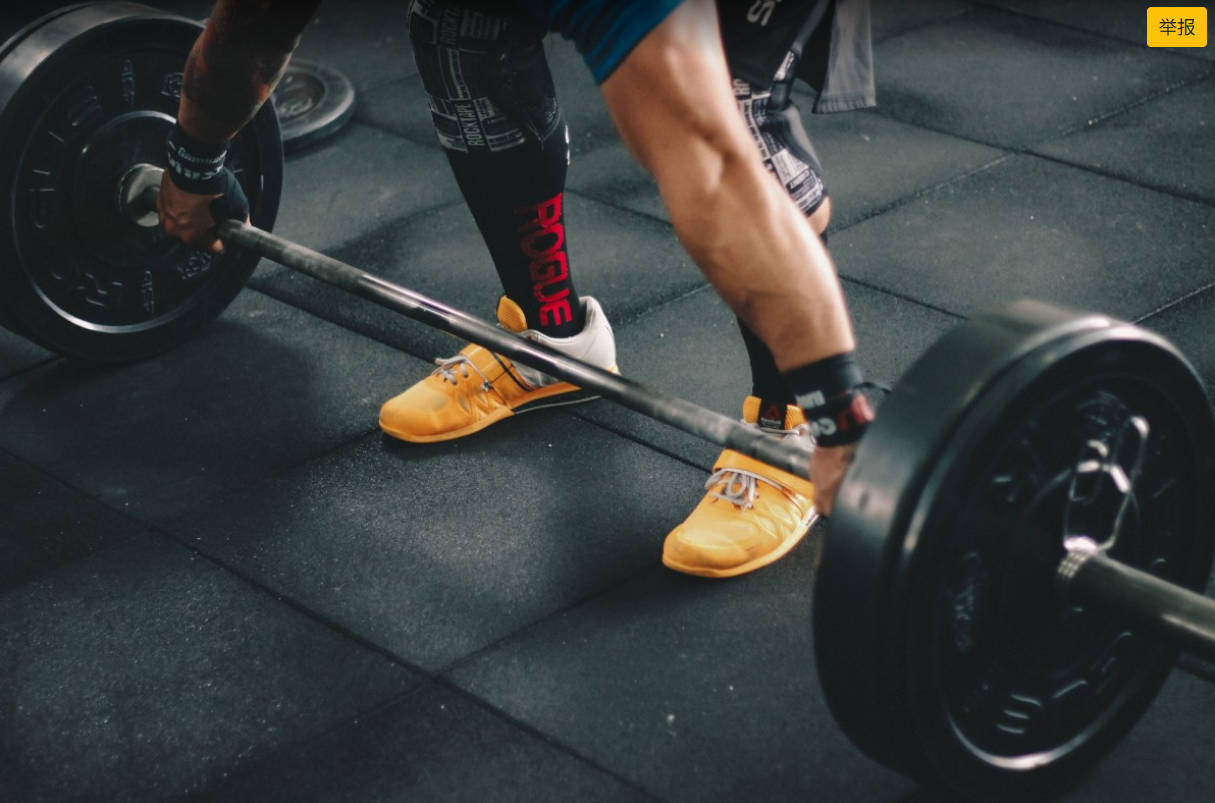
Contents
Introduction
Color is one of the most important aspects of clothing. It is the first thing people notice when they look at a garment. As such, it is essential to maintain consistency in the color of clothing during production. However, color differences are a common issue in the garment industry. These differences may arise due to several factors, including fabric variation, dyeing techniques, and production methods.
In this article, we will discuss the different ways in which manufacturers can reduce color differences in the garment quality control process.

1.Standardization of Color Management
The first step towards reducing color differences in clothing production is to standardize the color management process. This process involves the creation of a color standard that is used throughout the production cycle. This standard should be created based on industry standards, such as the Pantone Color Matching System (PMS), which is widely used in the garment industry.
The color standard should be communicated to all stakeholders, including designers, fabric suppliers, and production teams. The use of digital color management systems can help ensure that the color standard is followed throughout the production process.
2. Fabric Inspection
Fabric inspection is an essential part of the quality control process. It involves the examination of the fabric for defects, including color differences. Fabric inspection should be done before the dyeing process to ensure that the fabric is consistent in color and free from any defects that may affect the dyeing process.
3. Dyeing Process
The dyeing process is critical in determining the final color of the garment. As such, it is essential to ensure that the dyeing process is consistent throughout the production cycle. This can be achieved by using standard dyeing techniques and monitoring the dyeing process closely.
The use of digital color matching systems can help ensure that the dyeing process is consistent. These systems use color sensors to measure the color of the fabric and provide feedback on the dyeing process. The use of these systems can help reduce color differences by ensuring that the dyeing process is consistent.
4. Lighting
Lighting is an essential factor in color perception. Different lighting conditions can affect the way colors are perceived. As such, it is important to use consistent lighting conditions throughout the production process.
The use of a lightbox can help ensure that lighting conditions are consistent. A lightbox is a device that provides uniform lighting conditions, allowing for accurate color assessment. The use of a lightbox can help reduce color differences by ensuring that colors are assessed under consistent lighting conditions.
5. Color Assessment
Color assessment is an important part of the quality control process. It involves the comparison of the final product with the color standard to ensure that the color is consistent. Color assessment should be done under consistent lighting conditions to ensure accurate color perception.
The use of digital color assessment systems can help ensure that color assessment is consistent. These systems use color sensors to measure the color of the final product and compare it to the color standard. The use of these systems can help reduce color differences by ensuring that color assessment is consistent.
6. Training
Training is an essential part of any quality control process. It ensures that all stakeholders are aware of the standards and processes involved in the production cycle. Training should be provided to all stakeholders, including designers, fabric suppliers, and production teams.
The training should include information on color management, fabric inspection, dyeing techniques, lighting, and color assessment. The use of digital training materials can help ensure that training is consistent and easily accessible.
Conclusion
In conclusion, color differences are a common issue in clothing production. However, there are several ways in which clothing manufacturers can reduce color differences in the quality control process. These include standardization of color management, fabric inspection, consistent dyeing techniques, lighting, color assessment, and training.
The use of digital color management systems, digital color matching systems, lightboxes, and digital training materials can all help to ensure that the color standard is followed throughout the production cycle and reduce color differences.
By implementing these measures, clothing manufacturers can improve the quality of their products and reduce the likelihood of customer complaints. Consistent color management can also help to build a brand image and establish trust with customers.
It is important to note that reducing color differences in clothing production is an ongoing process that requires constant monitoring and adjustment. As such, it is essential to establish a system for regular quality control checks and to make changes as necessary.
In summary, reducing color differences in clothing quality control process is critical for ensuring consistency in the final product. Through standardization of color management, fabric inspection, consistent dyeing techniques, lighting, color assessment, and training, manufacturers can improve the quality of their products, build brand image, and establish trust with customers.