Pre-shipment inspection is a critical phase in the toy manufacturing process. It ensures that toys meet the required quality and safety standards before they are shipped to customers. A thorough pre-shipment inspection helps identify defects, deviations from specifications, and compliance issues, preventing the distribution of substandard or unsafe toys. In this article, we will explore the key considerations that should be taken into account during the pre-shipment inspection of toys.
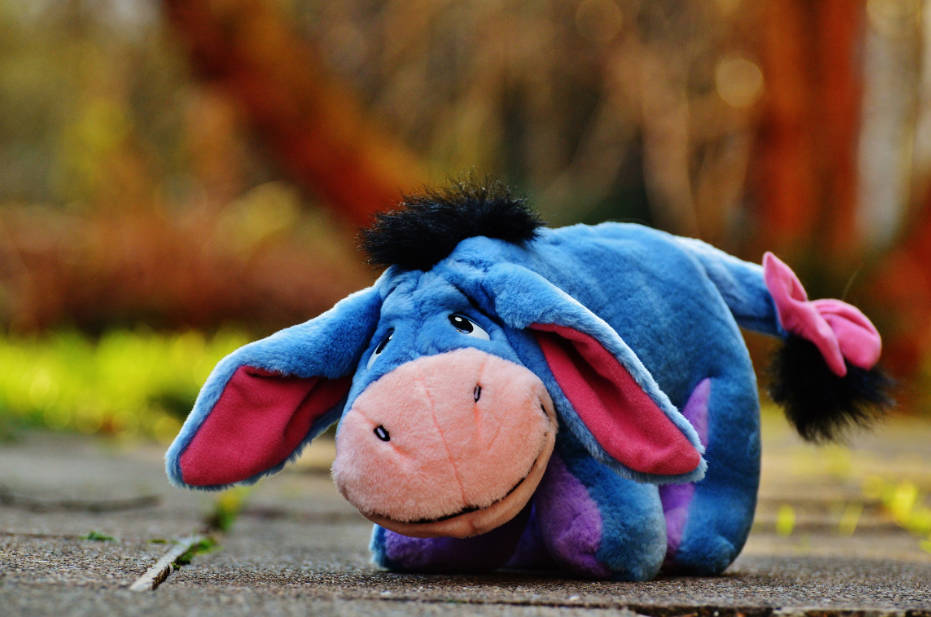
Contents
- 1 1. Adherence to Safety Standards
- 2 2. Material Quality
- 3 3. Workmanship and Craftsmanship
- 4 4. Mechanical and Functional Testing
- 5 5. Packaging and Labeling
- 6 6. Quantity and Consistency
- 7 7. Regulatory Compliance
- 8 8. Testing Equipment Calibration
- 9 9. Random Sampling
- 10 10. Documentation and Reporting
- 11 11. Corrective Actions
- 12 12. Timely Communication
- 13 Conclusion
1. Adherence to Safety Standards
Safety is paramount when it comes to toys, especially those intended for children. The first and foremost consideration during pre-shipment inspection is verifying that the toys comply with relevant safety standards. These standards may include ASTM F963-21, EN 71, ISO 8124, and others, depending on the target market. Inspectors should check for sharp edges, small parts that pose a choking hazard, and any potentially harmful chemicals or substances. Ensuring adherence to these standards mitigates risks associated with physical injuries, choking hazards, and exposure to toxic materials.
2. Material Quality
The quality of materials used in toy production is a critical factor. Inspectors should assess the materials’ durability, toxicity, and compliance with safety regulations. For instance, wooden toys should be made from non-toxic and splinter-free wood, while plastic toys must not contain hazardous substances like lead or phthalates. For plush toys, the fabric should be soft, non-irritating, and free from allergens. High-quality materials not only ensure the safety of the toys but also their longevity and overall appeal to consumers.
