Shrinkage in denim garments, particularly those predominantly made of cotton, is a common occurrence in the textile industry. As part of the garment inspection process, accurately measuring garment size and conducting shrinkage rate tests are crucial steps in ensuring product quality before shipment. Several factors contribute to the shrinkage of denim clothing, impacting its size and overall quality. Let’s delve into these factors and their implications for garment production and quality control.
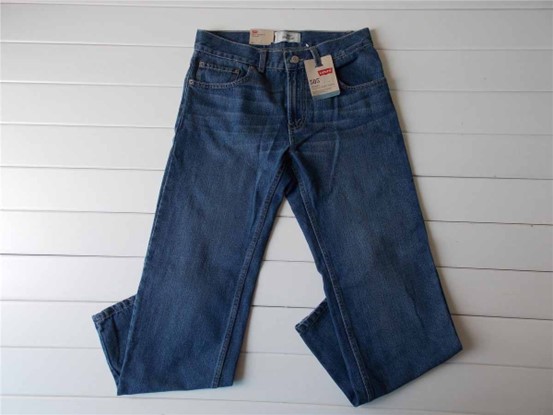
Main Factors Affecting Denim Garment Size
- Fabric Shrinkage: Denim fabric undergoes various processing techniques such as washing, rinsing, sand washing, and pickling to achieve desired aesthetics and properties. Different washing methods directly influence fabric shrinkage, thereby affecting garment size. Consequently, it’s essential to consider fabric shrinkage rates when creating garment patterns to ensure accurate sizing during production.
- Weaving Direction: The weaving direction of denim fabric can significantly impact garment size. For instance, fabric shrinkage rates may vary depending on whether the weaving pattern is straight or twill. This variation can lead to discrepancies in garment dimensions, making it challenging to meet customer specifications. It’s imperative to account for weaving direction when determining fabric shrinkage rates and adjusting garment patterns accordingly.
- Thickness of Stitching and Folding: The thickness of seams and hems in denim garments can affect shrinkage uniformity. Uneven thickness in these areas may result in inconsistent shrinkage rates, leading to misalignment and sizing issues. Techniques such as ring hemming or binding and curling can exacerbate this problem, highlighting the importance of uniformity in garment construction to maintain size integrity.
- Other Production Processes: Beyond fabric shrinkage, factors such as fabric yarn direction, seam thickness, and post-washing treatments can influence garment size. Each stage of production, from cutting to finishing, introduces potential sources of size variation. Seamstress expertise and adherence to quality standards are crucial for minimizing these deviations and ensuring consistent garment sizing.
Understanding Denim Fabric Shrinkage
Denim fabric shrinkage is primarily attributed to natural, thermal, and water-induced factors:
- Natural Shrinkage: Fabric fibers undergo mechanical stress during weaving and processing, leading to potential strain and deformation. Factors such as fiber type, weaving technique, and storage conditions contribute to natural fabric shrinkage. Understanding these variables is essential for predicting and controlling fabric shrinkage in garment production.
- Thermal Shrinkage: Denim fabric exhibits thermoplastic behavior, causing it to shrink when exposed to high temperatures during production and ironing. The inherent properties of fabric fibers and the mechanical stress endured during processing contribute to thermal shrinkage. Careful temperature control is necessary to mitigate shrinkage-induced size variations in garments.
- Water Shrinkage: Absorption of water by denim fabric results in anisotropic expansion, causing fibers to swell and fabric thickness to increase. This water-induced expansion leads to shrinkage upon drying, known as water shrinkage or simply shrinkage. The fabric’s hygroscopic properties dictate the extent of water shrinkage, with higher moisture absorption capacities correlating to greater shrinkage rates.
Conclusion
Shrinkage in denim garments is influenced by a combination of factors spanning fabric properties, production techniques, and environmental conditions. Understanding these factors is essential for effectively controlling garment size and ensuring quality consistency throughout the manufacturing process. By addressing fabric shrinkage rates, weaving direction, seam thickness, and other production variables, manufacturers can minimize size discrepancies and deliver garments that meet customer expectations for fit and quality.