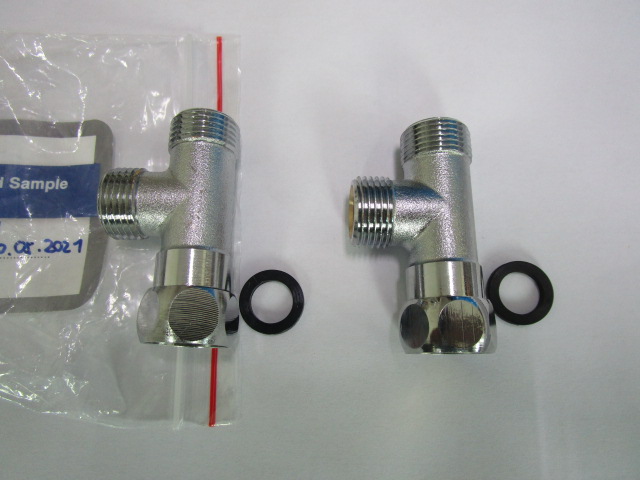
Food-grade plastics are crucial in the food and beverage industry as they ensure the safety and quality of packaged products. These plastics are designed to minimize the risk of chemical leaching and contamination, making them suitable for direct contact with consumable items. They are categorized into various classes based on their properties, suitability, and regulatory compliance. This article discusses the different types of food-grade plastics, the relevant international standards, and the methods used to inspect and verify the quality of food-grade plastic products.
Contents
Types of Food-Grade Plastics:
- Polyethylene (PE): PE is one of the most common food-grade plastics. It comes in various densities, including high-density polyethylene (HDPE) and low-density polyethylene (LDPE). HDPE is known for its strength and rigidity, making it suitable for packaging milk, juices, and water. LDPE, on the other hand, is more flexible and is often used for squeeze bottles and packaging that requires some flexibility.
- Polypropylene (PP): PP is another widely used food-grade plastic known for its high melting point and excellent chemical resistance. It is commonly used for packaging hot foods, as well as for containers and utensils. PP is known for its microwave-safe properties.
- Polyethylene Terephthalate (PET): PET is commonly used for beverage bottles and food containers. It offers good barrier properties against moisture and oxygen, making it suitable for carbonated beverages and packaged foods. PET is recyclable and considered safe for single-use applications.
- Polyvinyl Chloride (PVC): PVC is used for a variety of food-grade applications, including cling film, food wraps, and some bottles. However, due to concerns about potential chemical leaching, PVC is less preferred for direct food contact and is being replaced by safer alternatives in certain applications.
- Polycarbonate (PC): PC is known for its transparency, making it suitable for items like water bottles and baby bottles. However, there have been concerns about the potential release of bisphenol A (BPA), a chemical used in the production of PC, which has led to a shift towards BPA-free alternatives.
- Polyamide (PA): PA, also known as nylon, is used for manufacturing food packaging films, pouches, and containers. It offers excellent barrier properties against oxygen and aromas, making it suitable for preserving the freshness of food.
International Standards for Food-Grade Plastics:
- FDA Regulation (USA): The United States Food and Drug Administration (FDA) regulates food-contact materials, including plastics. The Code of Federal Regulations (CFR) Title 21 outlines the rules for materials intended for contact with food. The FDA approves certain polymers and additives for use in food-contact applications based on their safety evaluations.
- EU Regulation (Europe): The European Union’s framework for food-contact materials is governed by Regulation (EC) No 1935/2004. This regulation ensures that materials do not transfer harmful substances to food and outlines specific migration limits for various types of plastics.
- Health Canada Regulation (Canada): Health Canada regulates food packaging materials through the Food and Drugs Act and its associated regulations. The agency sets guidelines for the safe use of food-contact materials, including plastics.
- JHOSPA (Japan): In Japan, the Japan Hygienic Olefin and Styrene Plastics Association (JHOSPA) establishes safety standards for olefin and styrene plastics used in food packaging. These standards ensure the materials’ suitability for food-contact applications.
Inspection Methods for Food-Grade Plastic Products:
- Visual Inspection: A visual assessment of food-grade plastic products is essential to identify any visible defects, irregularities, or contamination. This includes checking for discoloration, scratches, and foreign particles.
- Migration Testing: Migration testing assesses whether harmful substances from the plastic material migrate into the food. This involves simulating contact conditions and analyzing the food for potential contaminants using advanced analytical techniques.
- Chemical Analysis: Advanced techniques such as gas chromatography-mass spectrometry (GC-MS) and liquid chromatography-mass spectrometry (LC-MS) can be employed to identify and quantify potential chemical contaminants in food-grade plastic products.
- Mechanical Testing: Mechanical tests evaluate the physical properties of plastic materials, including tensile strength, impact resistance, and flexibility. These tests ensure that the plastic maintains its integrity during use.
- Sensory Evaluation: Sensory evaluation involves assessing the taste, odor, and appearance of food that has come into contact with plastic packaging. Any off-flavors or odors can indicate potential contamination.
- Compliance with Standards: The plastic products must undergo tests to verify compliance with relevant international standards. These standards define permissible limits for migration of specific substances and set guidelines for overall safety.
Conclusion:
Food-grade plastics are vital components of the food and beverage industry, ensuring the safety and quality of packaged products. Different types of food-grade plastics offer unique properties suitable for various applications. International regulations, such as those set by the FDA, EU, Health Canada, and JHOSPA, ensure that food-contact materials, including plastics, adhere to strict safety standards. To ensure the quality and safety of food-grade plastic products, thorough inspection methods, including visual assessment, migration testing, chemical analysis, mechanical testing, sensory evaluation, and compliance with standards, are employed. These measures collectively contribute to the protection of consumer health and the maintenance of product quality in the food industry.