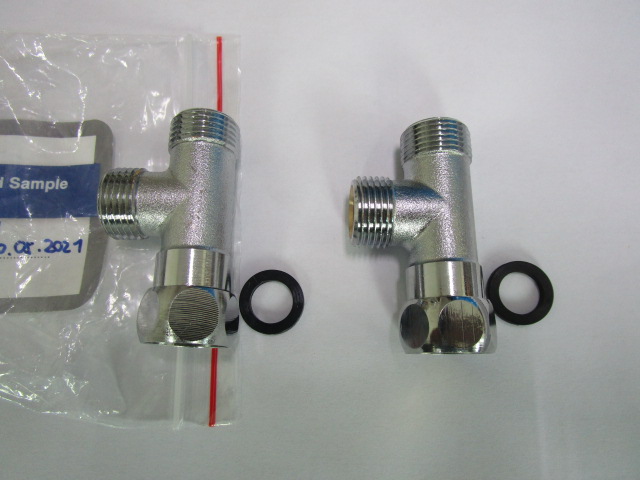
NBNQC is a renowned quality control service provider in China, specializing in conducting inspections for international buyers to ensure that goods manufactured in Chinese factories meet delivery standards and compliance requirements. In this article, we will discuss the comprehensive checklist used for flashlight inspections and provide insights into our testing procedures.
Contents
1.Flashlight Quality Control Checklist:
To ensure the highest quality standards for flashlights, NBNQC follows a meticulous checklist that encompasses various aspects of flashlight production. The checklist includes the following key points:
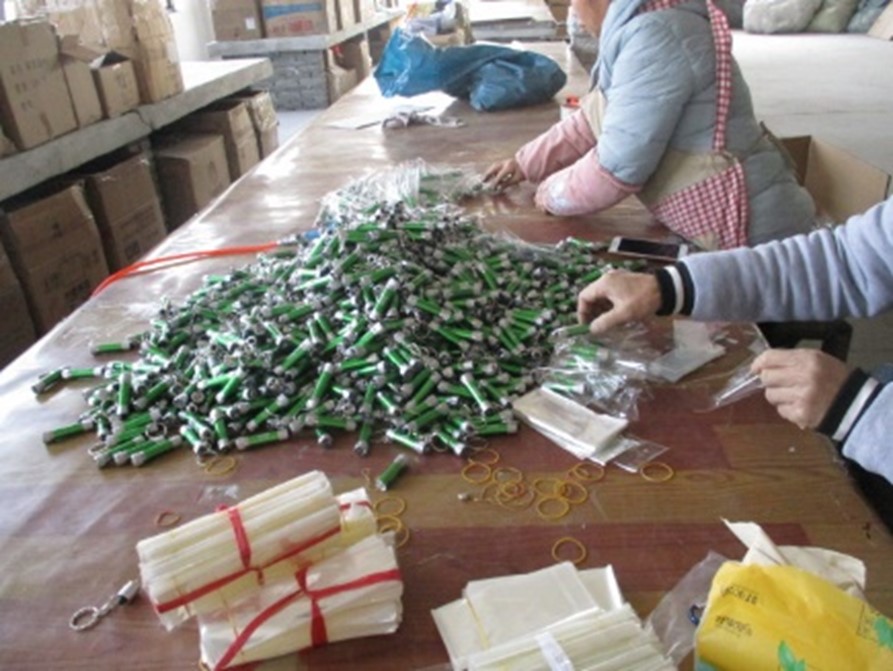
1.1 Materials and Components:
- Verify the quality of materials used in flashlight production, such as the body, lens, bulb, and batteries.
- Ensure that all components meet the specified standards and are free from defects or damage.
1.2 Dimensions and Specifications:
- Confirm that the flashlight dimensions and specifications adhere to the buyer’s requirements.
- Measure the length, width, and weight of the flashlight to ensure consistency.
1.3 Functional Testing:
- Test the flashlight’s basic functions, including turning on/off, adjusting brightness levels (if applicable), and activating additional features like strobe or SOS modes.
- Verify the functionality of any switches, buttons, or sliders.
1.4 Light Output and Beam Quality:
- Measure the flashlight’s lumen output using specialized equipment.