3. Workmanship and Craftsmanship
The overall quality of workmanship and craftsmanship plays a significant role in toy inspection. Inspectors should closely examine the stitching on plush toys, the finish on wooden toys, and the assembly of electronic components in electronic toys. Any defects, irregularities, or subpar workmanship should be identified and documented. Attention to detail in workmanship ensures that toys are durable and safe for use, enhancing customer satisfaction and reducing the likelihood of returns and complaints.
4. Mechanical and Functional Testing
Mechanical and functional testing is essential to ensure that the toys operate as intended and are safe to use. This includes testing moving parts, such as wheels on toy cars, joints on action figures, and buttons on electronic toys. Functional tests for electronic toys should verify that all features and functions work correctly, including sound, lights, and sensors. Thorough mechanical and functional testing helps identify potential hazards and operational failures that could harm children or render the toys useless.
5. Packaging and Labeling
Inspectors should assess the packaging and labeling of toys. The packaging should be sturdy and protective to prevent damage during transit. Labels must include all required information, such as safety warnings, age-appropriateness, and manufacturer details. Missing or incorrect labeling can result in non-compliance with regulations. Proper packaging and accurate labeling are crucial for protecting the toys during shipment and providing consumers with necessary information to ensure safe and appropriate use.
6. Quantity and Consistency
Ensuring that the correct quantity of toys is being shipped is crucial. Inspectors should count the items in each carton and verify that they match the order specifications. Additionally, they should check for consistency in terms of color, design, and any customization requested by the customer. Consistency in the product batch assures customers of the reliability and quality of the toys they receive, fostering trust in the brand.
7. Regulatory Compliance
Toys must meet various regulations depending on the target market. Inspectors should be well-versed in the specific regulations applicable to the toys they are inspecting. This includes safety standards, labeling requirements, and documentation for customs clearance. Compliance with these regulations ensures that toys can be legally sold in the intended markets, avoiding legal issues and potential recalls.
8. Testing Equipment Calibration
It’s essential to ensure that testing equipment used during pre-shipment inspection is properly calibrated and maintained. Accurate measurements and tests rely on well-functioning equipment. Regular calibration and maintenance routines should be in place to guarantee the reliability of inspection results. Properly calibrated equipment ensures the accuracy of safety tests and quality checks, providing trustworthy inspection outcomes.
9. Random Sampling
Inspectors should select a statistically significant random sample of toys from the production lot. Random sampling ensures that the inspection results are representative of the entire batch of toys. The sample size and selection method should align with industry standards and best practices. Effective sampling techniques help detect systemic issues in production, ensuring overall batch quality.
10. Documentation and Reporting
Accurate and thorough documentation is a hallmark of a successful pre-shipment inspection. Inspectors should maintain detailed records of their findings, including photographs and test results. A comprehensive inspection report should be provided to the manufacturer or importer, highlighting any issues discovered during the inspection. Detailed documentation supports accountability and traceability, enabling manufacturers to address and rectify identified issues effectively.
11. Corrective Actions
When defects or non-compliance issues are identified during pre-shipment inspection, it is essential to define corrective actions. These actions may involve reworking, repairing, or disposing of substandard toys. Manufacturers should address these issues promptly to prevent the shipment of faulty products. Implementing corrective actions ensures continuous improvement in the manufacturing process and enhances product quality over time.
12. Timely Communication
Effective communication between the inspection agency, manufacturer, and customer is crucial. Any issues or delays should be promptly communicated to all parties involved to facilitate quick resolution and avoid disruptions in the supply chain. Clear and timely communication helps in managing expectations and ensuring smooth operations, thereby maintaining customer satisfaction and operational efficiency.
Conclusion
Pre-shipment inspection is a critical step in ensuring the quality and safety of toys before they reach the hands of consumers. By diligently considering the factors mentioned above, manufacturers and importers can be confident that their toys meet the required standards and regulations. Ultimately, a comprehensive pre-shipment inspection process not only safeguards consumer safety but also protects brand reputation and reduces the risk of costly recalls and returns. Through rigorous inspection practices and proactive quality management, the toy industry can continue to provide safe, high-quality products that delight and reassure customers worldwide.