Contents
Introduction
Table tennis, also known as ping pong, is a beloved sport enjoyed by millions worldwide. The table tennis racket, a critical piece of equipment, directly influences a player’s performance. Therefore, ensuring the quality and performance of table tennis rackets is paramount. This article outlines the quality requirements and provides detailed pre-shipment inspection procedures for table tennis rackets to uphold quality standards and meet customer expectations.
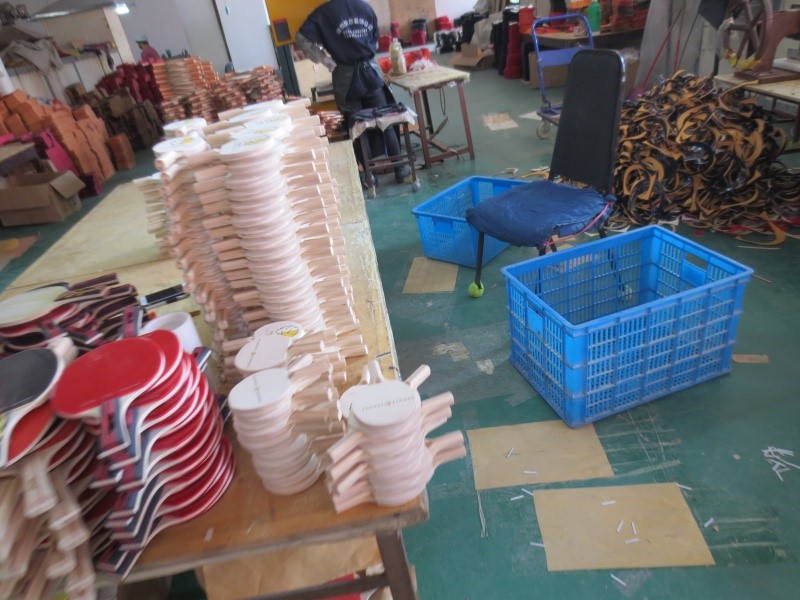
Quality Requirements
1. Blade Quality:
- Material Composition: The blade should be crafted from high-quality wood or composite materials, ensuring durability, resilience, and optimal ball response.
- Surface Finish: The blade’s surface must be smooth, free from defects, and uniformly finished to ensure consistent ball trajectory and bounce.
- Handle Comfort: The handle grip should be ergonomically designed for comfort and provide a secure grip during intense gameplay.
2. Rubber Quality:
- Pips Integrity: The rubber pips on both sides of the racket must be uniform in size, shape, and density to ensure consistent ball contact and spin generation.
- Rubber Thickness: The thickness of the rubber sheet should adhere to International Table Tennis Federation (ITTF) regulations for fair play and consistent performance.
- Adhesive Strength: The bond between the rubber and the blade should be strong and durable, preventing detachment or peeling during gameplay.
3. Overall Construction:
- Weight Balance: The racket must be well-balanced, with even weight distribution between the blade and handle, enabling precise control and maneuverability.
- Edge Tape Condition: The edge tape must be securely applied to the blade to protect the edges from damage and maintain the racket’s structural integrity.
- Handle Stability: The handle must be securely attached to the blade, with no signs of looseness or instability during gameplay.
Detailed Pre-Shipment Inspection Procedures
1. Visual Inspection:
- Blade Examination: Visually inspect the blade for any visible defects, cracks, warping, or irregularities in the surface finish.
- Rubber Assessment: Examine the rubber surfaces closely for uniformity, smoothness, and any signs of wear, damage, or irregularities in the pips.
2. Measurement and Testing:
- Thickness Measurement: Use calipers or a thickness gauge to measure the thickness of the rubber sheet, ensuring compliance with ITTF regulations.
- Weight Balance Test: Utilize a precision weighing scale to assess the weight distribution of the racket and ensure proper balance.
- Handle Grip Evaluation: Test the comfort, grip, and ergonomics of the handle by simulating gameplay conditions and evaluating user experience.
3. Performance Testing:
- Ball Rebound Test: Perform a ball rebound test to evaluate the consistency and responsiveness of the racket’s surface, ensuring optimal ball control and spin generation.
- Spin and Speed Assessment: Assess the racket’s ability to generate spin and speed by conducting controlled strokes and observing the ball’s trajectory and behavior.
4. Adhesive Strength Evaluation:
- Pull Test: Apply controlled force to the rubber sheet to assess the adhesive strength between the rubber and the blade, ensuring secure bonding and preventing detachment.
5. Compliance Verification:
- ITTF Regulations: Verify compliance with ITTF regulations regarding size, weight, material specifications, and other relevant standards.
- Quality Standards: Ensure adherence to internal quality standards and customer requirements for product excellence and customer satisfaction.
6. Documentation and Reporting:
- Record Keeping: Maintain detailed records of inspection results, including measurements, observations, and any deviations from quality standards.
- Reporting: Prepare comprehensive inspection reports summarizing the findings, highlighting any issues or recommendations for corrective actions or further evaluation.
7. Post-Inspection Follow-Up:
- Quality Assurance: Implement quality assurance measures to address any identified issues and ensure consistent product quality.
- Customer Feedback: Solicit feedback from customers to assess satisfaction levels and identify areas for improvement in product quality and performance.
Conclusion
In conclusion, rigorous pre-shipment inspection procedures are essential for maintaining the integrity and quality of table tennis rackets. By adhering to quality requirements and conducting thorough inspections, manufacturers can ensure that their products meet regulatory standards, customer expectations, and industry benchmarks. Continuous monitoring, feedback, and improvement initiatives are vital for sustaining product excellence and customer satisfaction in the competitive market of table tennis equipment.