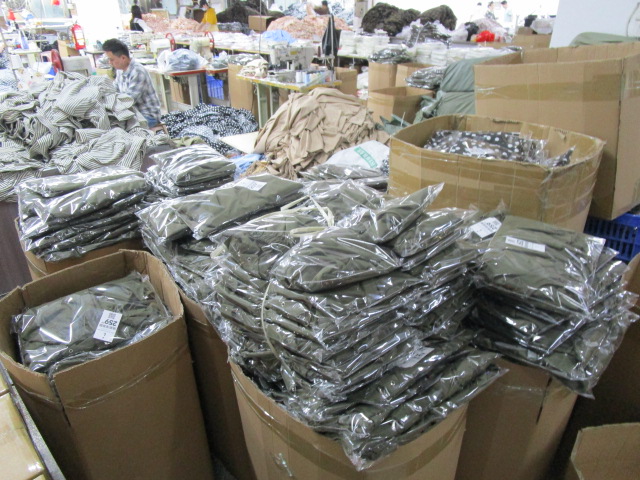
Stationery products, encompassing everything from writing tools and paper to adhesives and office essentials, are integral to our daily routines. Their ubiquitous presence, particularly in settings frequented by children, underscores the importance of their safety. Leveraging third-party inspections is vital in safeguarding the quality and safety of these products. This process provides an impartial assessment, ensuring that stationery items meet stringent safety standards before they reach consumers.
Contents
Key aspects of safety in stationery products
1. Chemical Safety:
Chemical safety is a critical aspect of stationery product inspection. It involves assessing the presence and levels of hazardous substances, such as heavy metals (lead, cadmium), phthalates, and volatile organic compounds (VOCs). Inspectors should verify compliance with relevant regulations, such as the European Union’s REACH (Registration, Evaluation, Authorization, and Restriction of Chemicals) regulation. They should test stationery products for the presence of harmful substances and ensure that they meet acceptable limits to protect users from potential health risks.
2. Choking Hazard Prevention:
Stationery products, especially those designed for children, should be free from small parts or components that pose a choking hazard. Inspectors need to assess the size and integrity of product components, such as pen caps, erasers, or small decorative elements. They should verify compliance with relevant safety standards, such as the ASTM F963 standard for toy safety, to ensure that the products are safe for use by children of different age groups.
3. Sharp Edge and Point Assessment:
Stationery items like scissors, knives, or compasses should undergo inspections to ensure the absence of sharp edges or points that could cause injuries. Inspectors should check the design, construction, and finish of these products, paying particular attention to potential sharp areas. They should verify compliance with safety standards, such as ISO 6396, which specifies requirements for cutting edges on stationery articles.
4. Ink and Paint Safety:
Writing instruments, such as pens and markers, often use ink or paint. Inspectors should evaluate the safety of these substances, ensuring they comply with regulations regarding toxic substances and allergens. They should conduct tests for ink solubility, drying time, and smudging. Additionally, inspectors should verify compliance with labeling requirements, including warnings about potential skin or eye irritation.
5. Mechanical Safety and Durability:
Stationery products should undergo mechanical safety and durability assessments to ensure their resistance to breakage or malfunction during normal use. Inspectors should check the overall construction, including the strength of materials, proper assembly, and the functionality of moving parts. They should test products for impact resistance, fatigue, and stress under expected usage conditions to ensure they meet quality and safety standards.
6. Packaging and Labeling Compliance:
Packaging and labeling are vital elements in ensuring the safety and proper use of stationery products. Inspectors should verify that packaging materials are free from contaminants, such as lead or phthalates, and evaluate the adequacy of packaging to protect products during transportation. They should check labeling requirements, including product identification, safety warnings, instructions for use, and age recommendations. Compliance with regulations like the Consumer Product Safety Improvement Act (CPSIA) in the United States should be ensured.
7. Performance and Functionality:
Inspectors should test the performance and functionality of stationery products to ensure they meet customer expectations. This includes assessing the quality of writing or drawing marks, the ease of use, and the consistency of product performance. For example, pens should provide smooth ink flow without skipping or smearing, while adhesive products should have proper bonding strength and drying properties.
8. Ergonomics and User Safety:
Considerations for ergonomics and user safety are essential, especially for stationery products designed for prolonged use, such as ergonomic pens or desk accessories. Inspectors should assess the design and comfort of these products, checking for features like non-slip grips, proper finger positioning, and reduced strain on the user’s hand or body.
Key Considerations for Third-Party Inspections
During third-party inspections of stationery products, inspectors should pay attention to the following considerations:
- Compliance with Regulations: Inspectors must be well-versed in applicable safety regulations, such as those mentioned earlier, to ensure that stationery products meet the required standards.
- Sample Selection: Inspectors should select representative samples for testing and inspection, ensuring they cover different variations, designs, and production batches.
- Testing Methods: Inspectors should utilize appropriate testing methods, such as chemical analysis, mechanical testing, and performance evaluations, to accurately assess the safety and quality of stationery products.
- Inspection Protocols: Inspectors should follow established protocols and checklists to ensure consistent and thorough evaluations. This helps in identifying potential safety hazards and non-compliance issues.
- Documentation and Reporting: Inspectors should maintain detailed documentation of the inspection process, including testing results, photographs, and any non-compliance issues found. They should generate comprehensive inspection reports, providing clear information on the product’s safety and quality status.
Safety is of utmost importance when it comes to stationery products. Third-party inspections play a crucial role in ensuring that these products meet the necessary safety standards and comply with regulations. By considering the aspects of chemical safety, choking hazard prevention, sharp edge assessment, ink and paint safety, mechanical safety, packaging compliance, performance evaluation, and user safety, inspectors can effectively assess the quality and safety of stationery products. Through rigorous inspections, we can ensure that stationery items are safe for use, particularly among children, and promote consumer confidence in the industry.