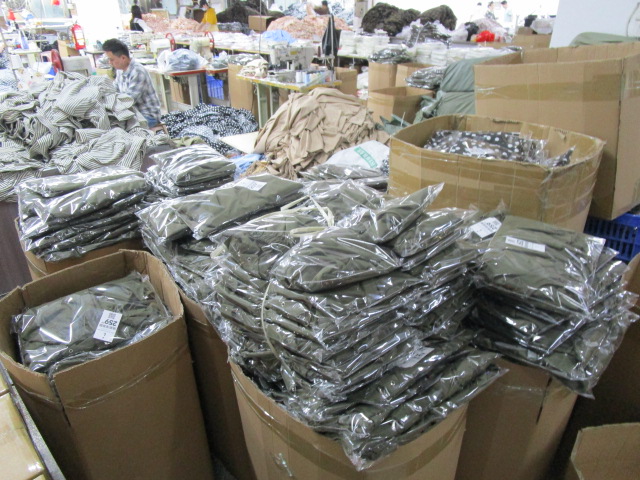
Quality control is a paramount concern for manufacturers striving to deliver products that meet or exceed customer expectations. One quality control method that garners attention is the 100% inspection process, wherein every single item produced is thoroughly examined. However, the effectiveness of this process hinges on the establishment and adherence to well-defined quantitative inspection standards. These standards guide inspectors in evaluating product conformity and help identify deviations that might otherwise go unnoticed.
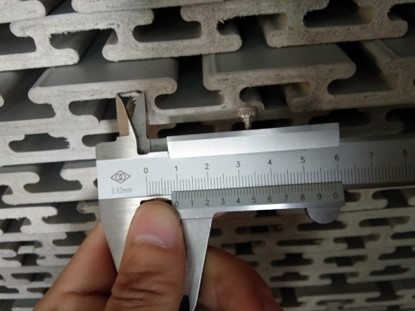
Contents
Benefits of Quantitative Inspection Standards:
1.Uniform Criteria: Quantitative inspection standards provide a uniform set of criteria against which each product is evaluated. This ensures consistency and fairness in assessments, reducing the risk of subjective judgments that might arise in the absence of clear benchmarks.
2.Defect Detection: Establishing specific measurement parameters and tolerances allows for the early detection of defects or variations. This preemptive identification helps prevent the accumulation of flawed products, thus minimizing wastage and rework.
3.Consistency in Output: Consistent application of quantitative standards aids in maintaining a steady output quality. By identifying and rectifying deviations promptly, manufacturers can ensure that product quality remains high throughout the production process.
4.Customer Satisfaction: High-quality products enhance customer satisfaction and brand reputation. Quantitative inspection standards contribute to the delivery of products that consistently meet customer expectations, fostering loyalty and positive reviews.
5.Process Improvement: The data collected during 100% inspections, guided by quantitative standards, offer valuable insights into production processes. Analysis of these data can lead to process improvements, driving efficiency and reducing defects in the long run.
Challenges in Establishing Quantitative Inspection Standards:
1.Complexity of Products: Some products have intricate designs or multifaceted functionalities that make it challenging to define universal quantitative standards. Striking a balance between comprehensive criteria and practical applicability is a persistent challenge.
2.Dynamic Industry Standards: Industries are subject to evolving regulations and technological advancements. Inspection standards must remain adaptable to these changes to remain effective and relevant.
3.Resource Intensiveness: Developing comprehensive quantitative standards demands significant resources, including time, expertise, and access to specialized equipment. Smaller manufacturers might face constraints in this regard.
4.Human Error: The human element in the inspection process introduces the potential for errors, both in assessing products against standards and in maintaining the standards themselves.
Real-world Applications:
1.Automotive Industry: In the automotive sector, 100% inspection is essential to ensure the safety and reliability of vehicles. Quantitative standards for components such as brakes, airbags, and electronic systems help identify even the slightest deviations that could compromise performance.
2.Electronics Manufacturing: With the rapid pace of technological advancement, electronics manufacturers rely on stringent quantitative inspection standards to catch defects in miniaturized components. This is vital to prevent malfunctions and potential safety hazards.
3.Pharmaceuticals: In the pharmaceutical industry, the application of 100% inspection coupled with rigorous quantitative standards ensures the quality and safety of medications. Deviations in dosage, packaging, or labeling can have serious consequences, making stringent standards imperative.
4.Food Production: Quantitative inspection standards play a critical role in the food industry to maintain consistent quality, prevent contamination, and adhere to regulations. From measuring ingredient ratios to checking for foreign particles, these standards safeguard consumers.
Conclusion:
The establishment of robust quantitative inspection standards is undeniably crucial in the process of 100% inspection. Such standards provide a foundation for consistent evaluations, timely defect detection, and ongoing process improvement. While challenges like product complexity and evolving industry norms exist, the benefits in terms of customer satisfaction, reduced defects, and enhanced brand reputation make the endeavor worthwhile. Across industries, from automotive to pharmaceuticals, these standards serve as a cornerstone of effective quality control, ensuring that each product leaving the production line meets the highest standards of excellence.