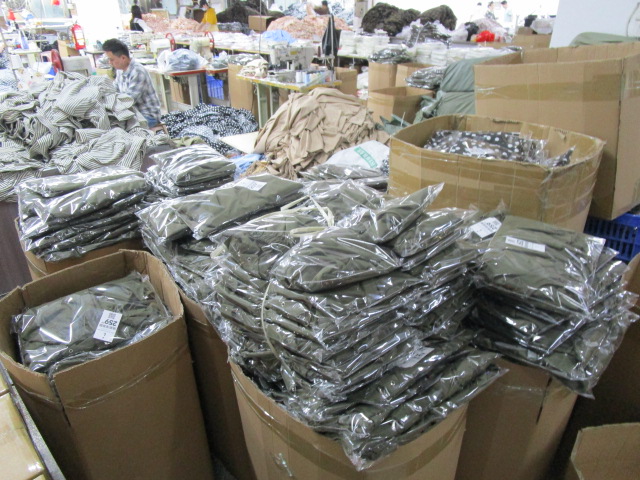
In the dynamic world of manufacturing and trade, third-party inspection companies play a vital role in ensuring that products meet quality standards before they reach the hands of consumers. This article provides a detailed insight into how third-party inspection companies execute pre-shipment inspections for socks, ensuring that every pair meets established quality criteria and safeguards customer satisfaction.
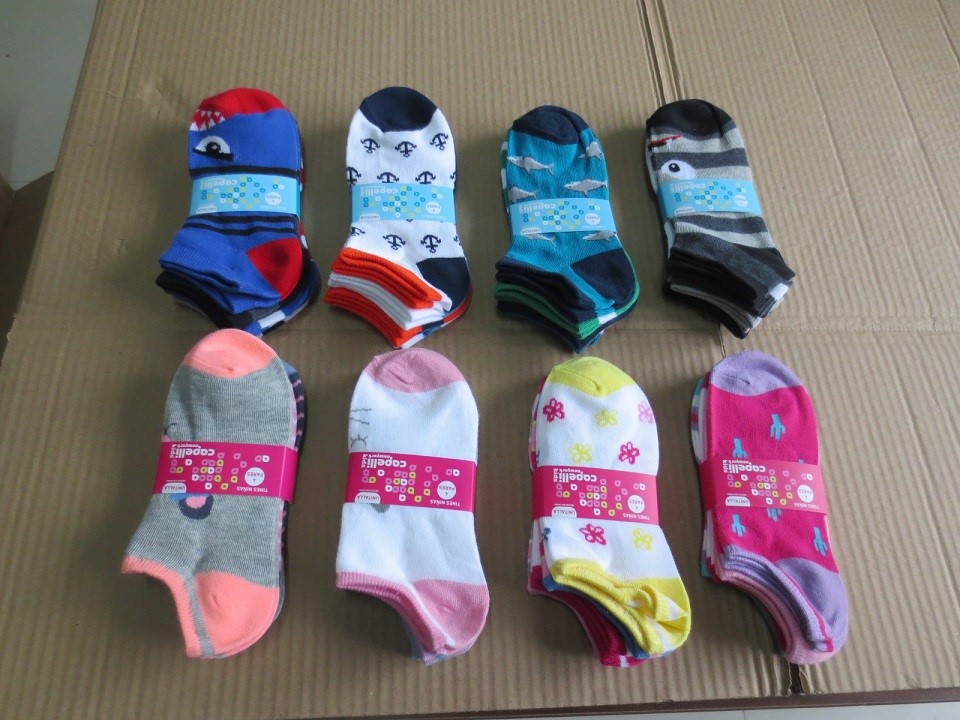
The Role of Third-Party Inspection Companies
Third-party inspection companies act as independent entities that evaluate and verify the quality, safety, and compliance of products on behalf of manufacturers, suppliers, and buyers. Their objective is to bridge the gap between producers and consumers by conducting impartial inspections that ensure the final products are of the highest quality.
