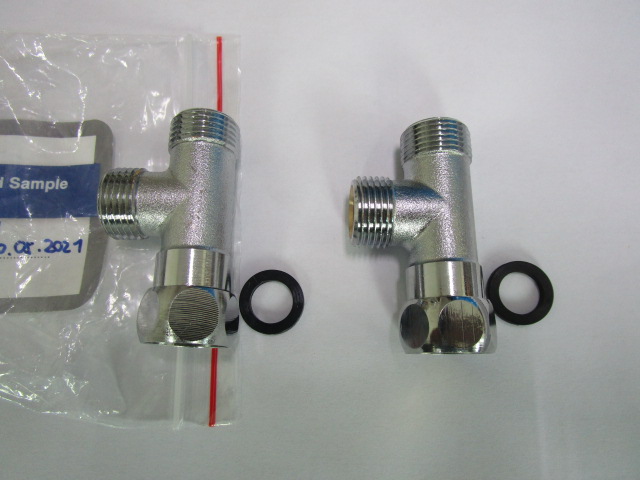
In the intricate world of manufacturing and production, the role of a resident inspector from a third-party inspection agency is critical for ensuring product quality and compliance with client specifications. These professionals serve as the eyes and ears of clients on the production floor, bridging the gap between product requirements and manufacturing processes. Their comprehensive understanding of production workflows and quality standards enables them to effectively monitor and guide the manufacturing process from inception to completion. This article delves into the responsibilities and workflow of resident inspectors, highlighting their indispensable role in maintaining product integrity.
Understanding the Role of the Resident Inspector
A resident inspector’s primary responsibility is to ensure that all aspects of production meet the client’s quality criteria. They achieve this through a meticulous process of monitoring, verifying, and reporting on various stages of production. By doing so, they not only safeguard the quality of the product but also facilitate timely interventions to correct any deviations from the set standards.
Key Responsibilities of the Resident Inspector
A. Routine Work Arrangement:
- Comprehensive Order Review: Inspectors start by thoroughly reviewing all order details, including designs, specifications, materials, and sample confirmations. Discrepancies between client expectations and supplier provisions are promptly addressed to ensure alignment.
- Assessment of Production Capabilities: Understanding the manufacturing facility’s strengths and weaknesses is crucial. Inspectors evaluate the plant’s capacity and quality control measures, preparing for potential challenges and formulating contingency plans.
- Continuous Communication: Maintaining open lines of communication with both the company’s quality department and the manufacturing plant is vital. This ensures that quality issues are minimized through collaborative efforts.
B. Quality Control Procedures in the Production Process:
- Raw Material Inspection: The inspector supervises the inventory and inspection of incoming raw materials, documenting any quality issues encountered.
- Monitoring Material Usage: Any deviation from the pre-determined material usage rates is reported to ensure efficient use of resources.
- Semi-Finished Product Checks: Early production stages are closely monitored, with semi-finished products inspected for compliance. Any issues are reported for immediate rectification.
- First Finished Product Review: The completion of the first item in each batch triggers a thorough inspection to establish benchmarks for subsequent production.
- Production Monitoring: Daily progress, finished product counts, and equipment productivity are meticulously recorded, ensuring adherence to the production schedule.
- Final Quality Assurance: Upon completion, a final inspection against shipping documents ensures that all products meet the required standards before dispatch.
Conclusion
The role of a resident inspector is paramount in upholding quality and ensuring that products meet the exacting standards demanded by clients. Through diligent oversight, precise communication, and proactive problem-solving, these professionals play a pivotal role in the seamless execution of production orders. By bridging the gap between client expectations and manufacturing realities, resident inspectors are indispensable allies in the pursuit of excellence in product quality and integrity.