Plastic components play a crucial role in various industries, ranging from automotive and electronics to consumer goods and packaging. With China being a major global manufacturing hub for plastic parts, ensuring the quality and compliance of these components is of utmost importance. This article delves into the significance of inspecting plastic components in China, the common inspection methods employed, and the regulatory landscape governing this process.
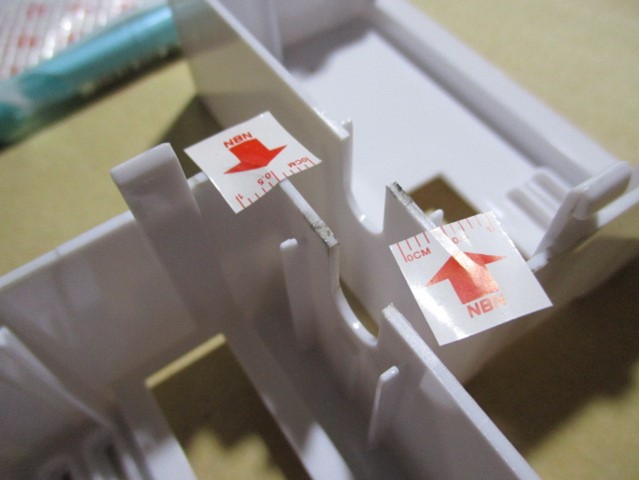
Contents
1. Introduction
China’s manufacturing prowess is undisputed, and its plastic component industry has witnessed tremendous growth over the years. As businesses around the world increasingly rely on China for their plastic part needs, the significance of thorough inspection processes becomes paramount. Proper inspection ensures that the plastic components meet industry standards, maintain product quality, and adhere to regulatory requirements.
2. Importance of Inspection
2.1 Quality Assurance
Maintaining consistent quality is vital for any business. With the diverse applications of plastic components, ranging from safety-critical automobile parts to medical devices, ensuring their quality is crucial to avoid potential failures or defects. Inspection processes help in identifying and rectifying any quality issues, leading to better customer satisfaction and long-term success for manufacturers.
2.2 Safety and Reliability
In certain industries, such as aerospace and medical, the safety and reliability of plastic components can have life-or-death consequences. Rigorous inspection protocols are essential to guarantee that these components meet the stringent safety standards and can perform flawlessly under various conditions.
2.3 Cost Savings
Effective inspection practices help detect defects early in the production process, minimizing rework and scrap rates. This, in turn, reduces overall production costs and enhances the company’s bottom line.
3. Common Inspection Methods
3.1 Visual Inspection
Visual inspection is one of the simplest yet effective methods of examining plastic components. Skilled inspectors examine the components for defects, such as surface irregularities, discoloration, or molding imperfections. Advanced lighting and magnification tools aid inspectors in identifying even the tiniest flaws.
3.2 Dimensional Inspection
Dimensional accuracy is critical for plastic parts to fit and function correctly. Coordinate measuring machines (CMM) and other precision tools are used to measure and verify critical dimensions against design specifications.
3.3 Mechanical Testing
Mechanical testing involves subjecting plastic components to various stress conditions to evaluate their mechanical properties, such as tensile strength, impact resistance, and flexural modulus. This helps ensure that the components can withstand real-world operating conditions.
3.4 Chemical Analysis
Chemical analysis is used to verify the composition of plastic materials, which is crucial for ensuring compliance with safety and environmental regulations. Spectroscopy and chromatography techniques are commonly used for this purpose.
4. Regulatory Landscape
China has various regulations and standards that govern the production and inspection of plastic components. Some of the prominent ones include:
GB/T 2918-2018: General rules for the sampling of plastic products.
GB/T 2828.1-2012: Sampling procedures for inspection by attributes – Part 1: Sampling schemes indexed by acceptance quality limit (AQL) for lot-by-lot inspection.
ISO 9001:2015: Quality management systems – Requirements.
ISO 13485:2016: Medical devices – Quality management systems.
Compliance with these regulations ensures that the manufactured plastic components meet the required safety, quality, and environmental standards.
5. Challenges and Solutions
5.1 Language and Cultural Barriers
For international businesses sourcing plastic components from China, language barriers can pose challenges during the inspection process. Collaborating with bilingual inspection companies or employing qualified translators can bridge this gap.
5.2 Supplier Selection
Choosing reliable and reputable suppliers is crucial. Conducting thorough background checks, assessing their quality control systems, and inspecting their production facilities can help in making informed decisions.
5.3 Counterfeit Concerns
Counterfeit plastic components can infiltrate the supply chain, leading to potential safety hazards and product failures. Implementing strict anti-counterfeit measures and partnering with trustworthy suppliers can mitigate this risk.
Conclusion
The inspection of plastic components in China is an essential process to ensure quality, safety, and compliance with international standards. Implementing effective inspection methods and adhering to regulatory requirements contribute to the success and reputation of manufacturers, fostering trust among customers worldwide. By continually improving inspection processes and addressing emerging challenges, China can solidify its position as a leading provider of high-quality plastic components.