Quality assurance plays a crucial role in ensuring that products meet the specified standards and requirements set by clients. In many industries, third-party inspectors are employed to assess and verify the quality of goods before they are shipped to customers. However, there are instances when these inspectors discover that a significant portion of the products do not meet the client’s requirements. This situation presents challenges and requires careful consideration of how to proceed. In this article, we will explore the steps and strategies that third-party inspectors can take when faced with non-conforming goods.
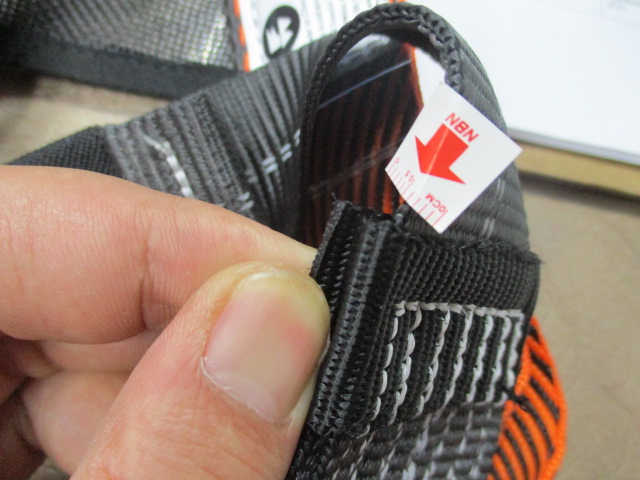
Contents
- 1 1.Understanding Non-Conforming Goods
- 2 2.Document the Findings
- 3 3.Verify the Requirements
- 4 4.Evaluate the Impact
- 5 5.Notify the Client
- 6 6.Collaborate with the Supplier
- 7 7.Determine Corrective Actions
- 8 8.Implement Preventive Measures
- 9 9.Reassessment and Reinspection
- 10 10.Seek Client Approval
- 11 Conclusion
1.Understanding Non-Conforming Goods
Non-conforming goods are products that do not meet the agreed-upon specifications, standards, or quality expectations set by the client. These goods may exhibit defects, deviations, or deficiencies that can compromise their intended use or functionality. When third-party inspectors encounter non-conforming goods during their assessment, it is essential to follow a systematic approach to address the situation.
2.Document the Findings
The first step when discovering non-conforming goods is to thoroughly document the findings. This documentation should include detailed descriptions of the defects or discrepancies observed, along with photographic evidence if possible. Accurate documentation is crucial for transparent communication with all stakeholders involved, including the client, supplier, and relevant parties within the inspection agency.
3.Verify the Requirements
Before taking any further actions, it is vital to double-check the client’s requirements and specifications. This ensures that the non-conformities are indeed deviations from the agreed-upon standards and not a misunderstanding or miscommunication. If there are any uncertainties, consult with the client to clarify the expectations and confirm the validity of the findings.
4.Evaluate the Impact
Once the non-conforming goods have been identified and the requirements verified, it’s time to assess the impact of the deviations. Determine whether the observed defects render the products unusable, pose safety risks, or affect their overall functionality. This evaluation helps in categorizing the severity of the non-conformities and guides the decision-making process.
5.Notify the Client
Communication is key when dealing with non-conforming goods. The next step is to promptly inform the client about the discrepancies that have been identified. Present the findings clearly and objectively, providing all relevant information, including the extent of the non-conformities and their potential impact. Open and transparent communication demonstrates professionalism and a commitment to resolving the issue.
6.Collaborate with the Supplier
Engaging with the supplier is essential to address non-conforming goods effectively. Reach out to the supplier to share the inspection findings and discuss possible causes for the deviations. Collaboration can help in understanding whether the issues are due to production processes, raw materials, or other factors. Work together to determine the root causes and develop a plan for corrective actions.
7.Determine Corrective Actions
Corrective actions are measures taken to rectify the non-conformities and prevent their recurrence. Collaborate with the supplier to identify appropriate corrective actions, which could involve reworking the products, replacing defective parts, or adjusting production processes. The goal is to bring the products back into compliance with the client’s requirements.
8.Implement Preventive Measures
In addition to corrective actions, preventive measures should be established to prevent similar non-conformities in the future. This might include improving quality control processes, enhancing supplier communication, conducting more rigorous inspections, or refining production protocols. Preventive measures are crucial for maintaining consistent product quality over the long term.
9.Reassessment and Reinspection
After the corrective actions have been implemented, it’s essential to reassess and reinspect the goods to ensure that the non-conformities have been effectively addressed. This step verifies whether the products now meet the client’s requirements and ensures that the issues have been resolved before proceeding with shipment.
10.Seek Client Approval
Before finalizing any decisions, obtain the client’s approval regarding the proposed corrective actions and the revised products. Transparency and collaboration remain critical throughout this process. Client approval indicates that they are satisfied with the resolution and are willing to accept the products, even after the non-conformities were identified.
Conclusion
Dealing with non-conforming goods as a third-party inspector requires a systematic and collaborative approach. Transparent communication, accurate documentation, thorough evaluation, and effective corrective actions are key components of managing this challenging situation. By following these steps, third-party inspectors can help ensure that quality standards are upheld, client expectations are met, and products are delivered according to specifications. Through dedication to quality assurance, the industry can continue to build trust and maintain high standards of product excellence.