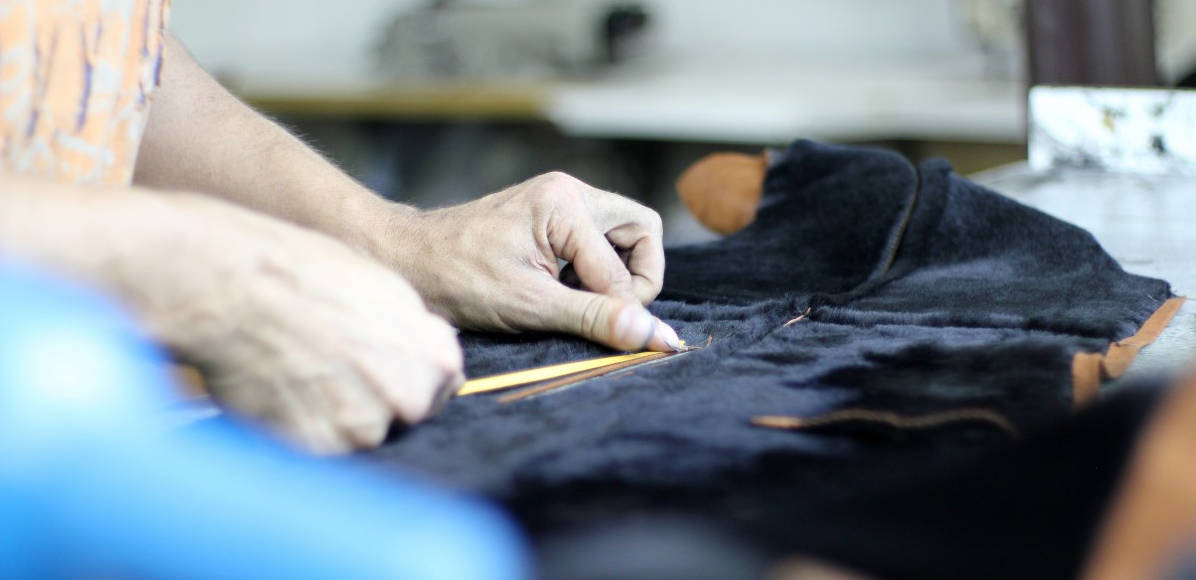
In the complex landscape of global trade and manufacturing, maintaining the highest standards of product quality is paramount for businesses aiming to sustain competitiveness and ensure customer satisfaction. One pivotal strategy companies employ to uphold these standards involves engaging third-party inspection services to conduct comprehensive evaluations of their products. Within this framework, “Client Requirements” emerge as a crucial element, tailoring the inspection process to address specific concerns or demands of the client. This article delves into the essence of Client Requirements in the context of third-party inspection services, highlighting their significance and operational dynamics.
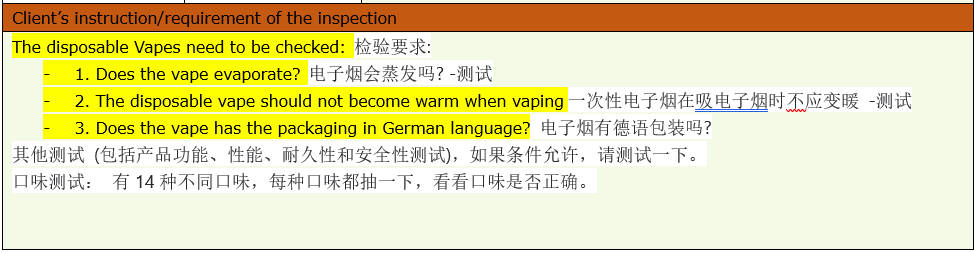
Contents
Understanding Client Requirements
Client Requirements refer to a set of specific, additional, or special inspection criteria requested by a client, supplementing the standard inspection protocols. These requirements are typically derived from unique product specifications, industry standards, regulatory mandates, or quality benchmarks that are critical to the client’s market positioning and brand reputation. The primary objective of incorporating Client Requirements is to ensure that the products not only meet generic quality standards but also align perfectly with the client’s specific quality expectations and operational necessities.
The Role of Client Requirements
- Customized Quality Assurance: Client Requirements enable businesses to customize the inspection process, ensuring that it precisely addresses their unique quality concerns, product specifications, and market needs.
- Regulatory Compliance: For products subject to strict regulatory standards, Client Requirements help ensure compliance with local, national, or international regulations, mitigating the risk of legal issues and market entry barriers.
- Brand Protection: By ensuring products meet both standard and bespoke quality criteria, businesses can protect their brand integrity, foster consumer trust, and maintain a competitive edge in the market.
- Risk Mitigation: Tailoring inspections to address specific risks associated with materials, production processes, or supply chains helps in proactively identifying and mitigating potential product failures or defects.
Operationalizing Client Requirements
The process of integrating Client Requirements into third-party inspections involves several key steps:
- Requirement Identification: The client identifies and documents specific inspection criteria, standards, or concerns that transcend standard inspection protocols. This often involves collaboration between quality assurance teams, product managers, and legal advisors to ensure all relevant quality and regulatory aspects are covered.
- Communication and Agreement: These detailed requirements are then communicated to the third-party inspection service provider. The provider reviews the requirements to assess feasibility, resource implications, and potential impacts on inspection timelines. Any clarifications or adjustments are discussed and agreed upon at this stage.
- Implementation Planning: The third-party inspector incorporates the Client Requirements into the inspection plan, outlining methodologies, tools, and techniques to be used in assessing these additional criteria. This plan also specifies how findings related to these requirements will be reported.
- Execution: During the inspection, the third-party inspector meticulously evaluates the product against both the standard inspection criteria and the specified Client Requirements. Special attention is given to these additional points to ensure no aspect is overlooked.
- Reporting and Feedback: The inspection report includes a detailed section on the Client Requirements, documenting the findings, any non-conformities, and recommendations for improvement. This allows clients to make informed decisions regarding product acceptance, adjustments, or further actions.
- Continuous Improvement: Feedback from the inspection process, particularly regarding the Client Requirements, is used to refine future inspections and quality control processes, ensuring they remain aligned with the client’s evolving needs and industry standards.
Conclusion
Client Requirements play a pivotal role in the realm of third-party inspections, offering businesses a tailored approach to quality assurance that aligns with their specific needs, regulatory obligations, and market expectations. By effectively integrating these requirements into the inspection process, companies can achieve superior product quality, safeguard their brand reputation, and foster trust among their customer base. The collaboration between clients and third-party inspection services in identifying, implementing, and refining these requirements is fundamental to continuous quality improvement and market success.