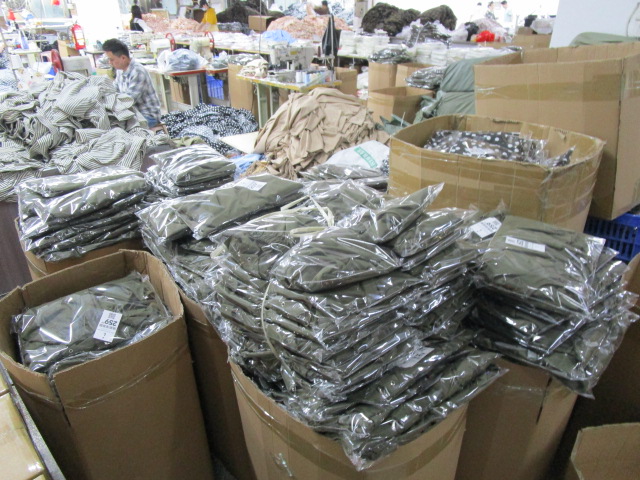
In the highly competitive global apparel industry, maintaining high product quality is crucial to avoid customer complaints and preserve brand reputation. To mitigate the risks associated with shipping defective garments, many companies rely on third-party inspection companies in China. These independent organizations play a critical role in conducting quality inspections and ensuring that only products of the highest standards are shipped. This article explores how leveraging Chinese third-party inspection companies can effectively control apparel quality, minimize the occurrence of defective products, and prevent customer complaints.
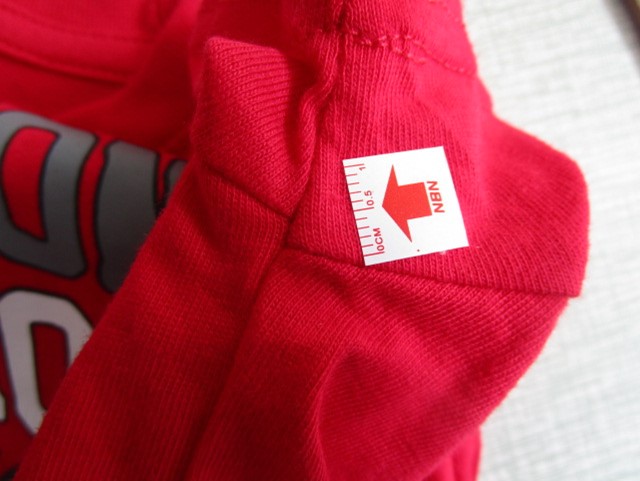
Contents
1. Understanding the Role of Chinese Third-Party Inspection Companies:
Chinese third-party inspection companies act as impartial entities responsible for conducting thorough quality inspections on apparel shipments. Their primary objective is to identify any defects or discrepancies in the products before they are dispatched to customers. By providing an independent assessment, these companies ensure that the garments meet the specified quality standards, thus mitigating the risk of delivering substandard products.
2. Selecting a Reliable Chinese Third-Party Inspection Company:
To effectively control apparel quality, it is essential to choose a reputable and experienced third-party inspection company in China. Consider the following factors during the selection process:
a. Track Record and Expertise: Look for companies with a proven track record in apparel inspection and considerable industry experience. Conduct thorough research, seek recommendations, and review customer feedback to assess their accuracy, reliability, and overall performance.
b. Accreditation and Certifications: Verify that the chosen inspection company holds relevant accreditations and certifications from recognized organizations such as the China National Accreditation Service (CNAS) or the International Organization for Standardization (ISO). These certifications validate their adherence to international quality standards.
c. Apparel-Specific Knowledge: Ensure that the inspection company possesses specialized knowledge and expertise in the apparel industry. They should be familiar with industry-specific quality standards, garment construction techniques, and common defects encountered in the manufacturing process.
d. Comprehensive Inspection Services: Select a company that offers a wide range of inspection services, including visual inspections, measurements, functional tests, and compliance checks. Comprehensive inspections enable a thorough evaluation of various aspects of garment quality.
3. Preparing for Quality Inspections:
To maximize the effectiveness of pre-shipment inspections conducted by third-party companies, apparel manufacturers should take the following steps:
a. Clearly Define Quality Standards: Establish comprehensive and precise quality standards that align with customer expectations. Provide the inspection company with detailed specifications, including design elements, materials, measurements, stitching requirements, and labeling instructions.
b. Collaborate with Suppliers: Foster open communication and collaboration with suppliers to ensure they understand and adhere to the defined quality standards. Regularly share customer feedback and encourage suppliers to implement proactive quality control measures throughout the production process.
c. Strategic Inspection Scheduling: Plan inspections at appropriate stages of production to allow sufficient time for any necessary corrections. Early-stage inspections can identify issues before significant resources are invested, while final inspections ensure that the finished garments meet quality expectations.
4. Executing Pre-Shipment Inspections:
During the pre-shipment inspection process, the third-party inspection company should perform the following key tasks:
a. Random Sampling: Select a statistically significant sample size from the production lot to ensure a representative evaluation of the entire batch. Random sampling minimizes the risk of biased results and provides a realistic assessment of overall product quality.
b. Visual Inspection: Thoroughly examine each garment for defects, including fabric flaws, color discrepancies, stitching irregularities, misaligned patterns, loose threads, and incomplete labeling. Evaluate the overall appearance and workmanship of the garments.
c. Measurement and Functional Tests: Verify that the garments meet the specified measurements and conduct functional tests as required. This includes assessing zipper functionality, button strength, colorfastness, and any other specific requirements outlined in the quality standards.
d. Compliance Checks: Ensure that the garments comply with relevant industry regulations, safety standards, and any specific legal requirements for the target market. This includes verifying the presence of proper labeling, care instructions, and adherence to international trade regulations.
e. Documentation and Reporting: The inspection company should provide comprehensive reports detailing the findings of the inspection, including any defects or non-compliance issues identified. These reports serve as valuable documentation for manufacturers to address any quality issues and make necessary improvements.
5. Acting on Inspection Results:
Upon receiving the inspection report, apparel manufacturers should take prompt action to address any identified quality issues. This may involve working closely with suppliers to rectify the defects, implementing corrective measures in the production process, or even rejecting and replacing defective garments. The goal is to ensure that only high-quality products are shipped to customers, minimizing the risk of customer complaints and product returns.
6. Continuous Improvement:
To maintain consistent apparel quality, it is crucial to view pre-shipment inspections as part of an ongoing quality improvement process. Manufacturers should use the insights gained from inspections to identify trends, recurring issues, and areas for improvement. By implementing corrective actions and sharing feedback with suppliers, manufacturers can work towards enhancing overall product quality and customer satisfaction.
Utilizing third-party inspection companies in China for pre-shipment inspections is an effective strategy to control apparel quality and minimize the occurrence of defective products. By carefully selecting reliable inspection partners, clearly defining quality standards, and actively collaborating with suppliers, manufacturers can enhance their quality control processes. These inspections provide valuable insights, allowing manufacturers to address any identified defects before shipping, thus avoiding customer complaints and safeguarding their brand reputation in the competitive apparel industry.