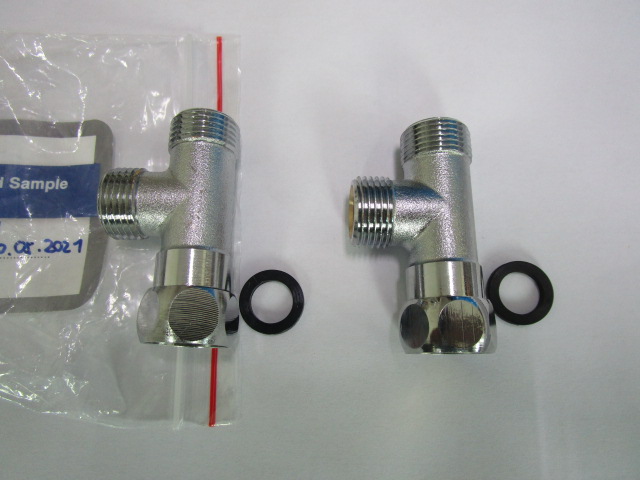
To thoroughly explore and expand upon the concepts of full inspection and sampling inspection in the context of international manufacturing and quality assurance, let’s delve into an in-depth discussion. This article aims to offer comprehensive insights into both methods, helping businesses make informed decisions based on their specific needs, product characteristics, and risk management strategies.
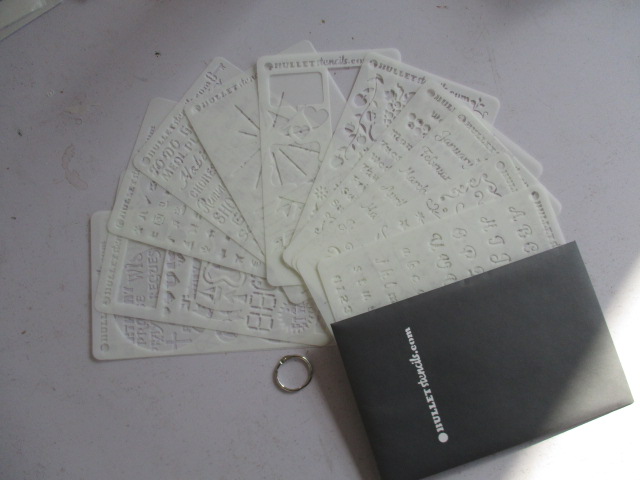
Contents
Understanding Full Inspection and Sampling Inspection in Quality Assurance
When manufacturing overseas, ensuring product quality aligns with expectations is crucial for any business. To mitigate the risks of quality issues and prevent substandard products from reaching the market, companies often rely on third-party inspection services. These services typically offer two primary types of inspections: full inspection and sampling inspection. Understanding the differences, advantages, and applications of each can significantly impact your quality control strategy.
Full Inspection: Ensuring Comprehensive Quality Control
Full inspection, as the term suggests, involves a detailed examination of every unit in a batch of products. Each item is individually assessed for quality, functionality, and compliance with specified standards. Any non-conforming items are identified and removed, aiming for a 100% quality check across the entire batch.
When to Choose Full Inspection:
- Volume Considerations: For smaller batches (e.g., 1-500 units), the cost of full inspection can be comparable to sampling inspection, making it a feasible option for comprehensive quality assurance.
- High-Value Products: Items with high unit costs or significant safety implications often warrant full inspections to minimize the risk of costly recalls or damage to brand reputation.
- E-commerce Concerns: Products sold on platforms like Amazon may benefit from full inspections to avoid customer dissatisfaction and returns due to quality issues.
- Post-Sampling Inspection Failures: If initial sampling inspections reveal widespread quality concerns, a full inspection can serve as a corrective measure to ensure no defective products are shipped.
Sampling Inspection: Balancing Cost and Quality
Sampling inspection involves selecting a random subset of products from a batch and testing these samples against quality standards. The results from these samples are then used to infer the quality of the entire batch. This method is favored for its cost-effectiveness and efficiency, particularly suited for large-scale productions.
Advantages of Sampling Inspection:
- Cost-Effectiveness: Sampling reduces the time and resources spent on quality control, making it an economical option for large batches.
- Efficiency: By inspecting a representative sample, companies can quickly gauge product quality without the need for exhaustive checks.
- Flexibility: Sampling plans can be adjusted based on risk tolerance, product value, and historical quality performance.
When to Choose Sampling Inspection:
- Large Production Volumes: For extensive batches, sampling offers a practical method for quality assessment without the need for exhaustive checks.
- Medium to Low-Value Items: Products with lower unit costs may not justify the expense of a full inspection, making sampling a sensible choice.
- Established Quality History: If a supplier has a consistent track record of high-quality production, sampling inspections may suffice to ensure ongoing compliance.
Implementing AQL Standards in Sampling Inspection
The Acceptable Quality Limit (AQL) is a crucial standard in sampling inspection. It defines the maximum number of defective items considered acceptable in a sample batch. Businesses can specify AQL levels and sampling sizes based on their quality expectations and risk management strategies.
Choosing the Right AQL Level:
- Defining Quality Expectations: The AQL level should reflect the acceptable threshold for defects, considering the nature of the product and customer expectations.
- Risk Management: Higher AQL levels may be appropriate for less critical items, while stricter AQLs are advisable for high-value or safety-sensitive products.
Strategic Considerations in Quality Inspection
Choosing between full inspection and sampling inspection requires a strategic approach, considering factors such as production volume, product value, customer expectations, and the potential impact of defects. Implementing a dynamic quality control strategy that adapts to these variables can help businesses maintain high-quality standards while managing costs effectively.
Conclusion
Quality control is a pivotal element of international manufacturing, demanding a thoughtful approach to inspection methods. Whether opting for full inspection or sampling inspection, the decision should align with the company’s overall quality assurance goals, product characteristics, and market demands. By understanding and applying the principles of each inspection type judiciously, businesses can ensure product quality, satisfy customer expectations, and uphold their reputation in a competitive marketplace.