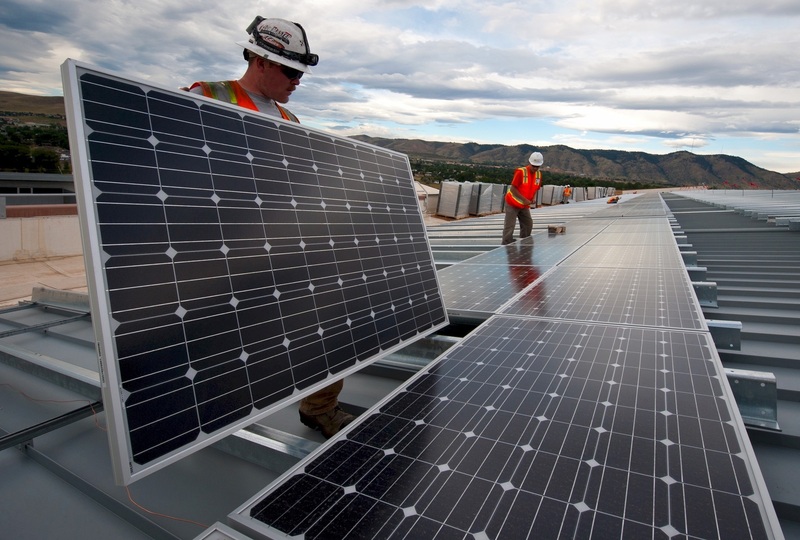
Mechanical components are critical elements of various industries, ranging from automotive and aerospace to manufacturing and construction. The quality and precision of these components directly impact the performance, reliability, and safety of the systems they are part of. Therefore, it is essential to conduct thorough inspections to ensure the integrity and functionality of mechanical parts. In this article, we will explore mechanical component inspection and quality control, including quality, dimension, surface characteristics and material properties.
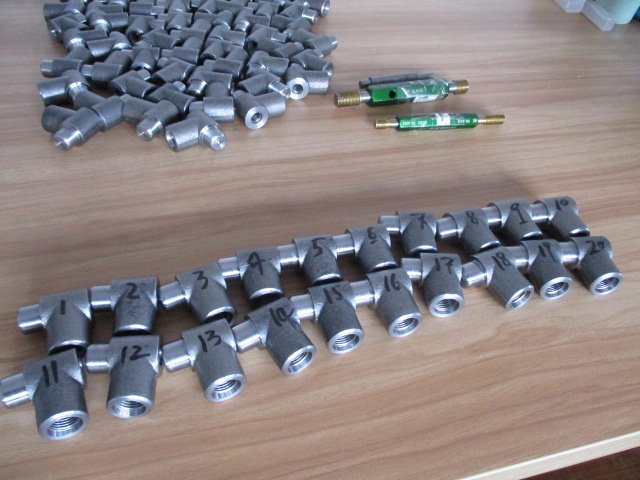
Contents [hide]
I. Visual Inspection:
- External Examination:
Visual inspection involves a detailed examination of the component’s external features. Inspectors look for surface defects such as cracks, scratches, corrosion, and unevenness. This examination provides a quick assessment of the component’s overall condition.
- Dimensional Verification:
Inspectors use measuring tools such as calipers, micrometers, and gauges to check critical dimensions of the component against the specifications provided. This ensures that the component meets the required tolerances and fits properly within the assembly.
II. Non-Destructive Testing (NDT):
- Ultrasonic Testing (UT):
UT uses high-frequency sound waves to detect internal defects or inconsistencies in materials. A transducer sends ultrasonic waves through the component, and any reflected waves indicate the presence of flaws such as cracks, voids, or inclusions. UT is particularly effective for assessing the integrity of metallic and composite components.
- Magnetic Particle Testing (MT):
MT is used to detect surface and near-surface defects in ferromagnetic materials. The component is magnetized, and magnetic particles are applied to the surface. The particles gather at areas of magnetic flux leakage caused by defects, making them visible under appropriate lighting conditions.
- Dye Penetrant Testing (PT):
PT is utilized to identify surface defects such as cracks, porosity, or leaks in non-porous materials. A liquid dye penetrant is applied to the surface, and after a specified time, excess dye is removed. A developer is then applied, causing the trapped dye to migrate and become visible, indicating the presence of defects.
- Radiographic Testing (RT):
RT employs X-rays or gamma rays to inspect the internal structure of components. The radiation penetrates the material, and a radiographic film or digital sensor captures the resulting image. This technique is particularly effective for detecting internal defects such as voids, inclusions, or weld discontinuities.
III. Coordinate Measuring Machine (CMM):
CMM is a highly precise measuring instrument used to assess dimensional accuracy and geometric characteristics of components. It employs a probing system to measure points on the component’s surface and records their spatial coordinates. The collected data can be compared to the CAD model or specifications to verify the component’s conformance.
IV. Material Testing:
- Hardness Testing:
Hardness testing determines the resistance of a material to indentation or deformation. Techniques such as Rockwell, Brinell, or Vickers hardness tests are conducted to evaluate the hardness properties of the component. This provides insights into the material’s strength, wear resistance, and durability.
- Tensile Testing:
Tensile testing measures the mechanical properties of a material under tension. A sample of the component is subjected to controlled forces until it reaches its breaking point. This test helps assess the material’s ultimate tensile strength, yield strength, elongation, and other mechanical characteristics.
V. Surface Finish Inspection:
Surface finish evaluation involves measuring and analyzing the texture, roughness, and surface characteristics of the component. Instruments such as profilometers or optical devices are used to quantify parameters such as Ra (average roughness), Rz (mean peak-to-valley height), and Rq (root mean square roughness). This inspection ensures that the component meets the required surface quality standards.
The inspection of mechanical components is crucial to ensure their quality, performance, and compliance with specifications. Visual inspection, non-destructive testing methods (UT, MT, PT, and RT), CMM measurements, material testing, and surface finish inspections collectively provide a comprehensive assessment of the component’s integrity, dimensions, material properties, and surface characteristics. By implementing these inspection techniques, manufacturers and industries can ensure the reliability, safety, and functionality of mechanical components in various applications.