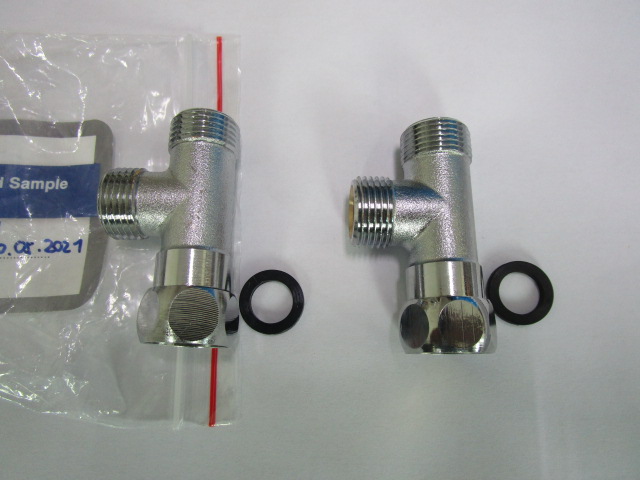
Electroplating is a sophisticated surface finishing process used across various industries to enhance the properties of metal parts. This process involves coating a thin layer of metal onto the surface of another metal through electrochemical deposition. The resulting electroplated components boast improved corrosion resistance, increased electrical conductivity, enhanced appearance, and extended service life. Given the critical role these components play in automotive, aerospace, electronics, and decorative applications, meeting stringent quality requirements and undergoing thorough inspection are paramount. This article explores the quality standards and inspection processes essential for ensuring the integrity and performance of electroplated parts.
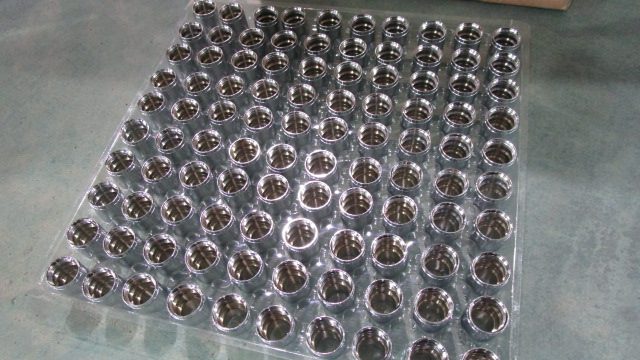
Contents
Quality Requirements for Electroplated Parts
The quality of electroplated parts is gauged by several key parameters that directly influence their performance, durability, and appearance. These parameters include:
- Thickness of the Coating: The coating thickness must meet the specifications for the intended application to ensure adequate protection and functionality.
- Adhesion Strength: The electroplated layer must firmly adhere to the substrate to prevent peeling or chipping under mechanical stress or environmental exposure.
- Uniformity: The coating should be evenly distributed across the part’s surface, without significant variations in thickness.
- Absence of Defects: Quality electroplated parts should be free from cracks, blisters, pits, and other surface imperfections that could impair their performance or aesthetic appeal.
- Corrosion Resistance: The coating should provide effective protection against corrosion, particularly for parts used in harsh environments.
- Electrical Conductivity: For electrical applications, the electroplated layer must meet specific conductivity requirements to ensure reliable performance.
Inspection Techniques for Electroplated Parts
To verify that electroplated parts meet these quality requirements, a series of inspections and tests are conducted, ranging from visual assessments to sophisticated analytical techniques.
Visual Inspection
Visual inspection is the first line of defense in identifying surface defects such as blisters, pits, and uneven coating. Inspectors look for inconsistencies in appearance and finish, which could indicate underlying issues with the electroplating process.
Thickness Measurement
Coating thickness is a critical quality attribute that is often measured using non-destructive techniques such as X-ray fluorescence (XRF), magnetic induction, and eddy current methods. These technologies allow for accurate and rapid thickness assessments without damaging the part.
Adhesion Testing
Adhesion tests evaluate the bond strength between the electroplated layer and the substrate. Common methods include the tape test, bend test, and pull-off test, each designed to apply mechanical stress to the coating in different ways to assess its adhesion properties.
Corrosion Resistance Testing
To assess the corrosion resistance of electroplated parts, salt spray (fog) testing is widely used. This test exposes the parts to a saline mist environment for a specified period, after which they are evaluated for signs of corrosion.
Hardness Testing
The hardness of the electroplated layer can be an indicator of its wear resistance. Hardness testing, often conducted using Vickers or Rockwell hardness scales, measures the resistance of the coating to indentation.
Electrical Conductivity Testing
For parts used in electrical applications, testing the electrical conductivity of the electroplated layer ensures that it meets the necessary performance criteria. This involves measuring the resistance of the coating and comparing it to established standards for the specific application.
Dimensional inspection and others
Since electroplated parts are mechanical components, their complete inspection process is the same as that for mechanical parts inspection.
Challenges in Inspecting Electroplated Parts
Inspecting electroplated parts presents several challenges, including the need for specialized equipment and expertise to accurately assess the various quality parameters. Furthermore, the diversity of electroplating processes and materials adds complexity to the inspection process, requiring adaptable and versatile inspection strategies.
Best Practices in Electroplated Part Inspection
Adopting best practices in inspection is crucial for maintaining the quality of electroplated parts. This includes regular calibration of measurement and testing equipment, training inspectors to recognize and evaluate defects accurately, and implementing standardized procedures for each type of inspection to ensure consistency and reliability.
Conclusion
The quality of electroplated parts is critical to their performance and reliability in their final applications. Through meticulous attention to quality requirements and the implementation of comprehensive inspection processes, manufacturers can ensure that their electroplated components meet the highest standards. As technology advances, so too will the methods for inspecting and ensuring the quality of these essential components, helping industries to deliver products that are not only aesthetically pleasing but also durable and reliable.