Glass containers play a vital role in various industries, including food and beverage, pharmaceuticals, and cosmetics. Ensuring the quality of glass containers is crucial to maintain product integrity and safety. However, there are several misconceptions that can hinder effective quality inspection processes. This article aims to address five common misconceptions in the quality inspection of glass containers and provides insights on how to overcome them.
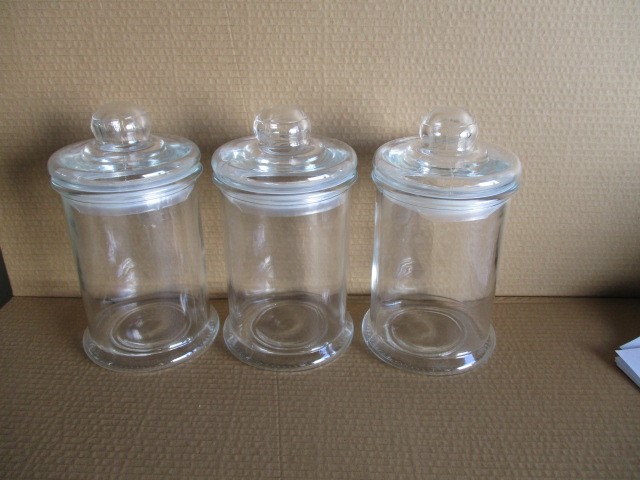
Contents
- 1 1.Misconception: Visual Inspection is Sufficient
- 2 2.Misconception: Thickness Uniformity Guarantees Strength
- 3 3.Misconception: Surface Scratches Are Superficial Issues
- 4 4.Misconception: Weight Variation Indicates Quality Issues
- 5 5.Misconception: Quality Inspection Should Occur Only at the End of Production
- 6 Conclusion:
1.Misconception: Visual Inspection is Sufficient
One of the most prevalent misconceptions is that visual inspection alone is enough to ensure the quality of glass containers. While visual inspection is essential, it cannot detect internal defects or structural weaknesses that may compromise the integrity of the container. Therefore, relying solely on visual inspection may lead to the oversight of critical issues.
Solution: Implement Additional Testing Methods
To overcome this misconception, quality inspection processes should include additional testing methods such as leak testing, stress testing, and dimensional measurements. These methods help identify potential defects that are not visible to the naked eye and provide a more comprehensive evaluation of the glass container’s quality.
2.Misconception: Thickness Uniformity Guarantees Strength
Some may assume that if a glass container exhibits uniform thickness, it automatically ensures its strength and durability. However, thickness alone is not the sole determinant of a glass container’s strength. Other factors, such as the glass composition, heat treatment, and design, also significantly influence its overall strength.
Solution: Perform Strength and Durability Testing
To address this misconception, quality inspections should include strength and durability testing. This may involve conducting drop tests, pressure tests, or impact resistance tests to evaluate the container’s ability to withstand various forces and environmental conditions. These tests provide a more accurate assessment of the container’s strength beyond thickness measurements.
3.Misconception: Surface Scratches Are Superficial Issues
Surface scratches are often considered minor cosmetic defects that do not impact the functionality or safety of glass containers. However, even small scratches can weaken the structural integrity of the glass and make it more prone to breakage or stress concentration points.
Solution: Evaluate Scratch Depth and Severity
To address this misconception, quality inspections should assess the depth and severity of surface scratches. Utilizing specialized equipment, inspectors can measure the depth of scratches and evaluate their potential impact on the container’s strength. By implementing appropriate acceptance criteria, manufacturers can ensure that even minor scratches are identified and addressed.
4.Misconception: Weight Variation Indicates Quality Issues
Another misconception is that weight variation in glass containers is always an indication of quality problems. While significant weight variations may suggest inconsistencies in the manufacturing process or improper filling, minor weight variations can be expected due to the inherent nature of glass manufacturing.
Solution: Establish Tolerance Levels
To overcome this misconception, manufacturers should establish tolerance levels for weight variations in glass containers. These tolerances should consider factors such as container size, design, and intended use. By setting appropriate tolerance ranges, quality inspectors can differentiate between acceptable weight variations and those that exceed the specified limits, indicating potential quality issues.
5.Misconception: Quality Inspection Should Occur Only at the End of Production
Some may mistakenly believe that quality inspection of glass containers should only occur at the end of the production process. However, relying solely on final inspection can result in detecting issues too late, leading to increased production costs, wastage, and customer dissatisfaction.
Solution: Implement In-process Quality Controls
To address this misconception, manufacturers should implement in-process quality controls throughout the production cycle. These controls can include inspections at various stages, such as raw material inspection, forming and shaping processes, and final assembly. By conducting inspections at multiple points, manufacturers can identify and rectify quality issues early, minimizing the likelihood of defects reaching the final product stage.
Conclusion:
Quality inspection is a critical aspect of ensuring the reliability, safety, and functionality of glass containers. By understanding and addressing common misconceptions in the quality inspection process, manufacturers can enhance their ability to detect and prevent defects. By implementing comprehensive testing methods, evaluating scratch severity, considering appropriate tolerance levels, and conducting in-process inspections, manufacturers can produce high-quality glass containers that meet industry standards and customer expectations.
NBNQC is a leading third-party inspection company in China and we are pleased to provide quality control and inspection services to our customers around the world.