In the realm of product quality control and inspection, Acceptance Quality Limit (AQL) is a crucial parameter. It helps businesses determine the maximum number of defective items that can be considered acceptable in a sample lot. AQL is particularly essential in assessing workmanship quality, ensuring that products meet the desired standards before reaching the consumer. This article explores AQL, its implementation in random sampling inspection, and the entire process involved.
Contents
What is AQL?
Acceptance Quality Limit (AQL) refers to the worst tolerable process average (mean) in percentage or ratio that is still considered acceptable. It defines a quality level that is the base of a systematic sampling method for ongoing production. The primary purpose of AQL is to instruct inspectors on the level of defects that can be tolerated during an inspection. If the defects exceed the AQL, the lot fails the inspection.
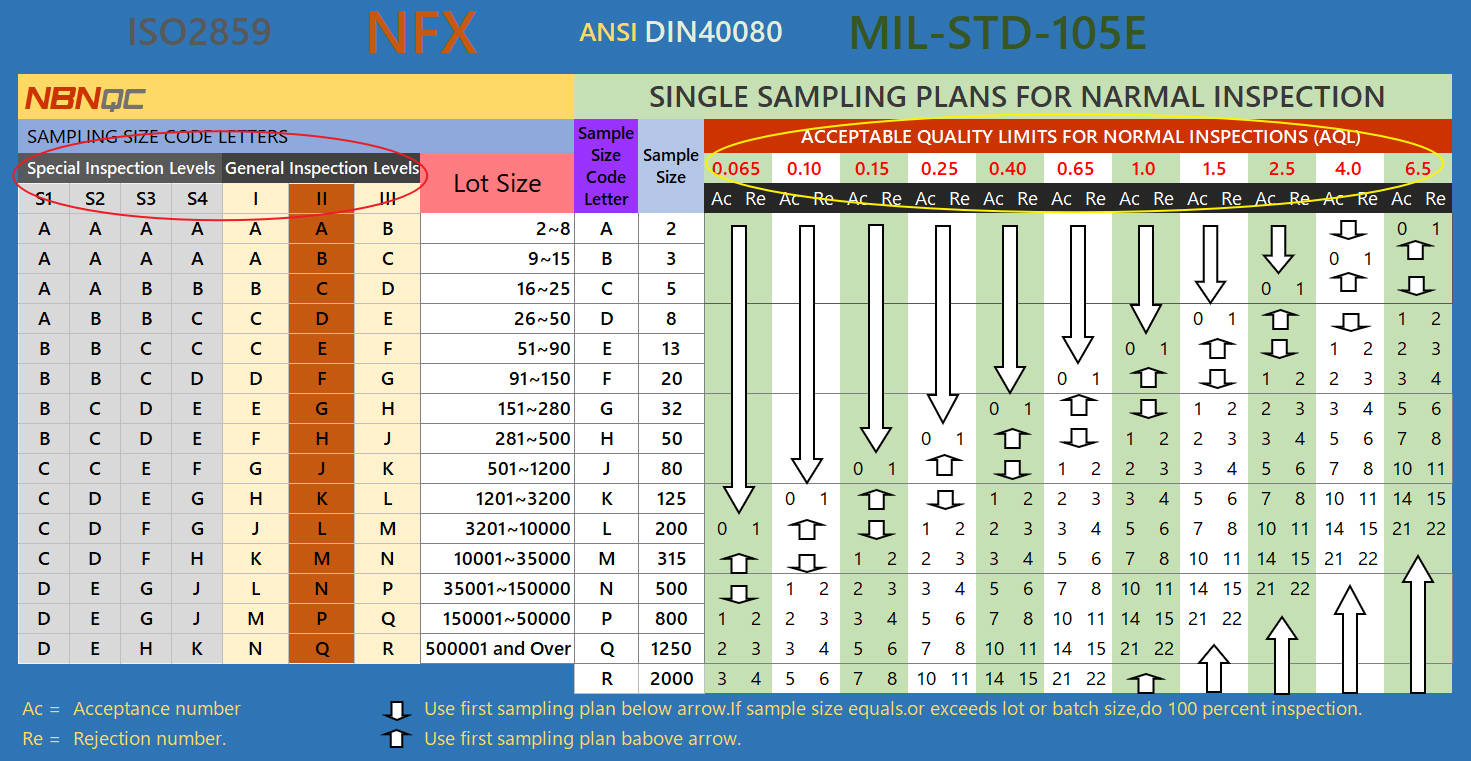
The AQL Sampling Process
The AQL inspection process involves several key steps:
1.Determine the Lot Size: The first step is to identify the total number of units in the batch that needs inspection.
2.Select the AQL Standard: Based on the criticality of defects (critical, major, or minor), choose an AQL value. Common AQL values are 1.5, 2.5, and 4.0 for major defects, with lower values indicating higher quality requirements.
3.Identify the Sample Size: Utilize AQL sampling tables to determine the sample size for inspection. These tables are based on the lot size and the chosen AQL level, giving you a code letter which corresponds to a specific sample size.
4.Conduct Random Sampling: Randomly select the quantity of units specified by the sample size from the lot. It’s crucial that the selection is random to ensure the sample accurately represents the entire lot.
5.Inspect the Sampled Units: Examine the selected units for defects. Each defect found is categorized as critical, major, or minor, according to predefined criteria focusing on workmanship.
6.Evaluate Results Against AQL: Compare the number of defects found to the acceptable number determined by the AQL. If the number of defects is within the AQL limit, the lot passes; otherwise, it fails.
Implementing AQL for Workmanship Quality Inspection
When inspecting for workmanship quality using AQL, the focus is on material finishes, assembly quality, and overall appearance. Inspectors must be trained to identify and classify defects accurately. The AQL criteria should be clearly defined in inspection manuals or guidelines to ensure consistency.
The Importance of Random Sampling
Random sampling is vital in the AQL process. It eliminates bias and ensures that the sample accurately reflects the quality of the entire lot. Techniques such as random number generation or systematic selection from a randomized starting point can be used to select samples.
AQL in Action: An Example
Consider a batch of 1000 units with an AQL of 2.5 for major defects. According to AQL tables, this might require a sample size of 80 units. If, upon inspection, the number of units with major defects is equal to or less than the acceptable number (determined by the AQL level), the batch passes. Otherwise, it fails, indicating a need for quality improvement.
The Role of AQL Tables and Charts
AQL tables and charts are essential tools in this process. They guide users in determining the appropriate sample size and the acceptable number of defects. These tables are standardized and widely available in quality control references and standards.
Conclusion
AQL is a fundamental aspect of quality control, providing a systematic approach to determine the acceptability of product lots. Through random sampling and inspection, AQL helps maintain workmanship quality, ensuring that products meet consumer expectations and industry standards. Proper implementation of AQL in the inspection process is crucial for maintaining product quality and brand reputation.