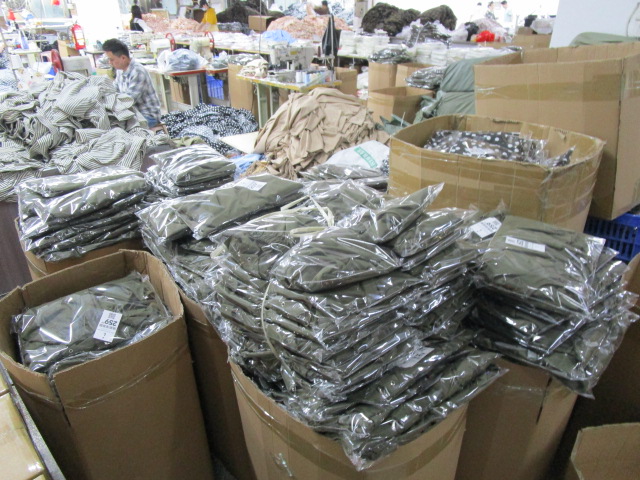
Container loading supervision plays a crucial role in ensuring the integrity and safety of goods during the shipping process. NBNQC, a leading third-party inspection service provider in China, specializes in quality control and inspection services, including container loading supervision. In this article, we will discuss some common problems that may arise during container loading and provide effective solutions to address them.
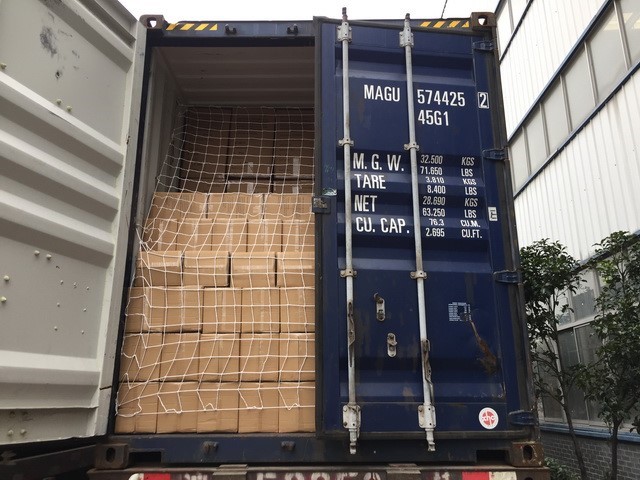
Contents
1.Insufficient Space Utilization:
Problem: Improper space utilization within the container can result in inefficient loading, leading to additional costs and potential damage to the goods.
Solution:
a. Proper Planning: Ensure that the cargo dimensions and weight are considered during the planning phase to optimize space utilization.
b. Professional Loaders: Trained and experienced loaders can efficiently arrange the cargo within the container, maximizing space utilization without compromising safety.
2.Inadequate Securing of Cargo:
Problem: Insufficient or improper securing of cargo within the container can cause shifting, collapse, or damage during transit.
Solution:
a. Quality Packaging: Ensure that goods are adequately packaged and protected to withstand the rigors of transportation.
b. Secure Lashing and Bracing: Implement proper lashing and bracing techniques to prevent cargo movement. Use dunnage bags, straps, or other suitable materials to secure the load effectively.
c. Use of Load Bars and Corner Protectors: Utilize load bars and corner protectors to create stability and prevent damage to the cargo.
3.Incorrect Weight Distribution:
Problem: Uneven weight distribution within the container can lead to instability, which may result in container tipping, cargo shifting, or damage during transportation.
Solution:
a. Balanced Loading: Distribute the weight evenly throughout the container, considering the load capacity and container specifications.
b. Placement of Heavier Items: Place heavier items at the bottom and closer to the center of the container to maintain stability.
c. Use of Load Cells: Implement load cells to accurately measure the weight distribution and ensure compliance with safety regulations.
4.Insufficient Documentation and Labeling:
Problem: Inadequate documentation and labeling can lead to delays, customs issues, and misplaced or lost shipments.
Solution:
a. Accurate Documentation: Ensure all necessary shipping documents, such as packing lists, bills of lading, and customs documentation, are complete and accurate.
b. Clear and Visible Labels: Use standardized labeling systems to identify the cargo accurately, including details such as weight, dimensions, and handling instructions.
c. Barcoding and RFID: Implement barcoding and radio-frequency identification (RFID) systems for efficient tracking and identification of cargo.
5.Poor Communication and Coordination:
Problem: Lack of effective communication and coordination among the various stakeholders involved in the loading process can result in errors, delays, and misunderstandings.
Solution:
a. Clear Instructions: Provide detailed loading instructions to the personnel involved, emphasizing the importance of following proper procedures.
b. Regular Communication: Maintain open lines of communication among the shippers, loaders, and supervisors throughout the loading process to address any issues promptly.
c. On-site Supervision: Assign a qualified supervisor to oversee the loading operations, ensuring adherence to the prescribed guidelines and resolving any conflicts or concerns.
Container loading supervision is a critical aspect of ensuring the safe and efficient transportation of goods. By addressing common issues such as space utilization, cargo securing, weight distribution, documentation, and communication, companies can mitigate risks, reduce costs, and maintain the integrity of their shipments. NBNQC, with its expertise in container loading supervision, continues to play a vital role in facilitating smooth and secure global trade operations.