- Evaluate the beam quality, including the beam distance, beam angle, and uniformity of light distribution.
1.5 Battery Performance:
- Test the battery life by running the flashlight continuously for the specified duration.
- Check the compatibility and effectiveness of rechargeable batteries (if applicable).
1.6 Durability and Impact Resistance:
- Conduct drop tests to assess the flashlight’s resilience to impact.
- Ensure that the flashlight can withstand typical usage conditions and environments.
1.7 Water and Dust Resistance:
- Evaluate the flashlight’s IP rating to determine its resistance to water and dust.
- Perform water immersion tests to verify the claimed level of waterproofing.
1.8 Safety and Compliance:
- Verify that the flashlight meets relevant safety standards and certifications, such as CE, RoHS, and UL.
- Check for potential hazards like sharp edges or exposed electrical components.
2.Execution of Testing Procedures:
NBNQC utilizes a systematic approach to execute the flashlight quality control testing. Here’s an overview of our procedures:
2.1 Pre-Production Inspection:
- Before the manufacturing process begins, our inspectors conduct a pre-production inspection to ensure that the factory has the necessary materials and equipment to meet the buyer’s requirements.
- We also review the production schedule to ensure timely delivery.
2.2 During Production Inspection:
- Inspectors visit the factory during production to assess the quality of randomly selected samples.
- This includes checking the materials, components, dimensions, and overall workmanship.
- Any deviations or issues are reported to the factory for immediate corrective actions.
2.3 Final Random Inspection:
- When production is complete, a final random inspection is conducted to evaluate the overall quality of the flashlight batch.
- Inspectors randomly select a predetermined number of flashlights for comprehensive testing based on the checklist.
- Detailed reports are provided to the buyer, highlighting any non-conformities or areas of concern.
2.4 Loading Supervision:
- During the loading process, our inspectors supervise the packaging and loading of the flashlights into containers.
- We ensure that the correct quantity of products is loaded, and the packaging is appropriate for safe transportation.
NBNQC plays a crucial role in ensuring that flashlight manufacturers in China deliver products that meet international quality standards and compliance requirements. By following a comprehensive checklist and executing rigorous testing procedures, we provide buyers with confidence in the quality and reliability of their purchased flashlights. With our commitment to quality control, NBNQC continues to be a trusted partner for international sourcing in China.
Inspection Steps for Flashlights: Ensuring Quality and Reliability
Flashlights are indispensable tools for various applications, from everyday use to emergency situations. Ensuring the quality and reliability of flashlights is essential to guarantee their optimal performance and user safety. This article outlines a comprehensive guide on the inspection steps for flashlights, including visual inspection, functional testing, safety assessment, and compliance with relevant standards.
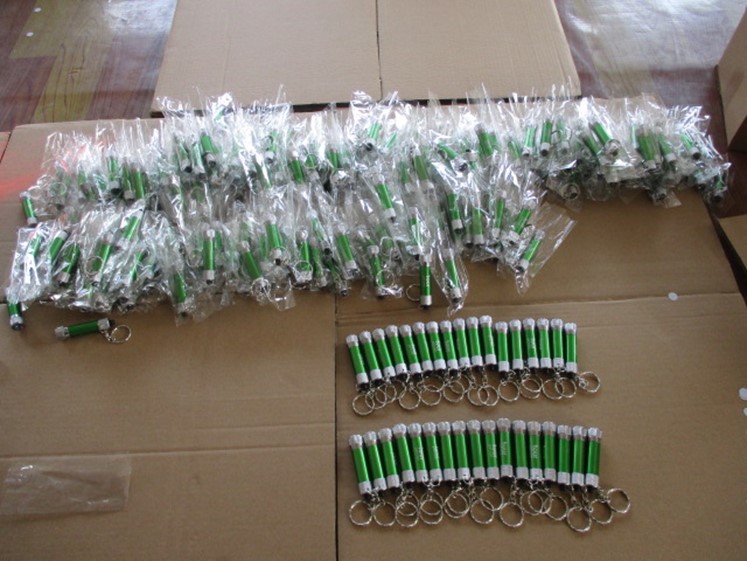
1.Introduction
Flashlights, also known as torches, are portable lighting devices widely used in homes, outdoor activities, workplaces, and emergency situations. The reliability and performance of flashlights directly impact user safety and satisfaction. A systematic inspection process helps identify defects, ensures adherence to quality standards, and enhances overall product quality.
