in the process is to define the specific criteria that the paper products must meet. This includes factors such as size, weight, thickness, color, print quality, and any other relevant specifications. These criteria should be aligned with industry standards and customer expectations.
2.Selecting Inspection Samples:
Random sampling is a common method used in pre-shipment inspection. A representative sample is chosen from the batch to evaluate the overall quality of the entire lot. The sample size and selection process should be statistically significant to ensure accurate results.
3.Engaging Qualified Inspectors:
Trained and experienced inspectors with expertise in paper products should be assigned to carry out the inspection. These inspectors should have a keen eye for detail and be knowledgeable about the specific characteristics of various paper types.
4.Physical Inspection:
The inspection process involves a thorough examination of the selected samples. Inspectors should check for defects such as creases, tears, ink smudges, uneven cuts, and print clarity. For packaging materials, factors like adhesive strength and proper folding are crucial. The visual appeal and tactile quality of the paper should also be assessed.
5.Measurement and Testing:
Using calibrated measurement tools, inspectors should verify the dimensions, weight, and thickness of the paper products. For printing paper, print quality, color accuracy, and alignment should be tested. Additionally, if the paper products have specific performance attributes (e.g., water resistance, durability), relevant tests should be conducted.
6.Documentation:
Comprehensive documentation of the inspection process is essential. This includes photographs of defects, measurement records, and detailed notes on any deviations from the specified criteria. Proper documentation serves as evidence in case of disputes and facilitates effective communication between manufacturers and customers.
7.Reporting and Decision-Making:
Inspectors should compile their findings into a detailed report that outlines the inspection results for each sample. This report should include a clear statement of whether the batch meets the defined criteria or not. Based on this report, manufacturers can make informed decisions about whether to proceed with shipment, rectify the issues, or reject the batch.
8.Corrective Actions:
If the inspection reveals any discrepancies, manufacturers should take prompt corrective actions to address the issues. This might involve reworking the defective products, conducting additional quality checks, or even producing a new batch if necessary.
Some relevant international standard references for paper products:
In order to ensure the consistency and reliability of paper products, international standards are developed by the International Organization for Standardization (ISO):
1.ISO 216: Paper Sizes:
ISO 216 defines the widely recognized international paper sizes, including A4, A5, and A6. These standardized sizes facilitate document interchange and printing consistency across borders. The standard ensures that printed materials fit well on commonly used paper sizes, reducing waste and enhancing efficiency.
2.ISO 534: Determination of Thickness, Density, and Specific Volume:
ISO 534 outlines the methodology for measuring the thickness, density, and specific volume of paper and board. This standard is essential for maintaining the intended properties of paper products, such as thickness for printing compatibility and density for proper folding.
3.ISO 536: Determination of Grammage:
The ISO 536 standard specifies methods for determining the grammage (weight per unit area) of paper and board. It ensures that manufacturers adhere to defined weight requirements for different types of paper products, promoting consistency in their production.
4.ISO 187: Sampling and Cutting of Test Pieces:
This standard, ISO 187, provides guidelines for obtaining representative samples from paper and board and cutting them into test pieces. Effective sampling is critical for accurate quality assessment and conformity testing.
5.ISO 12625: Tissue Paper and Tissue Products:
For hygiene and everyday use, ISO 12625 sets requirements for tissue paper and related products. It covers factors like tensile strength, absorption capacity, and softness, ensuring these products meet consumer expectations.
6.ISO 14021: Self-Declared Environmental Claims:
ISO 14021 pertains to environmental labeling and self-declared environmental claims. Although not specific to paper products, it can apply to them. Manufacturers can use this standard to make credible environmental claims about their products, fostering transparency and environmentally conscious consumer choices.
7.ISO 9706: Requirements for Permanence:
In the realm of archival and long-term preservation, ISO 9706 establishes requirements for paper used in documents that need to stand the test of time. This standard ensures that paper products maintain their physical and chemical properties over extended periods, enhancing their archival quality.
8.ISO 18916: Imaging Materials – Albums, Framing, and Storage Materials:
ISO 18916 addresses the protection of photographs through requirements for albums, framing materials, and storage. This ensures that precious memories captured on paper are preserved in optimum conditions, safeguarding their longevity.
9.ISO 186: Sampling to Determine Average Quality:
ISO 186 provides guidance on sampling paper and board to determine average quality. This standard is crucial for manufacturers to gauge the overall quality of their products and maintain consistency across production batches.
Conclusion:
In the competitive world of paper product manufacturing and trading, maintaining consistent quality is paramount. Pre-shipment inspection serves as a crucial step in ensuring that paper products meet the required standards and specifications before they reach the customers. By following a well-defined process of establishing criteria, selecting samples, engaging qualified inspectors, conducting thorough inspections, and taking corrective actions, manufacturers can uphold their reputation, build customer trust, and drive the success of their business in the long term.