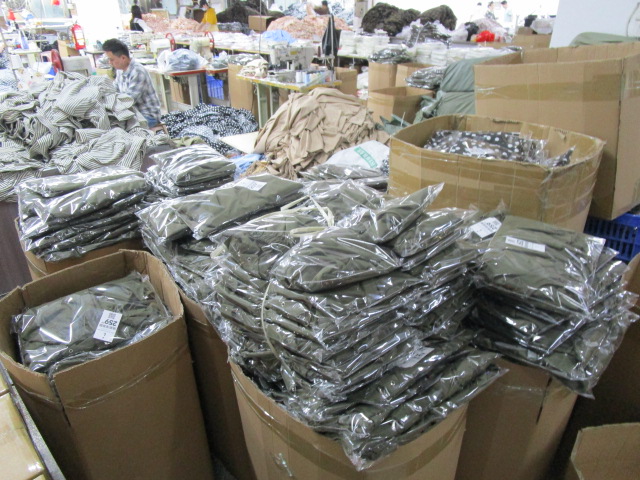
Introduction
External rotor motors play a crucial role in various industrial applications, ranging from HVAC systems to household appliances. Ensuring the quality of these motors is essential to maintain performance, reliability, and safety standards. This article delves into the quality requirements and detailed inspection procedures for external rotor motors to meet industry standards and ensure optimal functionality.
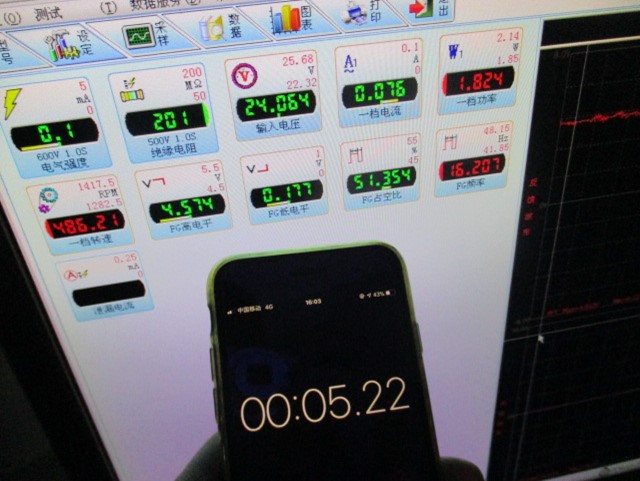
Quality Requirements
1. Material Quality:
- Core Material: The core material should meet specified magnetic and mechanical properties to ensure efficient operation and durability.
- Coil Insulation: Insulation materials must withstand high temperatures and voltage stresses to prevent electrical breakdowns.
2. Mechanical Precision:
- Rotor Balance: Precise balancing of the rotor is crucial to minimize vibrations and ensure smooth operation, especially at high speeds.
- Bearing Tolerance: Bearings must meet tolerance specifications to reduce friction, prevent overheating, and prolong the motor’s lifespan.
3. Electrical Performance:
- Efficiency: Motors should operate with high efficiency to minimize energy consumption and reduce operational costs.
- Insulation Resistance: Insulation resistance tests are conducted to ensure protection against electrical faults and prevent short circuits.
4. Safety Standards:
- Overload Protection: Motors should incorporate overload protection mechanisms to prevent damage from excessive currents or sudden voltage surges.
- Enclosure Rating: Enclosures must meet specified ingress protection (IP) ratings to safeguard against dust, moisture, and other environmental factors.
Detailed Inspection Procedures
1. Visual Inspection:
- Exterior: Inspect for any physical damage, corrosion, or irregularities in the motor casing and components.
- Labeling: Verify that all labels, nameplates, and markings are legible and comply with regulatory requirements.
2. Dimensional Checks:
- Rotor Diameter: Measure the diameter of the rotor to ensure it matches the specified dimensions.
- Shaft Alignment: Check the alignment of the rotor shaft with respect to the motor housing to prevent misalignment issues.
3. Electrical Testing:
- Insulation Resistance: Conduct insulation resistance tests using a megohmmeter to verify the integrity of insulation materials.
- Winding Resistance: Measure the resistance of motor windings to ensure consistency and detect any abnormalities.
4. Performance Evaluation:
- Load Testing: Apply various loads to the motor and measure parameters such as torque, speed, and current draw to assess performance under different operating conditions.
- Efficiency Measurement: Calculate the motor’s efficiency by comparing input power with output power under standardized test conditions.
5. Vibration Analysis:
- Dynamic Balancing: Utilize vibration analysis techniques to identify and correct any imbalance in the rotor assembly.
- Frequency Spectrum Analysis: Analyze vibration signatures to detect potential faults such as bearing wear or misalignment.
Conclusion
Maintaining high-quality standards in external rotor motors is essential to ensure optimal performance, reliability, and safety. By adhering to stringent quality requirements and conducting detailed inspection procedures, manufacturers can deliver products that meet industry standards and customer expectations. Continuous improvement in design, manufacturing processes, and quality control measures is imperative to stay competitive in the dynamic market of external rotor motors.