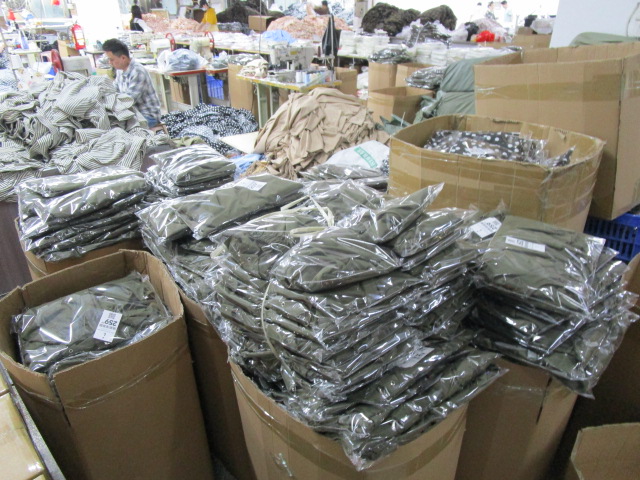
NBNQC is a trusted provider of apparel quality inspection services in China, catering to global clients. Committed to upholding industry standards, we play a vital role in ensuring that garments meet the highest quality requirements before shipment. In this article, we’ll explore our approach to pre-shipment inspection based on the DIN40080 standard, focusing on the process of sampling, measuring, recording, and ultimately determining the overall size accuracy of an entire order.
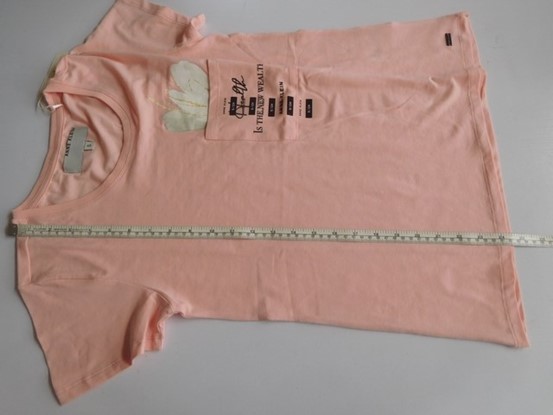
Contents
- 1 1. The Importance of Pre-shipment Inspection in Apparel Quality Assurance
- 2 2. Sampling Methodology According to DIN40080 Standard
- 3 3. Precise Measurement and Recording of Garment Dimensions
- 4 4. Determining the Overall Size Accuracy of the Entire Order
- 5 5. Ensuring Quality Assurance and Customer Satisfaction
- 6 Conclusion
1. The Importance of Pre-shipment Inspection in Apparel Quality Assurance
In the competitive apparel industry, meeting customer expectations and delivering top-notch products are essential for sustained success. Pre-shipment inspection is crucial in quality assurance, as it provides manufacturers with an opportunity to identify and rectify potential defects or discrepancies before the garments are shipped to customers. Ensuring accurate garment dimensions is particularly important, as it directly impacts fit, comfort, and customer satisfaction.
2. Sampling Methodology According to DIN40080 Standard
To efficiently assess the size accuracy of an entire production batch, we follow the DIN40080 standard, a widely accepted guideline in the apparel industry. Our approach involves random sampling to ensure a representative selection of garments for inspection.
Our sampling methodology includes the following steps:
a. Sample Size Determination: We calculate the appropriate sample size using statistical methods, considering factors such as the total order quantity, desired confidence level, and acceptable margin of error. This statistical approach ensures that the sample accurately represents the overall production lot.
b. Random Selection: To maintain an unbiased assessment, we randomly select garments from the production lot for inclusion in the sample. This randomization minimizes the risk of skewed results and ensures a fair representation of the entire batch.
3. Precise Measurement and Recording of Garment Dimensions
Accurate measurement of garment dimensions is crucial for evaluating size consistency and identifying any discrepancies. We employ various measurement tools and techniques to ensure precision.
The measurement and recording process includes the following steps:
a. Measurement Tools: We use non-stretchable tape measures, calipers, rulers, and gauges to measure critical dimensions such as length, width, height, and seam allowances.
b. Recording Process: Each garment in the sample is assigned a unique identifier, such as a SKU or production batch number, to distinguish it from others. We meticulously record the measured dimensions of each garment to facilitate data analysis and traceability.
c. Digital Documentation: We leverage digital recording systems to maintain organized and easily accessible records, enhancing efficiency and accuracy in data management.
4. Determining the Overall Size Accuracy of the Entire Order
After measuring and recording the sample garments, we determine the overall size accuracy of the entire order. This assessment involves comparing the measured dimensions of the sampled garments against the approved specifications provided by the client or international size standards.
Our determination process includes the following steps:
a. Statistical Analysis: We perform a statistical analysis on the collected measurement data to identify any patterns or trends that may indicate size discrepancies.
b. Tolerance Threshold: The measured dimensions are compared to the acceptable tolerance limits specified by the client or industry standards. Any deviations beyond the acceptable range are flagged for further evaluation.
c. Decision Making: Based on the evaluation results, we provide manufacturers with crucial insights into the size accuracy of the order. If the garments meet the required standards, the shipment can proceed. However, if significant discrepancies are identified, corrective action may be necessary before shipment.
5. Ensuring Quality Assurance and Customer Satisfaction
In cases where size discrepancies are detected, we collaborate closely with manufacturers to address the issues and ensure quality assurance. Our ultimate goal is to deliver garments that meet or exceed customer expectations.
Actions taken to ensure quality assurance include:
a. Reworking: If size discrepancies are within an acceptable range, we may recommend reworking the affected garments to bring them into compliance.
b. Replacement: In some instances, replacing non-compliant garments with new ones that meet the required size specifications may be necessary.
c. Process Improvement: We provide valuable feedback and recommendations to manufacturers to improve their production processes and prevent size inconsistencies in future orders.
Conclusion
Pre-shipment inspection is a crucial step in ensuring apparel quality and customer satisfaction. Our commitment to adhering to the DIN40080 standard for random sampling, precise measurement, and meticulous recording of garment dimensions ensures that global clients receive high-quality products with accurate size specifications. Through collaboration and continuous improvement, we work together with manufacturers to enhance apparel quality, meet industry standards, and exceed customer expectations on a global scale. With a dedication to excellence, we contribute to the success and reputation of apparel manufacturers in the competitive marketplace.