1. Agreement and Scope Definition
The pre-shipment inspection process typically begins with an agreement between the manufacturer, supplier, or buyer and the third-party inspection company. The terms of the inspection, including the scope, criteria, and sampling method, are clearly defined. The inspection company and the client collaborate to establish the specific requirements that the socks must meet.
2. Sampling Plan
One of the fundamental aspects of pre-shipment inspection is the sampling plan. The inspection company collaborates with the client to determine the appropriate sample size based on statistical principles and the acceptable quality level (AQL). The AQL defines the maximum number of defects or deviations from the standard that are acceptable within the batch.
3. Selection of Inspection Team
Third-party inspection companies have a roster of experienced and trained inspectors with expertise in various industries. For socks, inspectors should have an understanding of textile materials, manufacturing processes, and quality criteria. The inspection company assigns the most suitable inspector or team of inspectors for the job.
4. Pre-Inspection Preparation
Before the inspection day, the inspection company communicates with the manufacturer or supplier to ensure that the selected batch of socks is ready for evaluation. This involves coordination to have the necessary samples available, production documents accessible, and the production process at a stage where representative samples are available for assessment.
5. On-Site Inspection
On the designated inspection day, the inspection team visits the manufacturer’s facility or the designated storage location. The inspection is executed based on the predefined scope and criteria, covering various quality attributes:
- Material Inspection: The raw materials, including yarns, fabrics, and dyes, are examined to ensure they meet the established quality standards and are consistent with approved samples.
- Stitching and Seam Quality: Inspectors assess the stitching and seams of the sampled socks to ensure they are uniform, secure, and free from defects that could compromise the socks’ quality.
- Sizing and Fit: The sizing accuracy of the socks is checked against the predetermined standards to ensure a proper fit for consumers.
- Color Consistency: The color of the socks is evaluated to verify that it matches approved color samples and remains consistent throughout the batch.
- Elasticity and Stretch Recovery: The elasticity of the socks is tested by stretching them gently to assess their ability to recover their original shape.
- Packaging and Labeling: Inspectors review the packaging and labeling of the socks to ensure accuracy and alignment with the brand’s guidelines.
6. Documentation and Reporting
During the inspection, the inspection team meticulously documents their findings, noting any deviations from the established quality criteria. Photographs and detailed descriptions are recorded to provide clear evidence of the inspection outcomes. This documentation forms the basis of the inspection report.
7. Inspection Report
Upon completion of the on-site inspection, the inspection company compiles a comprehensive inspection report. This report includes:
- Detailed Findings: A description of the inspection process, including the criteria assessed and the findings for each attribute.
- Photographic Evidence: High-quality images that visually demonstrate the quality of the socks, highlighting any defects or deviations.
- Comparison to Standards: A clear comparison of the inspected socks against the agreed-upon quality standards and criteria.
- Defect Classification: An assessment of the severity of any identified defects, categorized based on their impact on product quality.
8. Corrective Action Recommendations
In cases where quality issues are identified, the inspection company may provide recommendations for corrective actions. These actions may involve reworking, repairing, or even rejecting the batch, depending on the severity of the issues.
9. Communication with the Client
The inspection company communicates the results of the inspection and provides the inspection report to the client, whether it’s the manufacturer, supplier, or buyer. This transparent communication allows the client to make informed decisions based on the inspection outcomes.
10 Continuous Improvement
Third-party inspection companies often collaborate with their clients to enhance overall quality. The insights gained from inspections can be used to improve production processes, address recurring quality issues, and optimize manufacturing practices.
Conclusion
The execution of pre-shipment inspection for socks by third-party inspection companies is a meticulous process that ensures the highest quality standards are upheld. These independent entities collaborate with clients, employ skilled inspectors, and follow standardized procedures to assess socks based on predefined criteria. By providing transparent reporting and recommendations for corrective actions, third-party inspection companies contribute to maintaining the integrity of the supply chain and delivering high-quality products to consumers. This collaborative effort between manufacturers, suppliers, buyers, and inspection companies ultimately fosters consumer trust and satisfaction in the products they receive.