2. Visual Inspection
Visual inspection is the first and crucial step in flashlight examination. Inspectors should meticulously examine each component of the flashlight for any visible defects, including but not limited to the following aspects:
- 2.1 Exterior Quality: Check for scratches, dents, cracks, or deformities on the flashlight body, lens, and reflector. Ensure that the surface finish is consistent and free from imperfections.
- 2.2 Switches and Buttons: Verify the functionality of on/off switches, mode selection buttons, and any other control mechanisms. Make sure they operate smoothly and do not show signs of wear or damage.
- 2.3 Battery Compartment: Inspect the battery compartment for any signs of corrosion or improper fitment. Proper contact between batteries and terminals is critical for optimal performance.
- 2.4 LED and Optics: Check the LED for any dead pixels, color inconsistencies, or defects. Inspect the lens and reflector for cleanliness and proper alignment.
- 2.5 Labels and Markings: Ensure that all necessary labels, markings, and safety warnings are present, legible, and accurate.
3.Functional Testing
Functional testing evaluates the performance of the flashlight in different operating modes and conditions. The following tests are commonly conducted:
- 3.1 Power Output: Measure the light output (lumens) of the flashlight in various modes, such as high, medium, and low. Compare the measured values with the manufacturer’s specifications.
- 3.2 Beam Distance: Assess the distance the flashlight beam can effectively cover. This measurement is crucial for outdoor and searchlight applications.
- 3.3 Battery Runtime: Test the runtime of the flashlight on different power settings. Verify if the claimed battery life aligns with the actual performance.
- 3.4 Waterproof and Dustproof Performance: Submerge the flashlight in water (as per the manufacturer’s instructions) to assess its waterproof capabilities. Similarly, test for resistance to dust and other foreign particles.
- 3.5 Impact Resistance: Conduct impact tests to determine the flashlight’s ability to withstand drops and shocks. Compare the results against the manufacturer’s specified impact resistance level.
4.Safety Assessment
Safety is paramount when dealing with electrical devices like flashlights. Inspectors should focus on the following safety aspects:
- 4.1 Overheating Protection: Verify if the flashlight has built-in mechanisms to prevent overheating during prolonged use.
- 4.2 Battery Protection: Check for features like overcharge protection, over-discharge protection, and short circuit protection to prevent potential hazards caused by battery malfunctions.
- 4.3 Electrical Insulation: Ensure that all electrical components are adequately insulated to prevent electrical shocks or short circuits.
- 4.4 Temperature Control: Evaluate the flashlight’s ability to maintain safe operating temperatures to prevent burns or injuries.
5.Compliance with Standards
Flashlights must adhere to relevant safety and quality standards to ensure consumer protection and satisfaction. Some key standards include:
- 5.1 ANSI/NEMA FL1 Standard: This standard outlines guidelines for flashlight performance testing, including light output, beam distance, runtime, impact resistance, and water resistance.
- 5.2 IEC 60529 (IP Code): The IP Code classifies the degree of protection provided against intrusion of solid objects, dust, and water.
- 5.3 CE Marking: For flashlights sold in the European Union, the CE marking signifies compliance with applicable safety, health, and environmental protection directives.
- 5.4 UL Listing: A UL listing indicates that the flashlight has been independently tested for safety by Underwriters Laboratories.
Conclusion
Proper inspection of flashlights is crucial to ensure their quality, reliability, and compliance with industry standards. By following the comprehensive inspection steps outlined in this article, manufacturers can identify and rectify potential defects, enhancing customer satisfaction and building a reputation for delivering high-quality and dependable flashlights. Furthermore, rigorous inspection processes promote user safety, particularly in critical applications where reliable lighting is essential for emergency situations and outdoor activities. With a commitment to continuous improvement and adherence to safety standards, flashlight manufacturers can thrive in a competitive market and establish lasting trust with their customers.