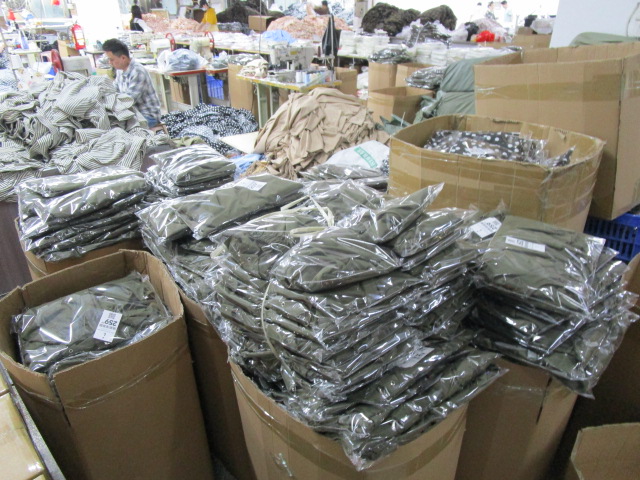
In the complex landscape of global trade, China stands as a pivotal manufacturing hub, offering a wealth of opportunities for international procurement. However, navigating this vast market requires a strategic approach to selecting suppliers that align with both product specifications and quality standards. This article explores the critical factors influencing supplier selection in China and the role of NBNQC in optimizing this process.
Key Factors in Choosing Suppliers in China
1. Experience and Reputation
The track record of a supplier is a testament to their reliability and operational maturity. Suppliers with extensive experience and a positive reputation in the industry are often better equipped to understand the nuanced demands of international clients. They are likely to have a history of successful projects and testimonials that vouch for their ability to deliver quality products consistently.
2. Manufacturing Capabilities
A supplier’s manufacturing capabilities are central to their ability to meet client demands. This includes not just the scale of their operations, but also the technology, machinery, and skilled labor they have at their disposal. Suppliers who invest in advanced manufacturing technologies and maintain flexible production lines can better accommodate custom orders and adapt to changing market trends.
3. Quality Control Measures
The quality of the end product is non-negotiable. Suppliers that implement stringent quality control measures at every stage of the production process are more likely to produce goods that meet international standards. This includes regular quality checks, from raw materials sourcing to the final product, ensuring that any issues are identified and addressed promptly.
4. Certifications and Compliance
Compliance with international standards and certifications (such as ISO, CE, or others relevant to specific industries) is crucial for ensuring that products are safe, reliable, and legally compliant. Suppliers with the appropriate certifications demonstrate a commitment to maintaining high standards in their operations and products.
5. Research and Development (R&D) Capabilities
Suppliers with robust R&D capabilities are valuable partners in innovation and product development. Their ability to design, test, and refine products can significantly shorten development cycles and bring competitive products to market faster.
The Role of NBNQC in Supplier Selection and Quality Assurance
NBNQC plays a pivotal role in ensuring that the supplier selection process is rigorous, transparent, and aligned with the client’s quality expectations.
1. Pre-Supplier Evaluation
Before engagement, NBNQC conducts comprehensive evaluations of potential suppliers. This assessment covers their financial stability, production capabilities, and adherence to quality standards, providing a solid foundation for informed decision-making.
2. Factory Audit
A detailed factory audit by NBNQC assesses the operational efficiency, quality control systems, and environmental and labor compliance of the supplier. This step is vital for verifying the supplier’s claims and getting an on-ground reality check.
3. Quality Inspections
NBNQC implements a series of quality inspections throughout the manufacturing process. These inspections are designed to identify and rectify defects early, ensuring that the final products meet the agreed-upon specifications and quality standards.
4. Sample Testing and Analysis
Through rigorous sample testing and analysis, NBNQC validates the quality, safety, and performance of products before mass production begins. This step is crucial for preventing costly recalls and ensuring product compliance with international standards.
5. Supplier Performance Monitoring
Continuous monitoring of supplier performance by NBNQC helps in identifying areas for improvement and ensuring consistent quality over time. This involves tracking delivery times, product quality, and response to issues, fostering a culture of continuous improvement.
In conclusion, the selection of suppliers in China’s competitive market is a multifaceted process that demands a strategic approach. By focusing on experience, manufacturing capabilities, quality control, certifications, and R&D capabilities, businesses can identify suppliers that are capable of meeting their needs. Furthermore, the involvement of NBNQC in pre-supplier evaluation, factory audits, quality inspections, sample testing, and supplier performance monitoring adds an additional layer of assurance, ensuring that the chosen suppliers not only meet but exceed expectations.